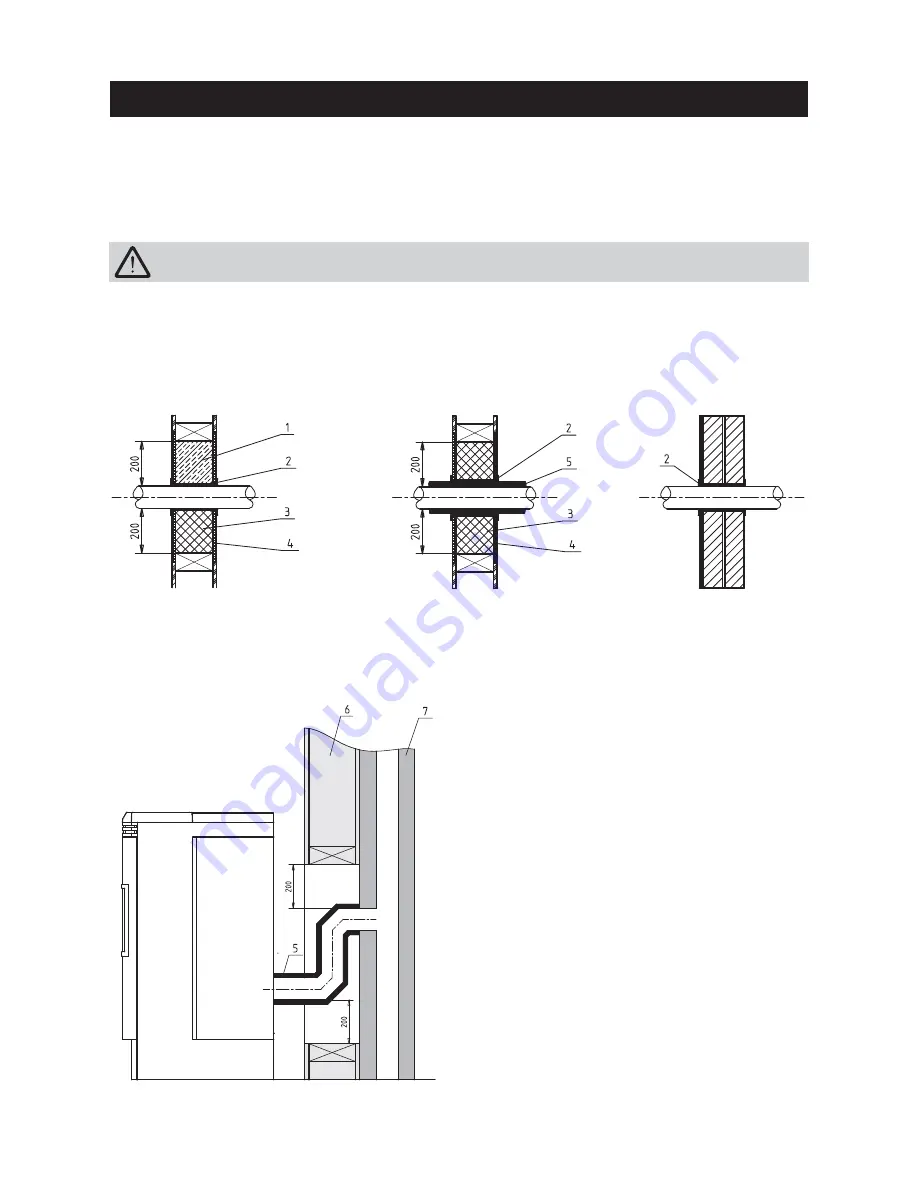
16
2.5
Minimum service clearances for fire protection, cleaning
and maintenance
The following minimum service clearances from flammable materials and for connections, cleaning and maintenance
must be complied with.
The configuration of the entire system must comply with technical fire protection requirements in accor-
dance with the applicable regulations, standards and guidelines.
2.5.1 Masonry feed-throughs for the exhaust pipe
Examples of masonry feed-throughs tested by the IBS – Institut für Brandschutztechnik und Sicherheitsforschung
(Institute for Fire Protection Technology and Safety Research)
1 . . . . . .Concrete fill
2 . . . . . .Lining pipe
3 . . . . . .Cavity fill with non-flammable material
(e.g. rock wool)
4 . . . . . .Non-flammable cover
5 . . . . . .Exhaust pipe insulation 20 mm
techn. data of insulation:
– Mineral wool insulation
– Melting point: > 1000 °C
– Thermal conductivity: < 0.04 W/mK
– Minimum thickness: 20 mm
6 . . . . . .Multi-layer flammable wall
7 . . . . . .Flue
Multi-layer flammable wall
Multi-layer flammable wall
Non-flammable wall
All dimensions in mm:
Fig. 13
Tested masonry feed-throughs for exhaust pipe
Multi-layer flammable wall
There must be a gap of 200 mm from flammable com-
ponents all round the exhaust pipe.
Fig. 14
Tested masonry feed-throughs for exhaust pipe
For the Installer
Summary of Contents for Bioflo
Page 45: ...44 4 6 FireWIN basic circuitry For the Service Technician 092464 01 ...
Page 50: ...Notes ...
Page 51: ...Notes ...