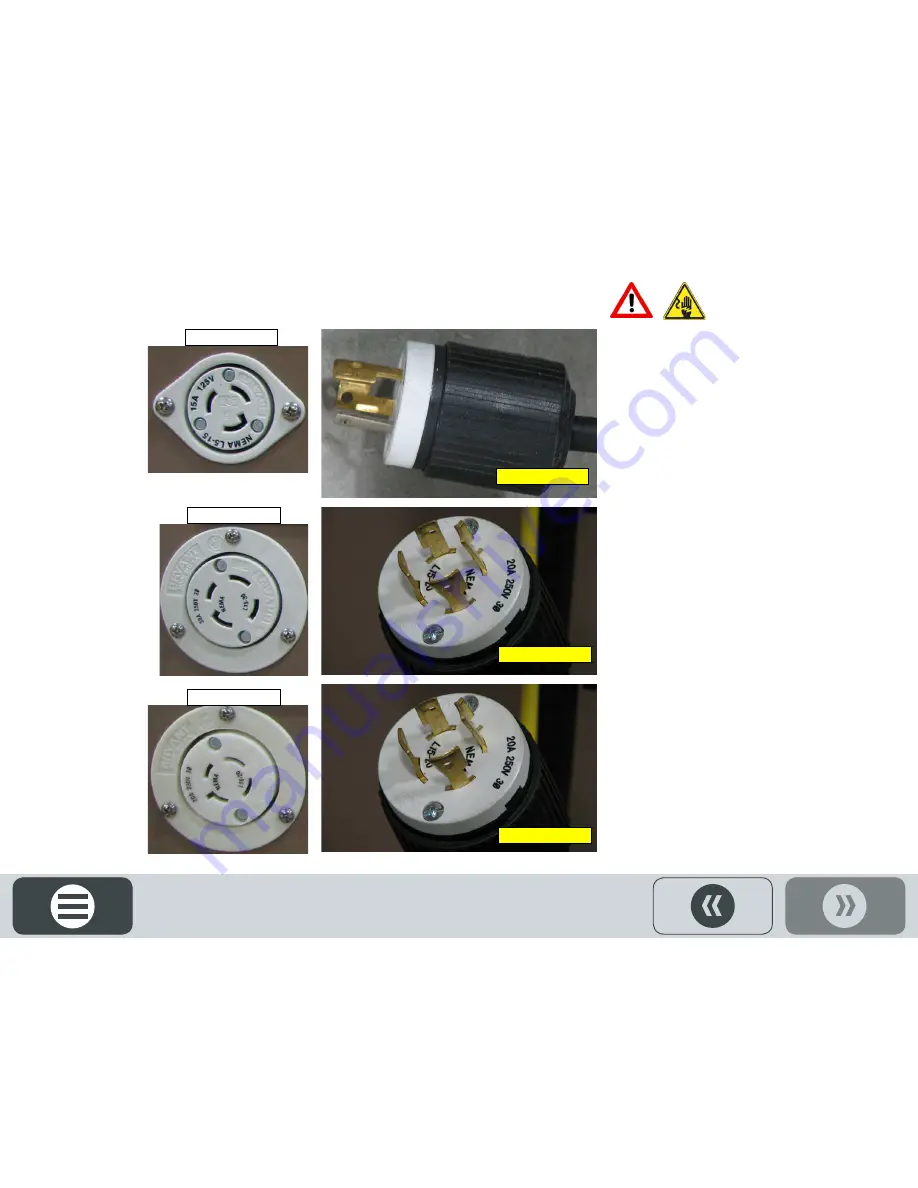
17
Electrical Connections
Step 1:
Connect the Atomizer 3-prong Power Cord to
the bottom of the Main Control Panel receptacle marked:
ATOMIZER
.
Step 2:
Connect the Seed Wheel 4-prong Power Cord to
the bottom of the Main Control Panel receptacle marked:
SEEDWHEEL
.
Step 3:
Connect the Drum VFD 4-prong Power Cord to the
bottom of the Main Control Panel receptacle
marked:
DRUM
ATOMIZER
SEEDWHEEL
DRUM
ATOMIZER
SEEDWHEEL
DRUM