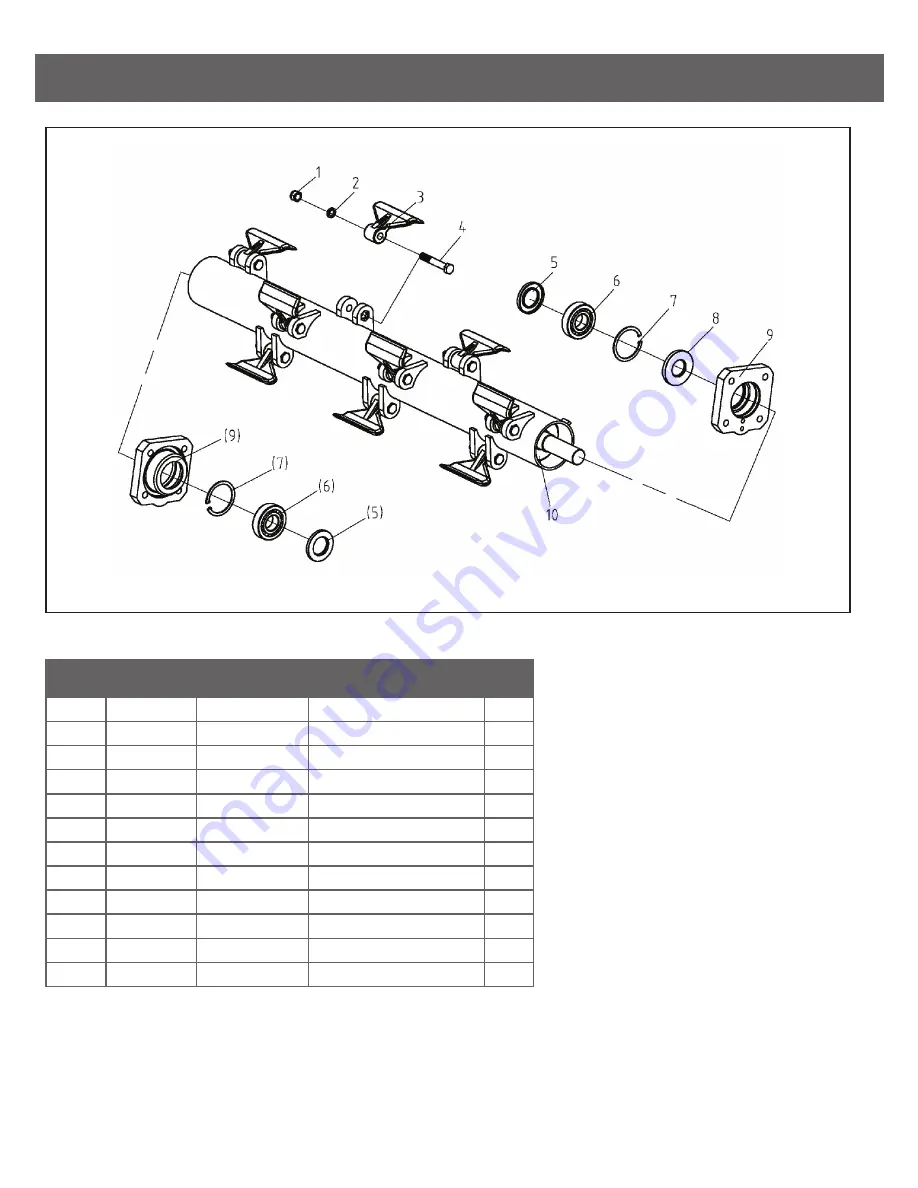
THE SWAY FRAME ASSEMBLY
BE-AGFxxx
REF NO.
PART NO.
DESCRIPTION
QTY
M16 Nut
DIN985-M16
1
12
16 Washer
GB93-16
2
12
Hammer
EFAG140.103
3
12
M16x100 Bolt
GB5782-M16X100
4
12
SYS. CODE
503010765
506030039
702480120
501010784
45x80x10 Oil Seal
GB13871-FB-
45X80X10
5
2
510020426
Bearing 1308
GB281-1308
6
2
90 Circlip
GB893.1-90
7
2
40x90x10 Oil Seal
GB1387-FB-
40X90X10
8
1
Bearing Seat
EFAG140-102A
9
2
511024244
506060195
510020445
702480119
Blade Axle AGF140
EFAG140.019B
10-1
1
802480092
Blade Axle AGF160
EFAG160.019B
10-2
1
Blade Axle AGF180
EFAG180.019B
10-3
1
802490093
802510095
Summary of Contents for BE-AGF Series
Page 17: ...PARTS DRAWING BE AGFxxx BE AGF FRAME ASSEMBLY ...
Page 20: ...THE SWAY FRAME ASSEMBLY BE AGFxxx ...
Page 24: ......