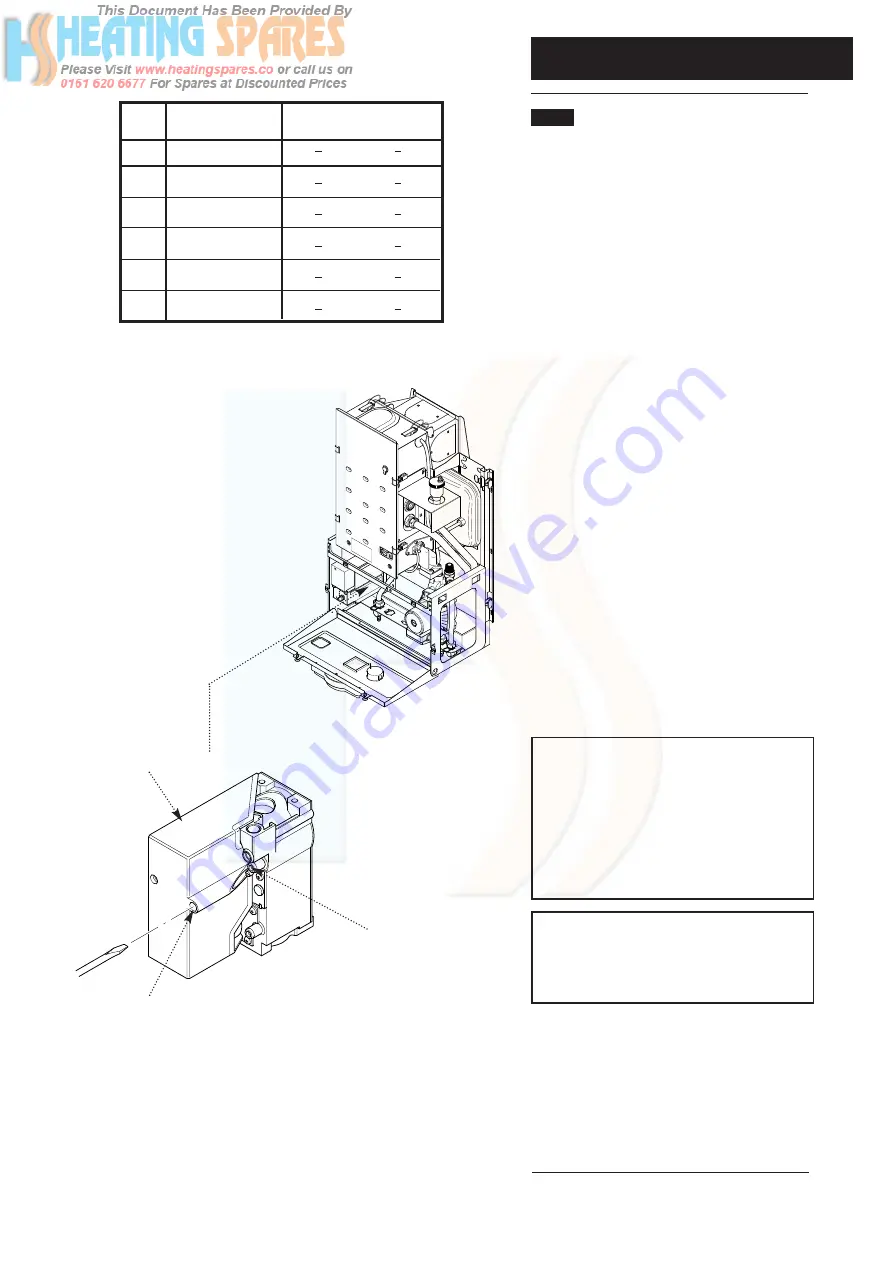
Supplied By www.heating spares.co Tel. 0161 620 6677
7.0 Commissioning the Appliance
33
7.1
Commissioning the Appliance
(Cont)
1. The burner pressure is factory set.
2. From the table opposite check that the main
burner pressure is correct after the appliance has
been running for 10 minutes. If necessary,
adjustment to main burner pressure can be made
by altering the regulator as shown (Fig. 84).
3. Check for gas soundness, with main burner
alight, using leak detection fluid.
4. Turn the boiler thermostat to the OFF position
marked 0. Remove the pressure gauge and screw
home the pressure test point screw. Turn the boiler
thermostat knob to the required setting (Fig. 84).
5. The boiler and system should be run and then
flushed and treated in accordance with
BS 7593:1992 and the flushing agent / inhibitor
manufacturers instructions. Pressurise the system
to 1.0 bar then close and disconnect the filling
loop.
6. When all the air has been removed from the
water circuit, the pump and radiators should be
balanced to achieve the design temperature drop
across the system.
7. Make a final check for gas soundness and set
any timer control, room thermostats etc. to the
customer's specific requirements.
8. The boiler is protected by an integral frost-stat,
but if the boiler is not to be used for a long period
of time, the system should be drained.
NOTE:
The frost thermostat operates even if
the boiler thermostat is in the OFF position and
it is necessary therefore, if the system is
drained, for the external electrical and gas
supplies to be isolated.
It is recommended that a label be affixed to the
appliance to draw attention to the fact that the
system has been drained.
WARNING -
If the system is filled with very cold
water and the boiler lit, the action of the frost
protection thermostat will prevent the boiler
from shutting down before the water
temperature reaches 10
°
C.
9. Carefully read and complete all sections of the
“
Benchmark
”
Installation, Commissioning and
Service Record Log Book that are relevant to the
appliance and installation. The details of the Log
Book will be required in the event of any warranty
work. The Log Book must be handed to the user
for safe keeping and each subsequent regular
service visit recorded.
Pressure Test Point
Gas Valve
Fig. 84
Fig. 83
Model
Input P
Setting Pressure
kW
Btu/h
mbar
in wg
30
10.99
37, 500
16.0 + 0.5
6.4 + 0.2
40
14.65
50, 000
16.0 + 0.5
6.4 + 0.2
50
18.32
62, 500
16.0 + 0.5
6.4 + 0.2
60
21.98
75, 000
16.0 + 0.5
6.4 + 0.2
70
25.64
87, 500
16.0 + 0.5
6.4 + 0.2
80
29.31
100,000
16.0 + 0.5
6.4 + 0.2
Regulator