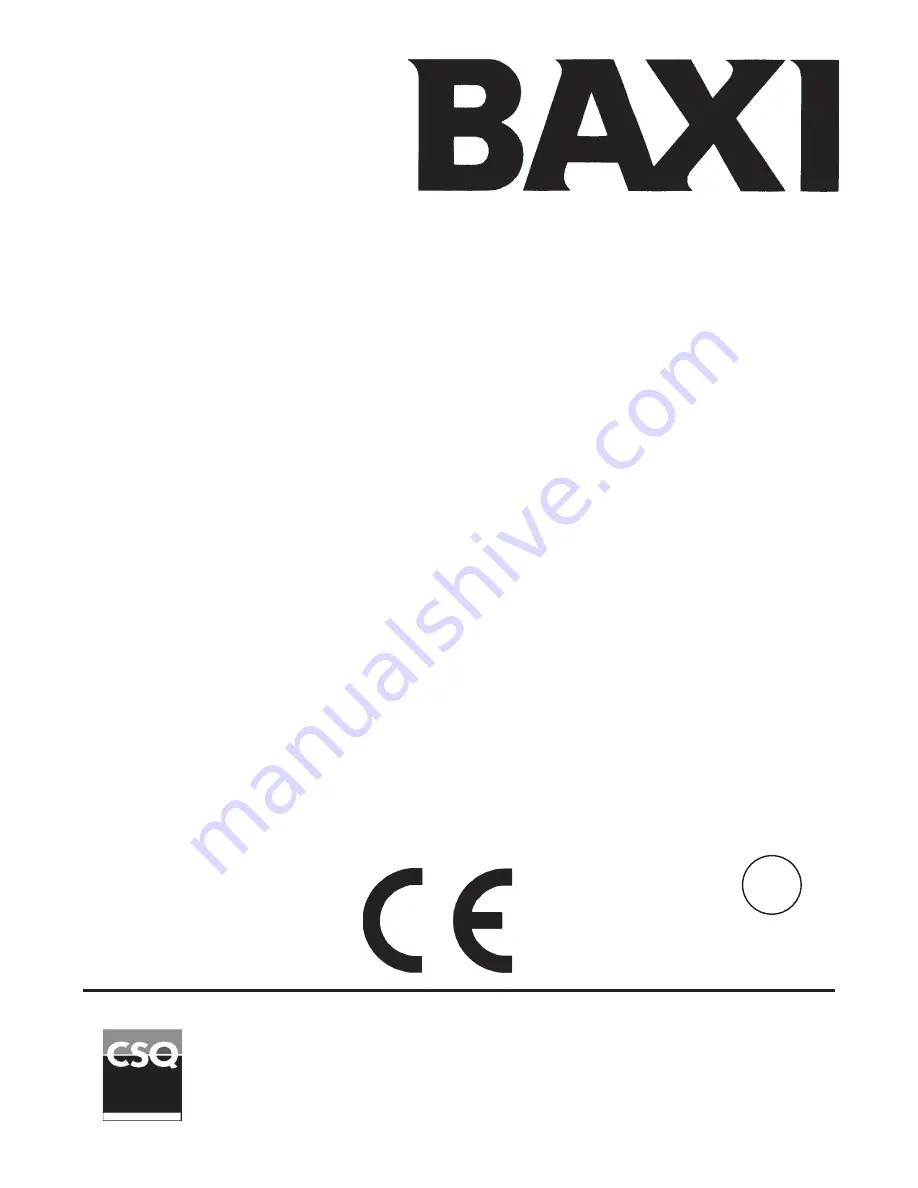
Wall-mounted condensing boilers
Installerʼs and Userʼs Instructions
BAXI S.p.A.
is a leading European manufacturer of central heating and domestic hot water appliances (wall mounted gas
boilers, floor standing boilers, electric water heaters) and has been certified by CSQ as conforming to UNI EN ISO 9001.
This certification confirms that the Quality System of
BAXI S.p.A.
in Bassano del Grappa, where this boiler was manufactured,
satisfies the strict UNI EN ISO 9001 standard covering all aspects of company organisation, manufacturing and distribution.
UNI EN ISO 9001
CERTIFICAZIONE DEI SISTEMI
QUALITA' DELLE AZIENDE
PRIME HT
0085
GB