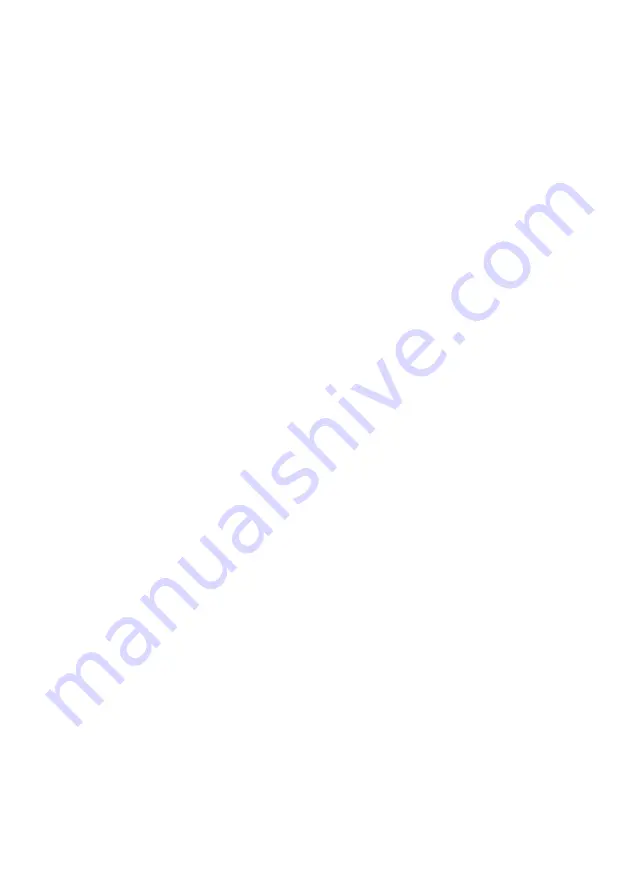
ELECTRICAL CONNECTION / FUNCTIONAL PRINCIPLE HMCP16
12/40
MB168T1EN - 11184527, 19A2, Baumer_HMC16-T1_II_EN
6.
ELECTRICAL CONNECTION
6.1
Functional principle HMCP16
The differential SinCos encoder signals, connected to the input, are converted into TTL,
HTL, SinCos output signals with interpolated pulses/cycles and/or SSI output (speed and
position), frequency output� The zero pulse is adjusted as well if available�
Zero pulse signals R+ and R- (output 1 and 2) are determined on the basis of the input
signals R+ and R- of the inputs 1 and 2 up to a speed of ~1000 rpm� At higher speeds R+
and R- are synthesised internally�
To achieve a reliable high resolution, automatic offset and amplitude adjustment for the
incoming SinCos signals and oversampling algorithms are applied�
The SinCos signals are sampled and digitized with 1 MHz and digitally pre-filtered. To
-
gether with the downstream oversampling filter for the calculated position, a high signal
quality of the multiplied output signals is achieved, even if the input signals are noisy or
distorted by hazardous peaks�
The SSI output, if available, has two SSI channels SSI1 and SSI2� The exact division of
bits and the scaling you can find in
�
SSI1 transmits a speed word included error bit and parity bit� SSI2 transmits angle infor-
mations� These consists an incremental 14 bit position word, a 14 bit position word for the
reference index Ri and a Ri seen bit, an error bit and a parity bit�
After turning on the device the incremental position is 0� Each revolution is passing
through a value range between 0 up to 2
14
-1�
After turning on the device the Ri seen bit is 0� The Ri seen bit gets to 1 when a valid
reference index Ri is detected� Then the active incremental position was safed and is
provided as Ri position�
If there‘s a detected problem with the input signals the error bit gets to 1�
For the dual version (two inputs) the input SinCos encoder signals were taken and inter-
nally together cleared to achieve a runout error compensation�
If the system is equipped with an error adjustment table (HMC16T1 ���) the accuracy of
the complete system is increased over again� This error adjustment table is aligned to the
HMCK16T1 ��� and the HMCP16T1 ��� which have the same serial number� Please note
that the error adjustment table only can cause an output signal amelioration when the
adapted HMCK16T1 ��� is connected to the HMCP16T1 ��� with the same serial number�
Furthermore the optimized output signal amelioration is only possible when output 1 of
the HMCK16T1 ��� is connected with the input 1 of the HMCP16T1 ��� and, if available, the
output 2 of the HMCK16T1 ��� is connected with the input 2 of the HMCP16T1 ����