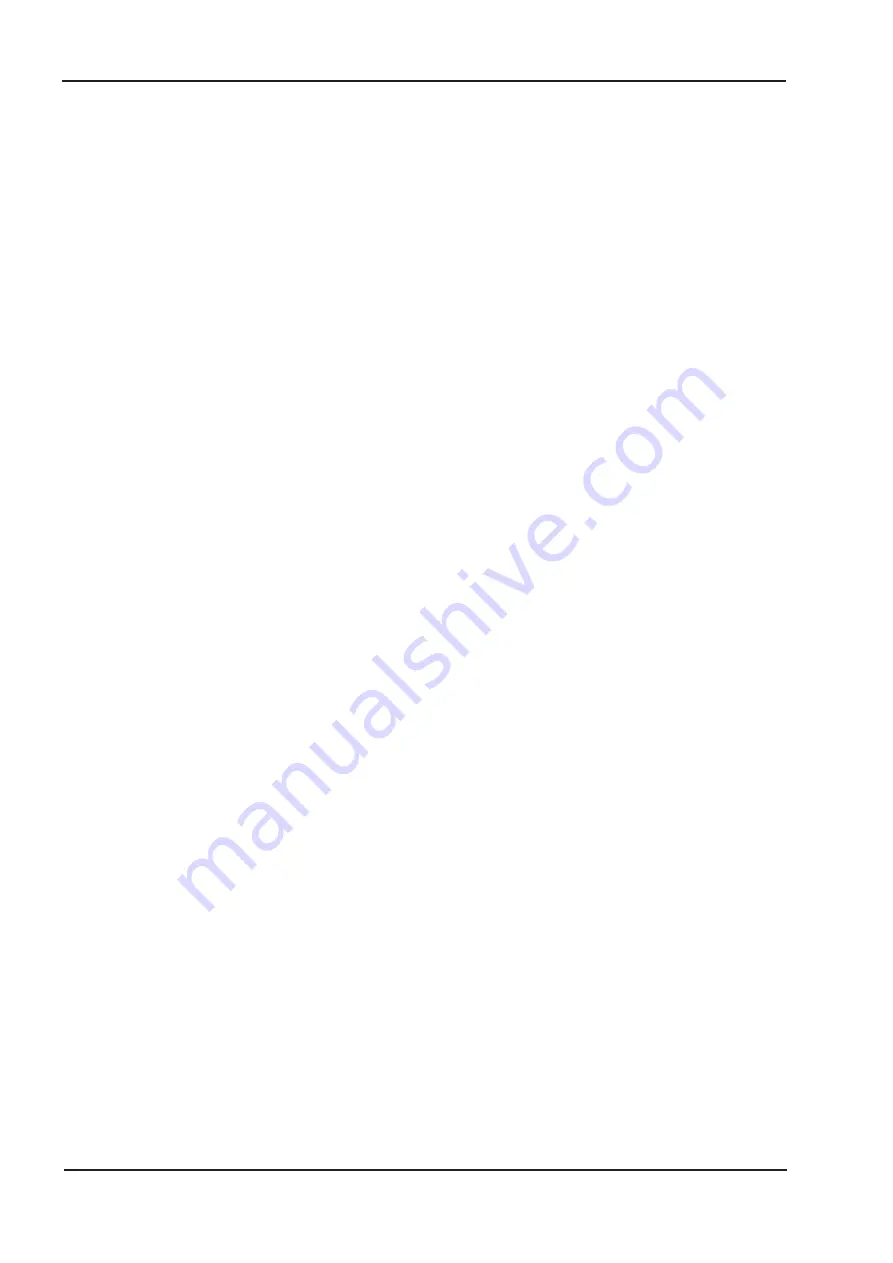
2.5
UL and cUL- Conformance
This servo amplifier is listed under UL file number
E217428
.
UL (cUL)-certified servo amplifiers (Underwriters Laboratories Inc.) fulfil the relevant U.S.
and Canadian standard (in this case UL 840 and UL 508C).
This standard describes the fulfilment by design of minimum requirements for electrically
operated power conversion equipment, such as frequency converters and servo ampli-
fiers, which is intended to eliminate the risk of fire, electric shock, or injury to persons,
being caused by such equipment.
UL(cUL) regulations also specify the minimum technical requirements of electrical devi-
ces, in order to take the necessary measures against the risk of fire, which can be trigge-
red by electrically operated devices. The technical conformance with the U.S. and Cana-
dian standard is determined by an independent UL (cUL) inspector through the type
testing and regular checkups.
Apart from the notes on installation and safety in the documentation, the customer does
not have to observe any other points in direct connection with the UL (cUL)-certification of
the equipment.
UL 508C
UL 508C describes the fulfilment by design of minimum requirements for electrically ope-
rated power conversion equipment, such as frequency converters and servo amplifiers,
which is intended to eliminate the risk of fire being caused by such equipment.
UL 840
UL 840 describes the fulfilment by design of air and insulation creepage spacings for
electrical equipment and printed circuit boards.
10
AX2500 Installation Manual
Technical description
02/06
Beckhoff
Summary of Contents for AX2500 Series
Page 31: ...3 4 4 Connector assignments AX2500 Installation Manual 31 Beckhoff 02 06 Installation...
Page 65: ...5 3 2 3 Status display on the master AX2500 Installation Manual 65 Beckhoff 02 06 Setup...
Page 68: ...This page has been deliberately left blank 68 AX2500 Installation Manual Setup 02 06 Beckhoff...