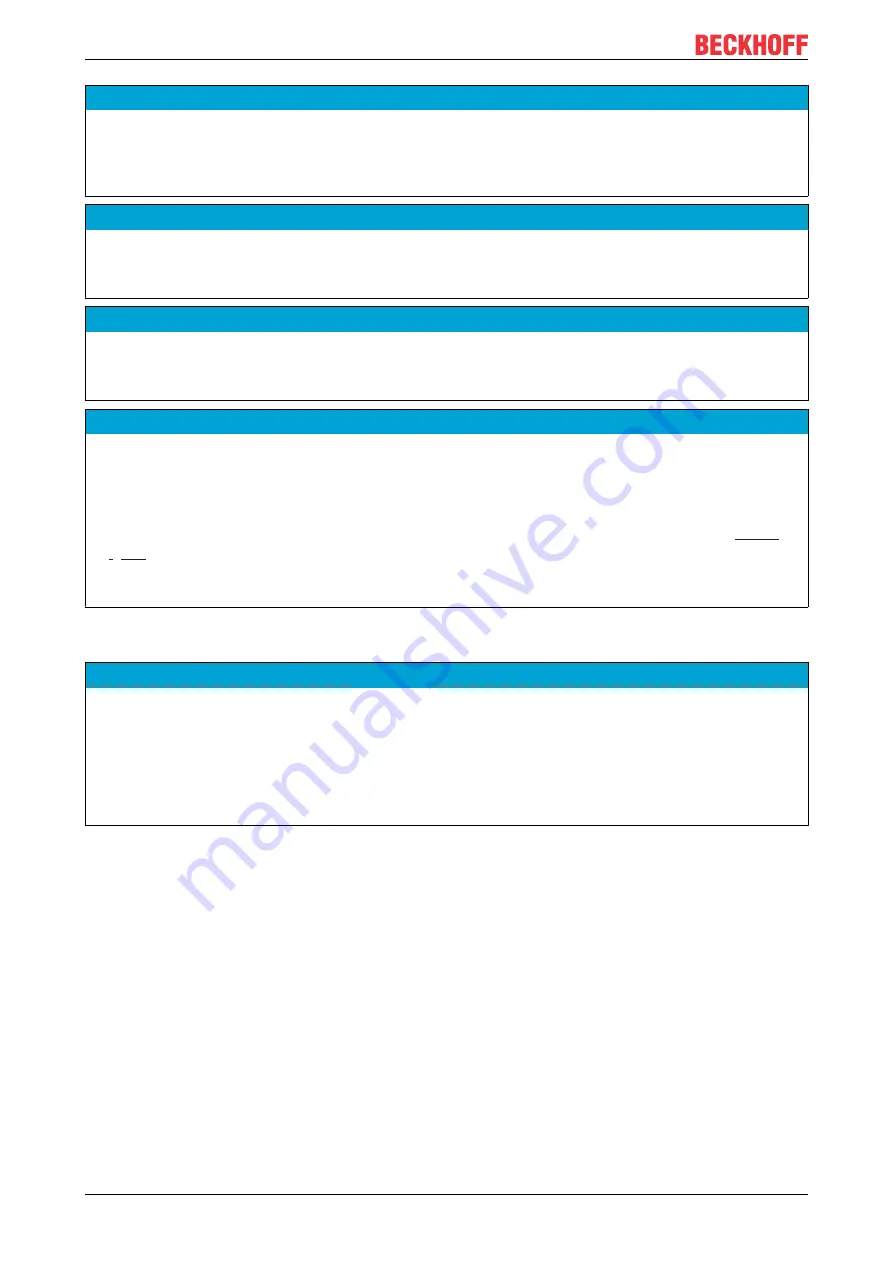
Mounting and wiring
ELX3312 and ELX3314
18
Version: 1.3.0
NOTE
Protect the terminals against electrostatic discharge (ESD)
Electronic components can be destroyed by electrostatic discharge. Therefore, take the safety measures to
protect against electrostatic discharge as described in DIN EN 61340-5-1 among others. In conjunction with
this, ensure that the personnel and surroundings are suitably earthed.
NOTE
Do not place terminals on E-bus contacts
Do not place the ELX terminals on the E-bus contacts located on the right-hand side. The function of the E-
bus contacts can be negatively affected by damage caused by this, e.g. scratches.
NOTE
Protect the terminals against dirt
To ensure the functionality of the ELX terminals they must be protected against dirt, especially on the con-
tact points. For this reason use only clean tools and materials.
NOTE
Handling
• It is forbidden to insert conductive or non-conductive objects of any kind into the interior of the housing
(e.g. through the ventilation slots in the housing).
• Use only the openings provided in the housing front and appropriate tools to actuate the spring-loaded
terminal contacts on the front side for attaching connection cables to the terminal; see chapter
• The opening of the housing, the removal of parts and any mechanical deformation or machining of an
ELX terminal are not permitted!
If an ELX terminal is defective or damaged it must be replaced by an equivalent terminal. Do not carry out
any repairs to the devices. For safety reasons repairs may only be carried out by the manufacturer.
NOTE
Contact marking and pin assignment
The colored inscription labels above the front connection contacts shown in the illustrations in the introduc-
tion chapter are only examples and are not part of the scope of delivery!
A clear assignment of channel and terminal designation according to the chapter contact assignment to the
actual terminal point can be made via the lasered channel numbers 1 to 8 on the left above the respective
terminal point as well as via the laser image.
Observe any possible polarity dependency of connected intrinsically safe circuits!