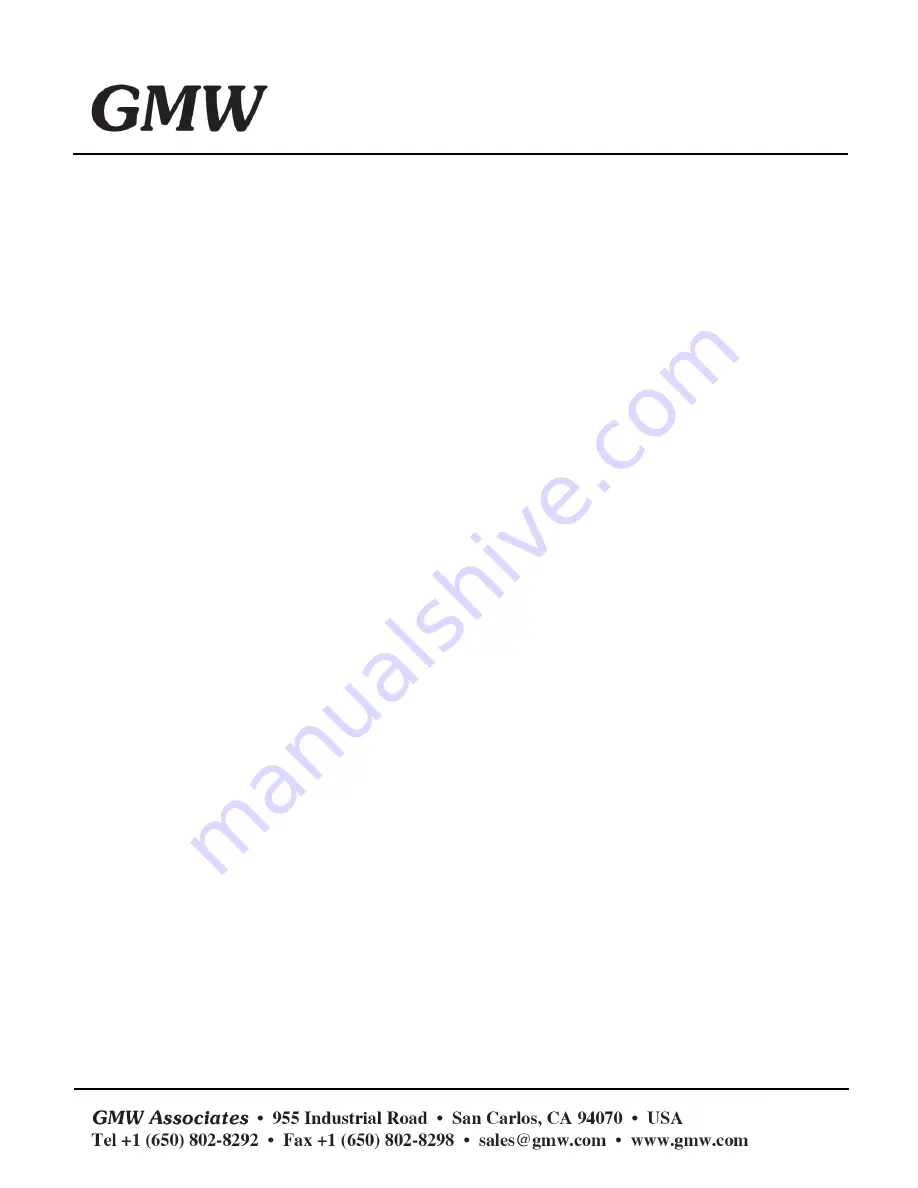
HELMHOLTZ COIL INSTALLATION AND CALIBRATION
should also be connected now. Report to the connection diagrams below for cases with the CU2. Next
connect the CU1 to the National Instruments acquisition card and finally connect the NI card to the PC.
If using the CU2, the CU2 reference magnetometer should be placed within the coils and aligned to the
coil’s axes.
When mounted in a Bartington coils, the CU2 Reference Magnetometer mounting face (the
one engraved) will be down, with the potting facing upwards.
Mains connections for the PA1, CU1 and PC can now take place. The power up order should be as
follow:
•
PC, including starting the Bartington Helmholtz Coil Control Software
•
National Instruments card
•
PA1
•
CU1
Note that if there is a connection issue between the CU1 and the NI card and PC, or that the software
is not opened, an alarm will sound in the CU1. The alarm will turn off once all elements including the
software are opened/switched-on.
The system now needs to be left to warm-up for at least 6 hours prior to calibration. This ensures that
calibration takes place with the system being stable. In the meantime, the Mag-13MS mounting jig can be
placed within the coils using the necessary support pillars/table provided (coil dependent). The jig should
be mounted so that the sensor’s Z axis (along the length of the sensor) is aligned with the coil’s Z axis
(refer to the axis orientation label on the coil). The Mag-13MS can also be connected to the CU1. If
choosing the Auxiliary input, the sensor will be automatically powered. If choosing to connect it to the
device under test (this will be compulsory if using the CU2), you will need to switch the power supply to
DUT to 12V in the control software. The input type should be set to differential where the Mag-13 is
connected, and if using the CU2, the auxiliary input should be set to single-ended.
Once at least 6 hours have passed, the system is now ready for calibration checks.
6.
Calibration
Systems are calibrated at Bartington after manufacture. However disassembly (for some coils),
transport, handling may affect some of the mechanical positioning of the coils, and therefore slightly
affect the system accuracy. Furthermore, DC offsets are specific to a given site and orientation of the coils.
These therefore need to be accounted for and adjusted. Three parameters are typically checked and
adjusted, DC offsets, scaling and orthogonality. The process to check each is described below.