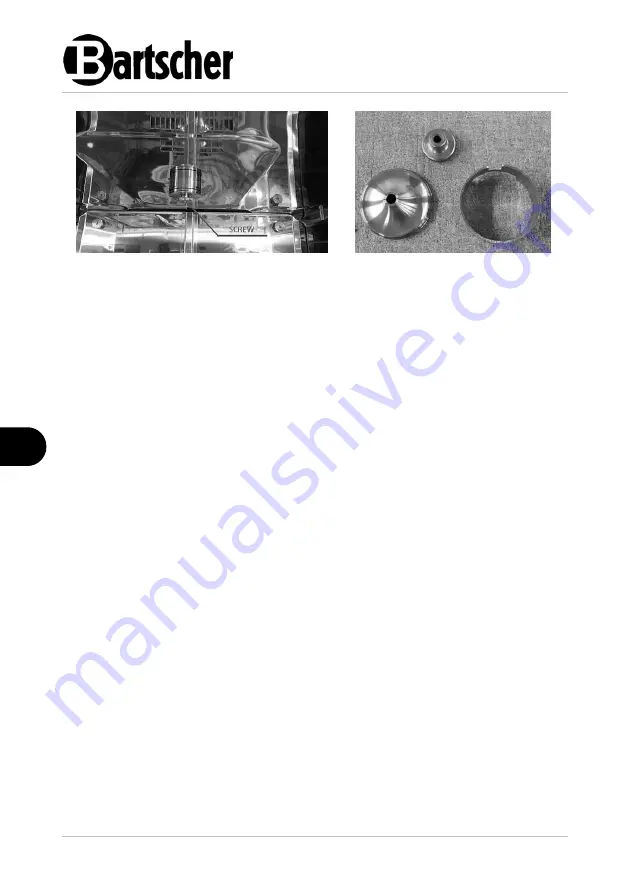
Cleaning and Maintenance
84 / 86
117900
EN
Fig. 50
Fig. 51
7.3
Maintenance
ATTENTION!
The following maintenance and cleaning work must only be carried out by
qualified and specialised personnel and never by the user of the
appliance!
Cleaning the Condensate Collecting Tank with Trap at the Oven Rear Wall
Every 3
–6 months, a preventive service inspection and cleaning of the outlet
channel and the condensate collecting tank with trap, located at the rear of the
oven, should be carried out.
The service technician should carry out the following steps:
– cool the oven down to room temperature before maintenance work;
– disconnect the oven from the main electricity supply;
– find the condensate collecting tank with the trap at the rear wall of the
oven for cleaning;
– unscrew the trap lid;
– clean the condensate collecting tank;
– clean the ends of all the supply lines to the trap lid;
– screw the cover back on;
– finally, check that all wires have been returned to their original positions
and that all connections have been tightened securely.