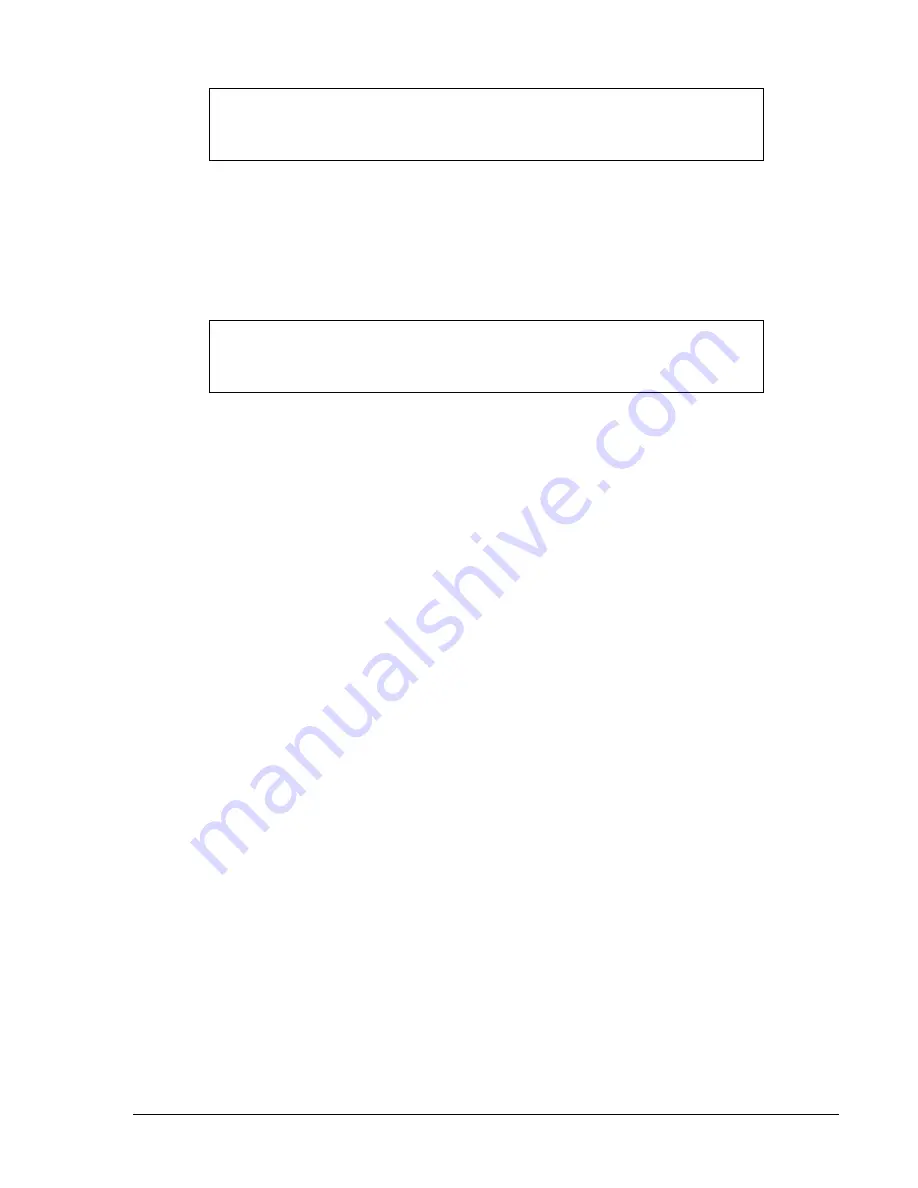
9171400990 Rev G
BE1-59N Testing
5-3
Step 16. Adjust the 150 or 180 Hz voltage (at terminals 6 and 7) to above pickup (i.e., UNDERVOLTAGE
LED OFF).
Step 17. Set the UNDERVOLTAGE TIME DIAL for any convenient delay. Reset targets (if present).
Step 18. Reduce the sensing input below pickup (or disconnect it) while noting the time lapse before the
undervoltage relay(s) trip. Check that response time is the TIME DIAL setting
±
525
milliseconds.
Step 19. Connect a 150/180 Hz source to relay terminals 6 and 7 as shown in Figure 5-1. Note that this
setup allows rapid switching from a voltage that is approximately twice pickup to a voltage that
is
Δ
V lower than pickup. The switching also provides a means of precisely verifying the time
between the voltage step change and the resulting output response.
Step 20. Set the UNDERVOLTAGE TIME DIAL to the desired characteristic curve. (Reference Figure 1-
4.)
Step 21. Adjust the voltage output of T2 to twice that of T1.
Step 22. Decrease the voltage of T1 by an amount that represents any
Δ
V of interest.
Step 23. Press and release S2 (of Figure 5-1) to assure that K1 is de-energized. Reset the timer. Press
S1. The time recorded by the counter should be within 5% or 25 milliseconds (whichever is
greater) of the time given in Figure 1-4.
Step 24. By changing
Δ
V, steps 22 and 23 may be repeated to verify any segment of the characteristic
curve that is of interest.
NOTE
Steps 16 through 18 apply only to relays with undervoltage definite time delay. If
not so equipped, proceed to the note following step 18.
NOTE
The remaining steps of this procedure apply only to relays with undervoltage
inverse time delay. For all other relays, the operational test is concluded.
Summary of Contents for BE1-59N
Page 2: ......
Page 6: ...iv BE1 59N Introduction 9171400990 Rev G This page intentionally left blank ...
Page 8: ...vi BE1 59N Introduction 9171400990 Rev G This page intentionally left blank ...
Page 16: ...1 8 BE1 59N General Information 9171400990 Rev G This page intentionally left blank ...
Page 22: ...3 4 BE1 59N Functional Description 9171400990 Rev G This page intentionally left blank ...
Page 24: ...4 2 BE1 59N Installation 9171400990 Rev G Figure 4 1 Panel Cutting Drilling Semi Flush Case ...
Page 32: ...4 10 BE1 59N Installation 9171400990 Rev G Figure 4 9 Sensing Input Connections ...
Page 38: ...5 4 BE1 59N Testing 9171400990 Rev G This page intentionally left blank ...