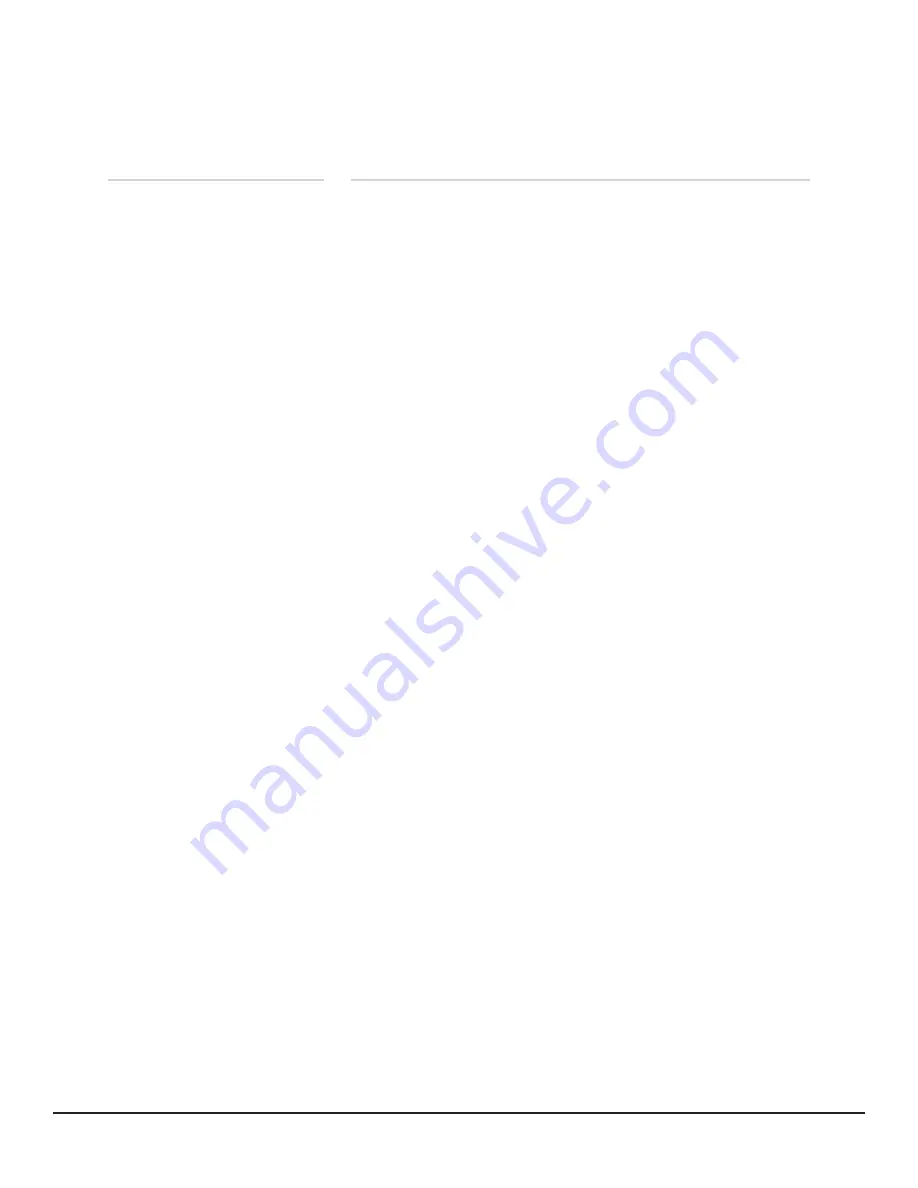
3-13
Operation
STARTING A RUN
Action
Result
1. Check that all parameters
are correct and the door is
firmly closed.
2. Press
_78%68a
.
The display will start showing actual centrifuge values within
5 seconds. The LED on the
_78%68a
key flashes during acceleration.
When set speed is reached, the light stays on continuously until the
centrifuge begins decelerating.
As the run begins, the system identifies the installed rotor. The system
verifies that the user-selected rotor and the installed rotor are the
same.
If the system detects that the installed rotor is not the rotor that the
user selected with the ROTOR knob, and the speed selected by the
user is
greater
than the installed rotor’s maximum permitted speed,
the system will reduce the run speed to the maximum allowed for the
installed rotor.
CHANGING PARAMETERS DURING A RUN
While a run is in progress, the speed, time, temperature, and accelera-
tion or deceleration setting can be changed without stopping the run.
The following parameters cannot be changed during a run:
• The rotor name.
• After acceleration starts, the acceleration setting cannot be
changed.
• After deceleration starts, the deceleration setting cannot be
changed.