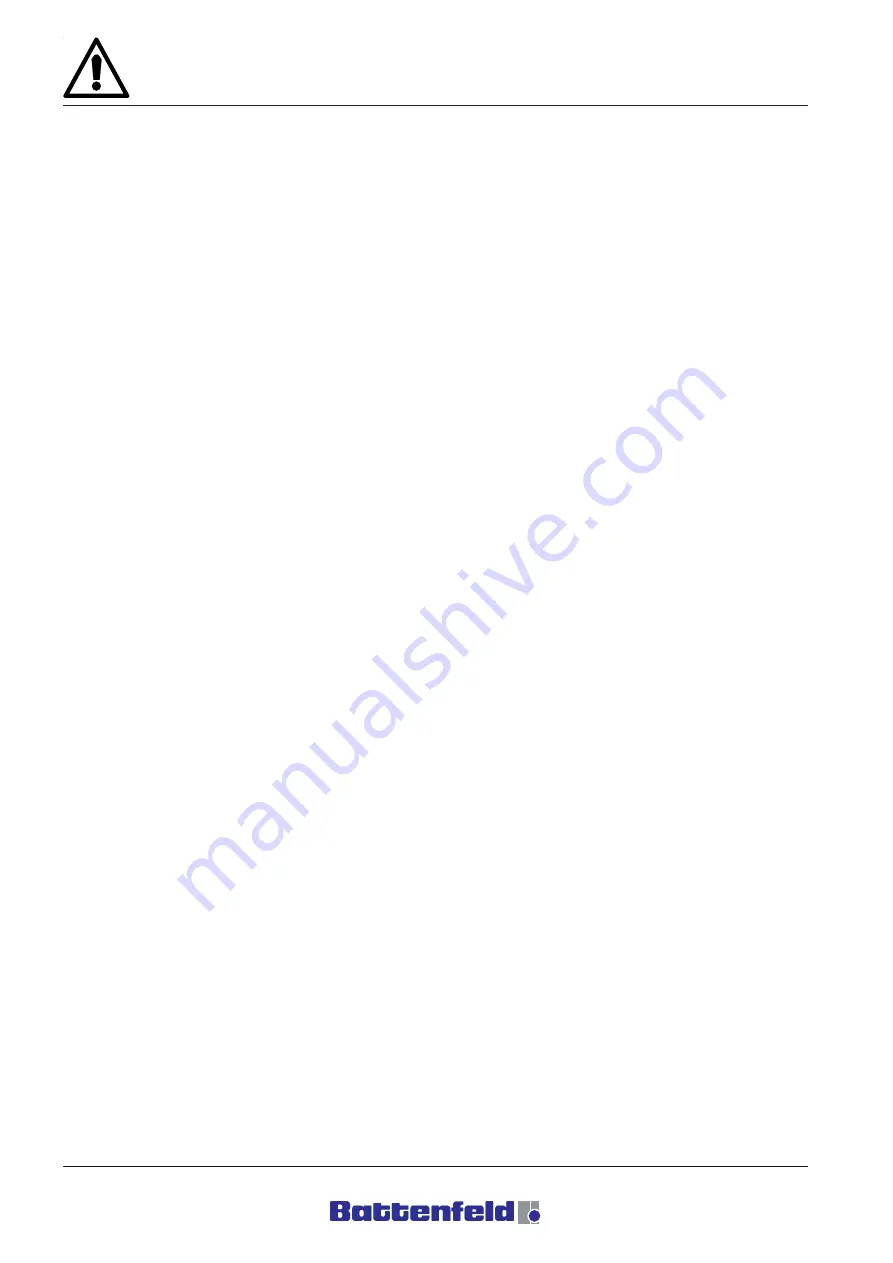
A: R82GB0BA.PMD
B: R82DE0BA.PMD
E: 080403 / T. Wenger
G: 020403 / TCS
Section 2
Page 6
Safety
2.1.5
Safety regulations – Pneumatic
system
Compressed air pipes for the pneumatic system
must be properly routed and fitted. The fittings,
length and cross section must meet with the
requirements.
Carry out regular checks on all pipes, hoses,
and screw connections to determine any leaks
and recognisable exterior damage. Any damage
must be repaired immediately.
2.1.6
Safety regulations – Electrical system
The IMM and robot electrical system, which
have been designed and built according to
currently valid DIN EN 60204-1 and IEC 801-2
norms, are operationally reliable. Hazards may
however be created in the IMM robot’s electrical
system if it is improperly operated by untrained
persons or used for purposes other than its
intended use. All assembly/disassembly,
conversion and maintenance work may
therefore only be carried out by electricians
(according to DIN VDE 0105 or DIN EN 60204-
1).
The electrical system may only be connected to
a power supply of a current type, voltage and
frequency which corresponds to the
specifications on the robot system rating plate.
Electrical feeder cables must meet with the
specified requirements.
Shut down the robot system at the main switch
before carrying out any assembly/disassembly,
conversion or maintenance work. Make sure
that the electrical system is de-energised,
earthed and short-circuited.
The electrical system must be checked
regularly. Any defects such as loose
connections or burned cables must be
remedied immediately.
For safety reasons, the operator must log off the
control system after completing the set-up
operation in order to prevent unauthorised
persons from specifying any other values.
Legal rules and regulations must be observed
when carrying out any assembly/disassembly,
conversion or maintenance work.
Summary of Contents for UNILOG B2
Page 4: ...A PB2GBI1A P65 B PB2DEI1A P65 E 180202 Ruder G 190202 G Krajnik Section IN1 Page 2 Index...
Page 10: ......
Page 14: ...A R82GB0AA PDM B R82DE0AA PDM E 080403 T Wenger G 020403 TCS Section 1 Page 4 General...
Page 16: ...A R82GB0AA PDM B R82DE0AA PDM E 080403 T Wenger G 020403 TCS Section 1 Page 6 General...
Page 32: ...A R82GB0CA PDM B R82DE0CA PDM E 080403 T Wenger G 020403 TCS Section 3 Page 10 Specifications...
Page 118: ...A R82GB0HA PMD B R82DE0HA PMD E 080403 T Wenger G 020403 TCS Section 7 Page 16 Maintenance...