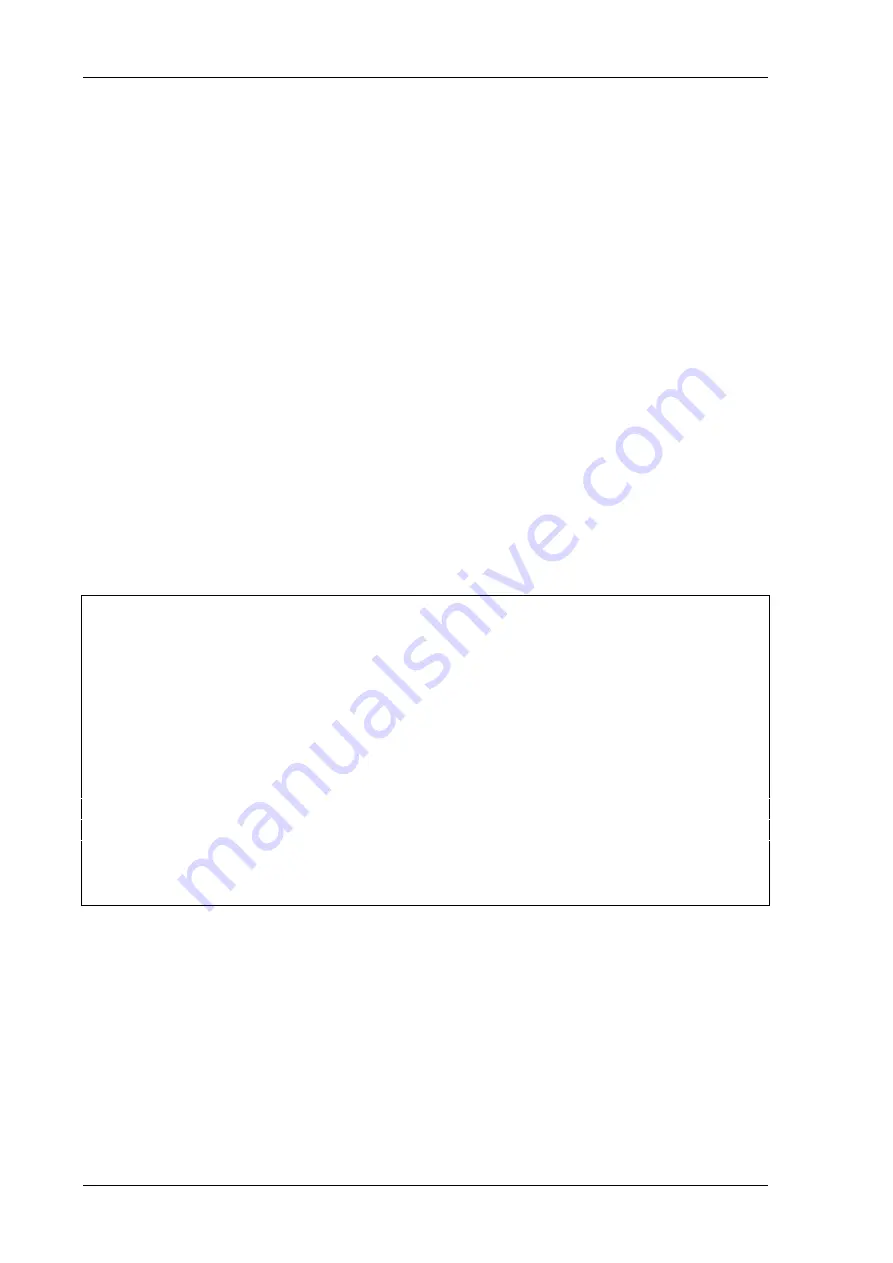
C1120 S5 to II/O-Lightbus Interface
Beckhoff II/O-Lightbus System
Page 10 of 52
Version 2.1
Date 27.06.97
To enlarge the I/O address space, the use of "indirect modules" is available - a list of
module
data fields is stored in the C1120 RAM memory. The base address to exchange data with the
Process image of the PLC is defined here (see equiv. chapter).
To obtain correct data for the PLC process image, the process image memory of the C1120 is
divided in pages, which each by each are switched towards the PLC and towards the II/O
Lightbus to refresh data contents. The pageswitch mechanism changes the memory pages to
and from the PLC. The pageswitch inputs are defined as lowest address, the pageswitch
outputs are defined as highest address by default.
By writing a "1" to the field "word alignment", the PLC is enabled to access the process
image by word commands (16 bit - wise) The necessary selects are generated automatically.
For use of more than one C1120, the word alignement can be disabled by overwriting a "0".
The default setup value of "0" in the field "Error request" enables the C1120 to stop the PLC
with a timeout status of the C1120 in case errors occur on the II/O-Lightbus System, the
C1120 interface deletes the I/O addresses in the Dual Ported RAM mapped to the PLC in case
of error. By programming OB 23 and OB 28 the timeout can be managed by PLC software.
By setting the field value "Error request" to "1", the I/O addresses are not deleted in case of
errors. The latest input data values are held in place, the writing of outputs data is confirmed,
but writing is not executed, the error flag in the status byte is set.
IMPORTANT REMARK:
By use of option "1" the user has to achieve the check of the status byte error
flag in every PLC cycle to branch into a error routine, if the error flag is set.
After occurance of the error flag the fault number and number of modules can
be read via the parallel communication channel. After return from the fault
situation (repair of fiber optic media) a start of the II/O-Lightbus System can be
forced by resetting the C1120 by software from the PLC.
In case of no success of the reset function, the error flag is set again, and as a
return value of the function RESET-LWL the value of the init- error is returned
(refer to chapter "Parellel communication channel").