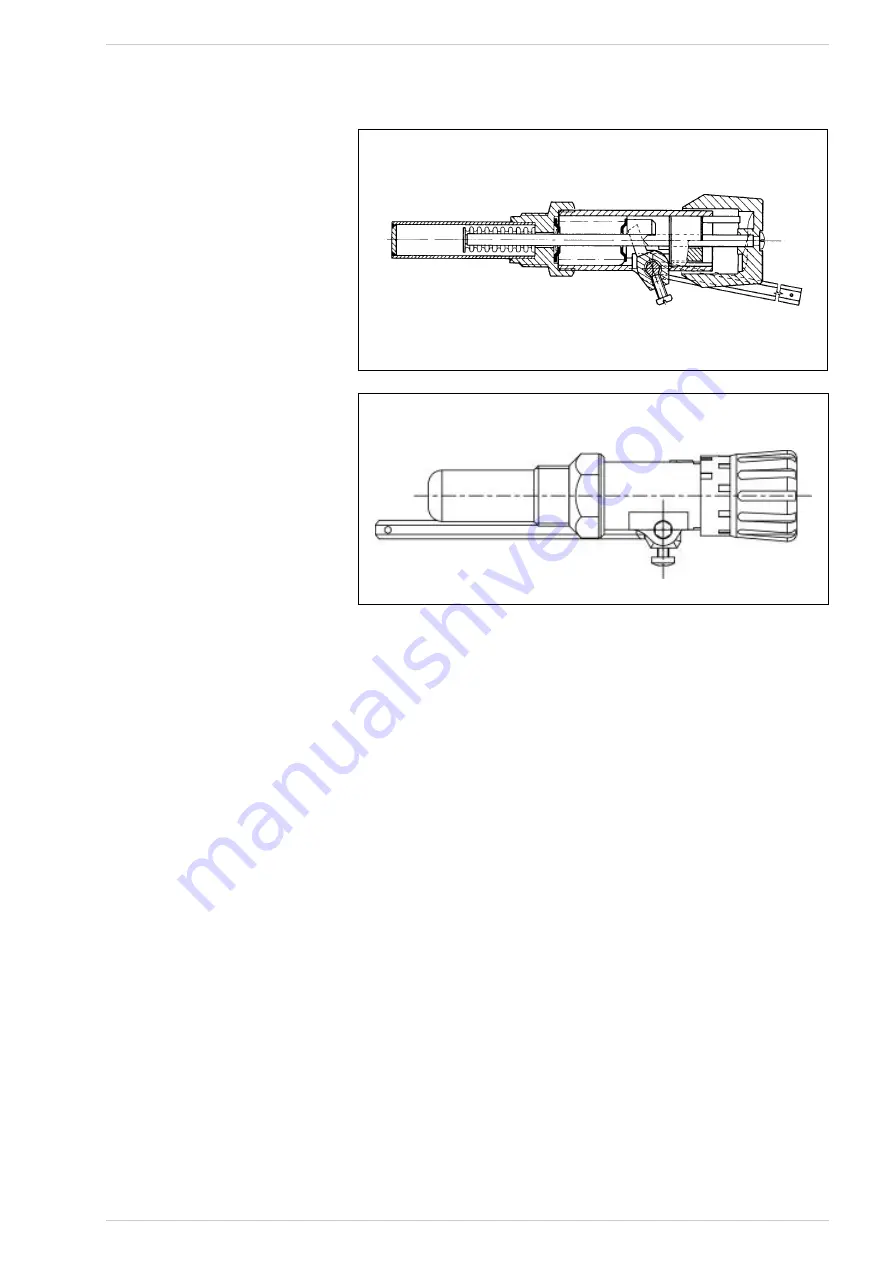
34
support brackets.
The assembly of the casing components
must be carried out in the following way:
– Unscr ew wit h some r o t ations t he
second or third nut of each tie rod.
– Connect the left side (1) on the lower
and upper tie rod of the boiler and adjust
the position of the nut and lock-nut of the
upper tie-rod.
– Block the side by tightening the locknuts.
– In order to assembly the right side (2)
proceed in the same way.
– Connect the rear panel (4) introducing
the two splines in the vents obtained on
each side and lock it with self-threading
screws.
– The protection deflector (5) is fixed to
the control panel (6) with three self-
threading screws. Insert the mineral
wool between the two components.
– Fasten the front panel (6) using the pres-
sure pins.
– Unwind the capillary of the thermometer
(7) and and introduce it in the left sheath
of the rear head introducing the contact
spring which must be cut at about 45
mm. The thermometer cable must be
placed above the insulation and must not
contact directly the iron cast body.
– Fasten the cover (8) to the sides of the
boiler using the pressure pins.
- Apply the BOILER TECHNICAL DATA
adhesive plate on the right or left side of
the covering, so as to be legible when
the appliance is installed.
NOTICE: Store the "Test report" and
"Declaration of conformity" placed in the
combustion chamber together with the
documents of the boiler.
4.6
DRAUGHT REGULATOR WITH
THERMOSTATIC OPERATION
By means of the draught regulator with
thermostatic operation, a continuous varia-
bility of the air introduced in the boiler fur-
nace can be obtained.
By means of a connecting chainlet, this
regulator acts on the lower primary air
intake port.
Once the set temperature has been rea-
ched, the regulator decreases the opening
of the air intake port automatically, so to
slow down the combustion and prevent
over-heating. In order to optimise the com-
bustion on the upper load port, place a
round adjusting port that distributes the
secondary air countercurrent compared to
the path of the combustion products.
This process further increases the yield
and allows exploiting the combustion more
effectively. Two types of thermostatic regu-
lators can be assembled on the boilers.
4.6.1
“THERMOMAT RT-C” Regulator
(fig. 7)
The “Thermomat” regulator is equipped
with a thermosetting resin knob of an adju-
stment field from 30 to 100 °C.
Screw the regulator on the 3/4” opening of
the anterior head and orientate the red
index on the upper part.
The lever with the chainlet should be intro-
duced in the regulator holder after having
assembled the instrument holder board
and after having removed the plastic lock.
If the joint is taken out, which fixes the lever
with the chainlet, take care in assembling it
again in the same position.
After having placed the knob at 60°C, block
the lever with the chainlet in a slightly incli-
ned position downwards, so that the chain-
let will be in axis with the air gate damper.
For the adjustment of the “Thermomat”,
which essentially consists in the determina-
tion of the chainlet length, proceed in the fol-
lowing way:
– Place the knob at 60°C.
– Switch on the boiler with opened air gate
damper.
– When the water temperature of 60° C
is reached in the boiler, fix the chainlet in
such a way on the lever of the air gate
damper, in order to obtain an opening of
about 1 mm.
– Now the regulator is calibrated and it is
possible to choose the desired operating
temperature by rotating the knob.
4.6.2
“REGULUS RT2” Regulator
(fig. 8)
The adjustment field is included between 30
and 90°C (fig. 8). Follow the same instruc-
tions of the “Thermomat” regulator for the
assembly and the activation.
4.7
SAFETY EXCHANGER
The safety exchanger is supplied upon
request with a kit:
- code 8105200 f or
BPI-Eco
1.250/1.350/1.450
-
code 8105201 f or
BPI-Eco
1.550/1.650
.
The kit must be used on closed expansion
tank systems with power lower than 35
kW. Its function is to cool the boiler in case
of over-temperature, by using a thermal
discharge valve connected to the exchan-
ger inlet hydraulically.
In correspondence to the exchanger outlet,
place one drainpipe with funnel and a
siphon that drive to a suitable discharge.
The discharge must be visible for inspec-
tion.
ATTENTION: Failure to comply with this
precaution, a possible activation of the
thermal discharge valve can damage per-
sons, animals and objects, which the
manufacturer is not responsible for.
Before commissioning the boiler, ensure
t hat t he wat er f low of t he t her mal
discharge valve is guaranteed.
Fig. 8
“REGULUS RT2” Regulator
Fig. 7
“THERMOMAT RT-C” Regulator
Summary of Contents for BPI-Eco 1.250
Page 1: ...IT RUS FR ENG BPI Eco ...
Page 2: ......
Page 12: ...12 NOTES ...
Page 37: ...37 NOTES ...
Page 38: ...38 NOTES ...
Page 39: ......
Page 40: ...Ediz 1 01 2014 codice 6113772 ...