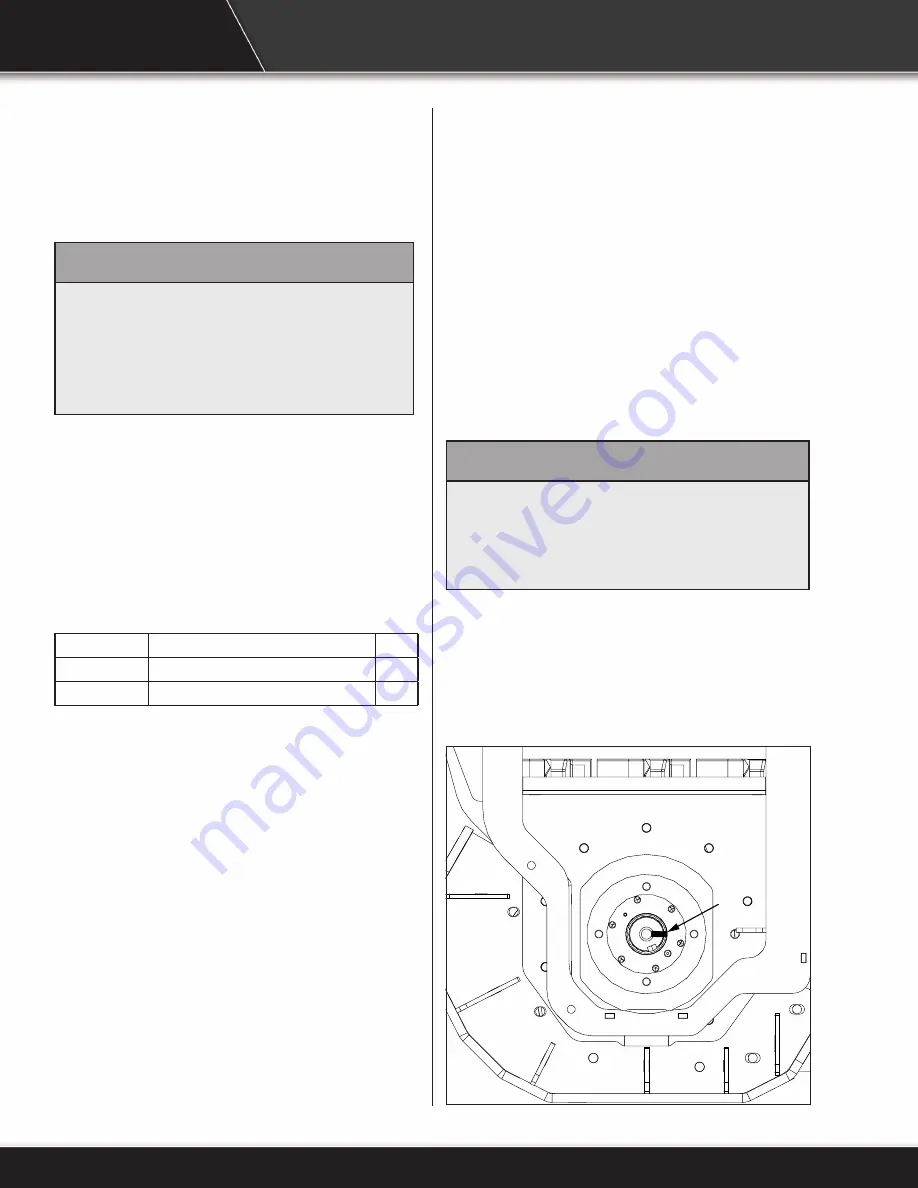
^
WARNING
Pressurized fluids can penetrate the
skin�
Disconnect and lock out power source
before disconnecting and/or connecting
hydraulic hoses�
The mulcher is equipped with short hoses that
are connected to the hydraulic motor. You must
connect your skidsteer hoses to these hoses.
Hydraulic couplers are not provided with the
mulcher. You must install couplers and connect
your skidsteer pressure, return and case drain
hoses to the mulcher hoses. Install your couplers
to the hoses listed in the table below.
Fitting Size Hose Description
Qty.
3/4 JIC FM Pressure & Return
2
3/8 JIC FM Case Drain
1
Identify the pressure port hose and connect your
hoses to the brush mulcher hoses.
4�2 Motor Pressure Port
C930 - A port on block (B port on motor)
C940 - A port on block (B port on motor)
C950 - A port on block (B port on motor)
C970 - A port on block (B port on motor)
4�3 Maximum Allowable Case
Pressure
C930 - 100 psi, case drain required.
C940 - 100 psi, case drain required.
C950 - 100 psi, case drain required.
C970 - 100 psi, case drain required.
4 INITIAL SETUP
4�1 Hydraulics
4�4 Optional Two Speed Motor Setup
The optional two speed motor requires fine tuning
to the flow provided by the carrier machine.
The fine tuning will need to be performed in the
field while operating in conditions where normal
work will be performed.
Baumalight recommends this be done by the
Dealer or Territory Sales Rep.
^
WARNING
Moving parts can crush and cut�
Entanglement hazard�
Keep clear of moving components�
1.
An RPM meter is required. Open cover and
place reflective tape (A) on bearing end of
shaft. Measuring shaft speed on the bearing
end will provide the most accurate results.
RPM setting from factory is 1525 RPM with 36
GPM.
A
10