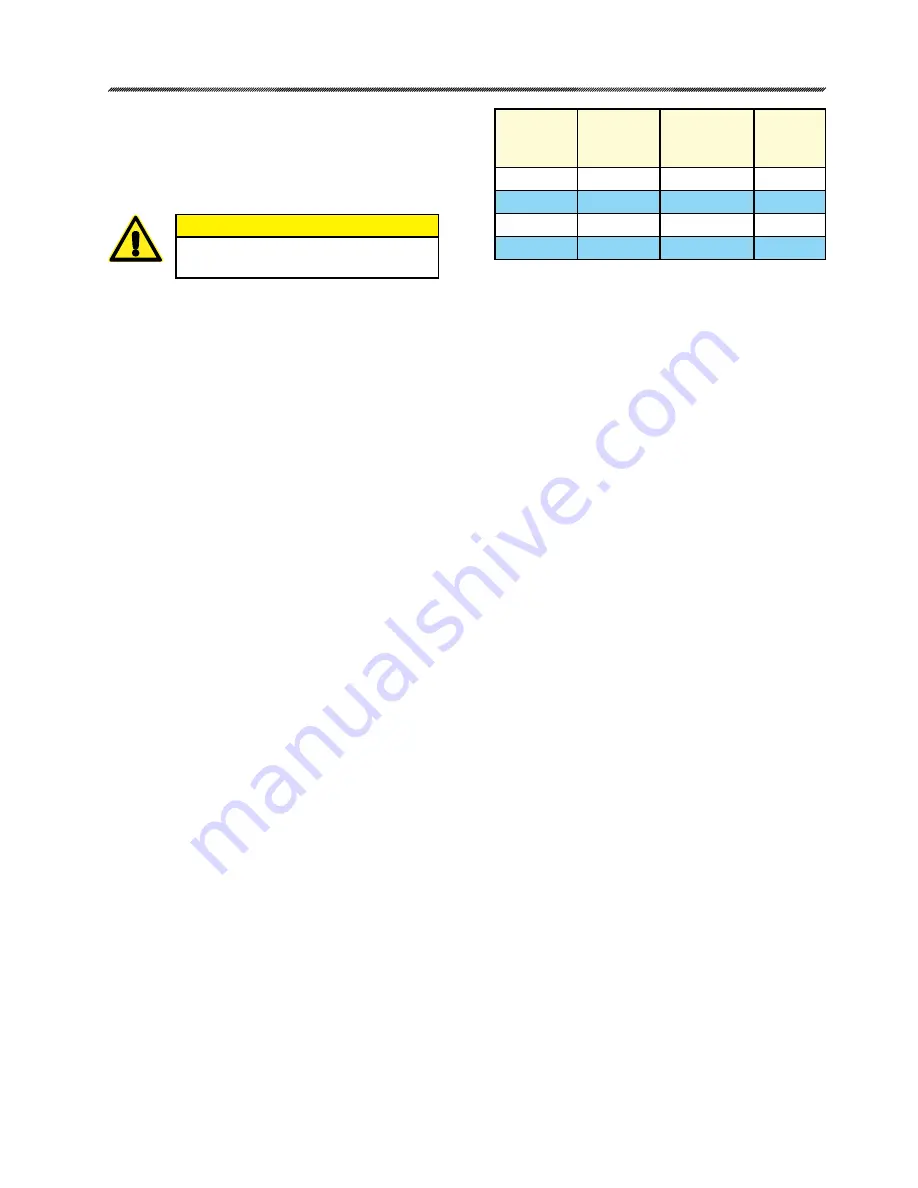
20
80-0042-00, Rev. 06.9
Setting Loss of Signal Function, cont'd
1. Remove the control module cover.
2. Verify the position of jumper plug J1/J2. Use
J1 to select the move to position function or
J2 to select the stay in place function.
CAUTION
Never use both J1 and J2—damage
will result.
3. Connect 120 V ac to terminals 1 and 2.
4. Turn on 120 V ac power supply.
5. Connect the voltmeter between test points
TP1 and TP2. TP2 is positive.
6. Turn trim potentiometer R15 until the desired
trigger level is measured on the voltmeter.
The voltage scale is:
0 V = 0 milliamps
1 V = 4 milliamps
2 V = 8 milliamps
Turn the potentiometer clockwise to increase
the trigger voltage, counterclockwise to
decrease the trigger voltage.
7. Disconnect the input signal (if connected) so
that the LOS becomes active.
8. If LOS is set to stay in place, the actuator
output shaft will not move.
9. If LOS is set to move to position:
Turn trim potentiometer R16 until the desired
output shaft position is reached. Turn the
potentiometer clockwise to increase the
output shaft position, counterclockwise to
decrease the output shaft position.
10. Replace the control module cover.
STALL FUNCTION
(Model 42‑107 Only)
The Stall function for Model 42-107 actuators
provides protection for the actuator motor and
gearing in the event of a stalled condition. The
time to stall is set at 136 seconds, after which
power to the motor is turned off. The timer resets
automatically when the signal reverses or the
Handswitch is moved from Auto to Manual.
The stall time of 136 seconds is set by the
factory and requires Jumper J3/J4 on the control
board (see Figure 7, page 19) to be set to the J4
position. If this Jumper is set to the J3 position (not
recommended), the time to stall will be decreased
to 68 seconds, which may be shorter than the full-
stroke travel time of some actuators.
R20
Ω
Parallel
Resistor
Ω
Effective
Resistance
Ω
Dead‑
band
1,000,000
1.0%
1,000,000 2,000,000
666,000
1.5%
1,000,000 1,000,000
500,000
2.0%
1,000,000
665,000
400,000
2.5%
DEADBAND ADJUSTMENT
Group 42, Option 7 actuators are shipped
with the deadband set to 1% of span to satisfy
the requirements of most control systems. If
excessive process and/or signal noise is present,
the actuator may be subject to unnecessary
cycling. It is recommended that excessive noise
be reduced at the source in order to prevent
unnecessary cycling. This will improve process
control and prolong component life.
If it is not possible to eliminate the excessive
noise, the drive's deadband can be widened;
however, this will reduce the resolution of
the drive. Widening the deadband can be
accomplished by changing the value of resistor
R20 on the Control Board (see Figure 7). The
recommended procedure is to solder a second
resistor in parallel with the existing resistor R20.
The new resistance value, recommended parallel
resistor and corresponding deadband are listed
in the following chart.
SHORT‑STROKE OPERATION
(Reducing Full Stroke Travel Distance)
Typically, it is best to use the full travel of the
actuator in response to the 0–100% Demand
input signal. However, some set-ups and
applications make it necessary to reduce this
response to less than the maximum full travel
distance. To reduce the full travel of the actuator
(short-stroke), use the following procedure:
First, adjust the Extend Travel Limit Switch
(S4) to the setting necessary to accommodate
the reduced travel range (see page 12). Note:
If necessary, both the Retract (S3) and Extend
(S4) Switches may be adjusted.
Next, perform the Feedback Signal
Calibration in relation to the new switch
setting(s) to complete setting the reduced
travel distance (see page 16).
CALIBRATION