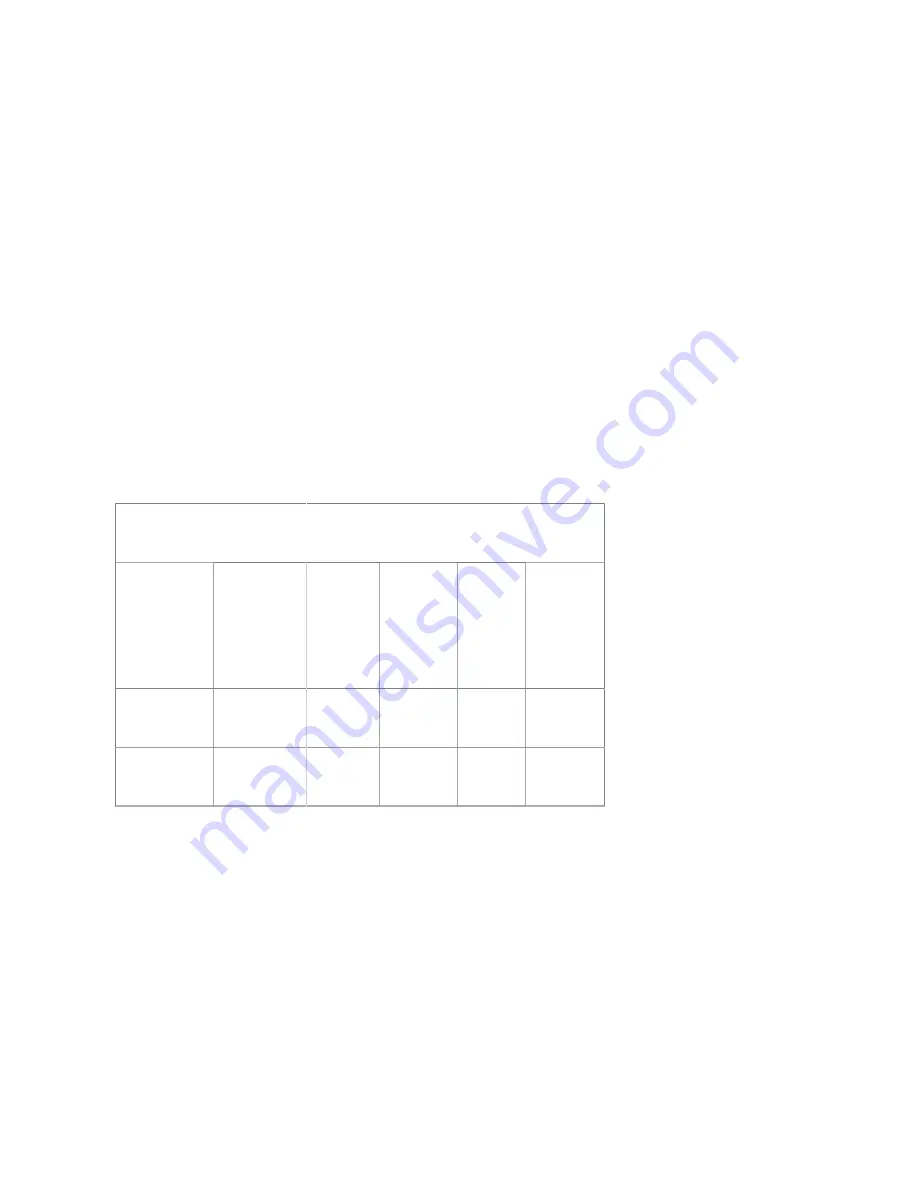
energy required to defrost the unit is drawn from the buffer and helps to prevent the room temperature
dropping unnecessarily. This also avoids unnecessary use of the 5kW electric heater which would
give an increase in electrical consumption. For these reasons, operation without a buffer vessel is not
recommended.
6. When the Baxi Ambiflo
™
Heat Pump is used in conjunction with Underfloor heating emitters, they are
of considerably greater thermal mass than the other heat emitters such as radiators. Because it takes much
longer to raise the floor temperature at initial start up, (although once operating it will stay at the correct
temperature for longer due to thermal mass), there is a problem if the whole floor area is opened up to
the heat pump on initial start up. The high heat losses into a cold floor will prevent the heating medium
reaching the correct operating temperature and ultimately could cause the heat pump to frost up severely.
To overcome this problem the best solution is to fit a thermal buffer between the heat pump and the
heating system so that the heat pump is raising the temperature within the buffer and not directly within
the floor. In addition the heating systems should be split into a number of zones to allow for variations in
heat load and to improve start up at the commissioning stage.
7. In low load conditions, the installation of a buffer can eliminate short cycling, which is where the heat
generated during the minimum run time for the heating appliance cannot be absorbed by the heating
system, maybe due to closure of the thermostatic radiator valves. This effectively increases the run time
of the heat pump and aids longevity and reliability of the system.
Baxi recommendations:
Underfloor
Radiators
Valves
System
Volume
less than
(litres)
buffer
Volume
(litres)
N
Y
closed
70
Y
100
Y
N
open
200
Y
100
Fig. 10
Page 15
4.0 Electrical
4.1 Baxi Ambiflo
™
Programmable room sensor.
1. This is a Baxi System solution using the controls supplied, where no other time or temperature controls
are used.