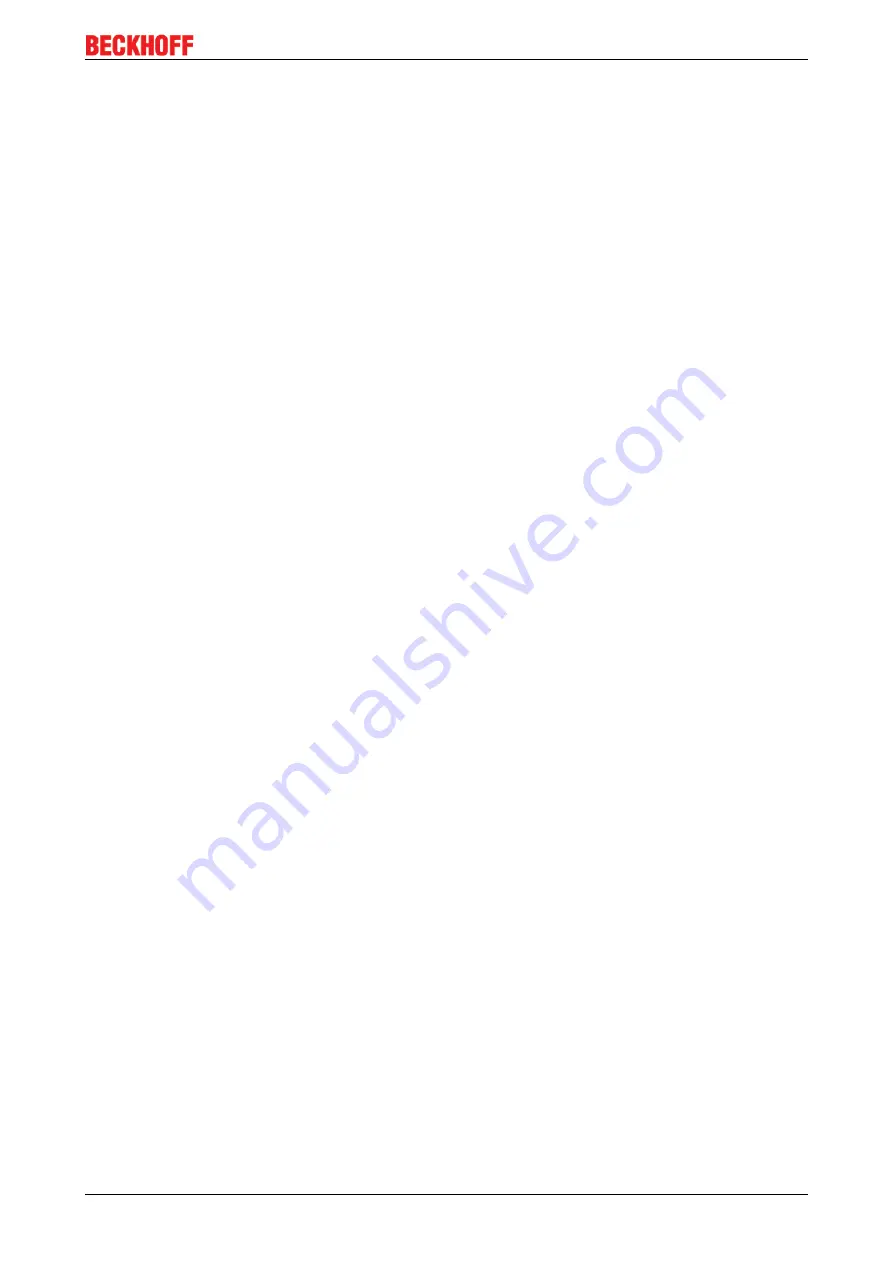
Parameterization and commissioning
BK3xx0
43
Version: 4.3.0
Configuration
You can configure the Fieldbus stations with the Configuration Software KS2000 offline. That means, setting
up a terminal station with all settings on the couplers and terminals resp. the Fieldbus Box Modules can be
prepared before the commissioning phase. Later on, this configuration can be transferred to the terminal
station in the commissioning phase by means of a download. For documentation purposes, you are provided
with the breakdown of the terminal station, a parts list of modules used and a list of the parameters you have
modified. After an upload, existing fieldbus stations are at your disposal for further editing.
Parameterization
KS2000 offers simple access to the parameters of a fieldbus station: specific high-level dialogs are available
for all bus couplers, all intelligent bus terminals and Fieldbus Box modules with the aid of which settings can
be modified easily. Alternatively, you have full access to all internal registers of the bus couplers and
intelligent terminals. Refer to the register description for the meanings of the registers.
Commissioning
The KS2000 software facilitates commissioning of machine components or their fieldbus stations: Configured
settings can be transferred to the fieldbus modules by means of a download. After a
login
to the terminal
station, it is possible to define settings in couplers, terminals and Fieldbus Box modules directly
online
. The
same high-level dialogs and register access are available for this purpose as in the configuration phase.
The KS2000 offers access to the process images of the bus couplers and Fieldbus Box modules.
• Thus, the coupler's input and output images can be observed by monitoring.
• Process values can be specified in the output image for commissioning of the output modules.
All possibilities in the
online mode
can be used in parallel with the actual fieldbus mode of the terminal
station. The fieldbus protocol always has the higher priority in this case.
4.4.7
Configuration via TwinCAT
The TwinCAT automation software is a complete automation solution for PC-compatible computers.
TwinCAT turns any compatible PC into a real-time controller, an IEC 61131-3 Multi-PLC, NC positioning
system, the corresponding programming environment and user interface. TwinCAT supports several different
PROFIBUS DP PC cards. Beckhoff recommends the PROFIBUS DP PCI master card FC3101, which can
also be obtained as a two-channel version (FC3102).
TwinCAT*System-Manager
The TwinCAT System Manager Tool is used to configure the FC310x PROFIBUS DP PCI card. The System
Manager provides a representation of the number of programs of the TwinCat PLC systems, the
configuration of the axis control and of the connected I/O channels as a structure, and organizes the
mapping of the data traffic.