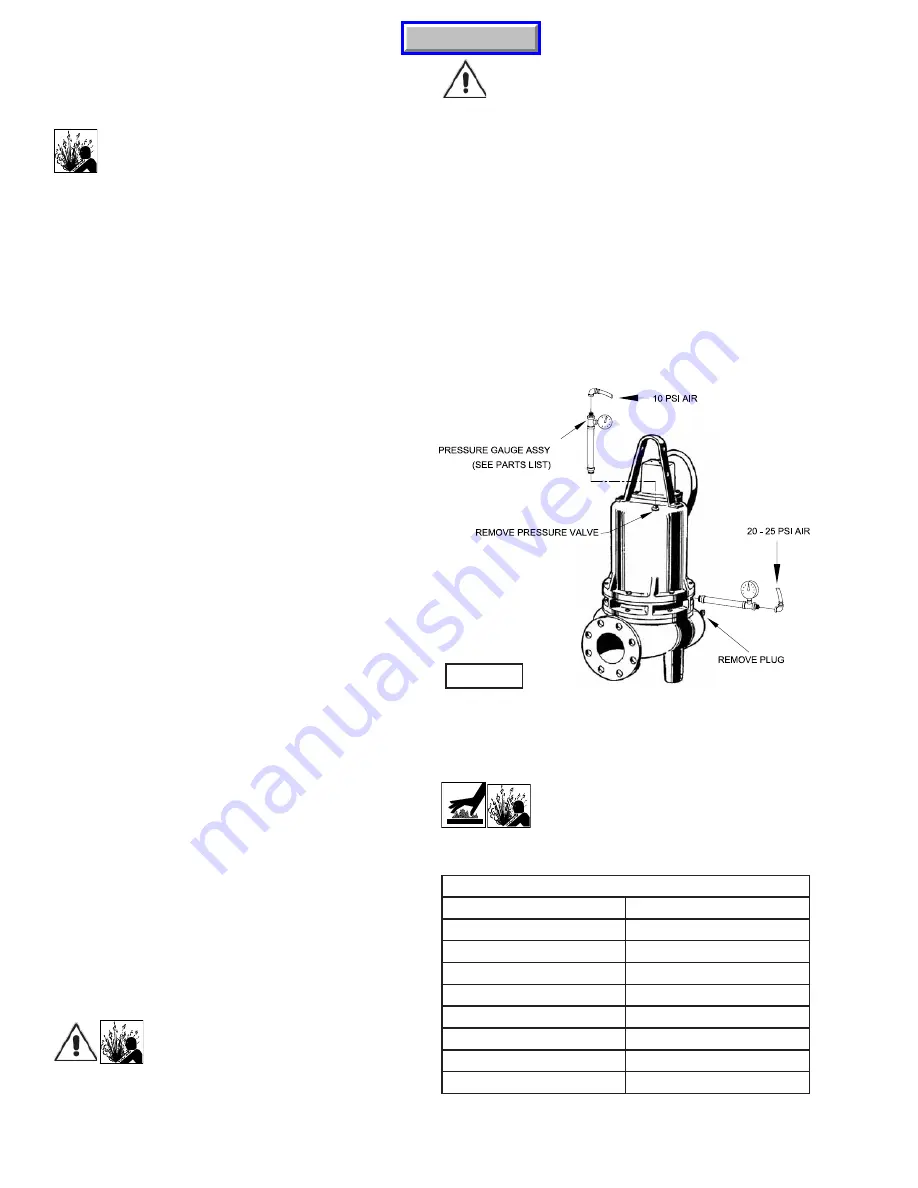
8
SECTION F: SERVICE AND REPAIR
NOTE:
All item numbers in ( ) refer to Figures 9 & 10.
WARNING ! - Before servicing and/or removing
pump from system, verify that the piping system
has no pressure.
F-1) Lubrication:
Anytime the pump is removed from operation the cooling oil
in the motor housing (2) and seal chamber, must be checked
visually for oil level and contamination.
F-1.1) Checking Oil:
Motor Housing -
To check oil, set unit upright. Remove cap
screws (6), lift conduit box assembly (10) from motor hous-
ing (2) but
DO NOT
disconnect conduit box wiring from motor
leads. With a fl ashlight, visually inspect the oil in the motor
housing (2) to make sure it is clean, clear and that oil level is
above all internal componentry.
Seal Chamber -
Place pump on its side with the square head
pipe plug (22) downward (180° from discharge on bearing
bracket 21), remove pipe plug (22) and drain oil from the seal
chamber. If the oil is found to contain considerable water or
other contamination or little oil drains out, the shaft seal (46)
and diaphragm (32) should be inspected and replaced if
required.
F-1.2) Testing Oil:
1. Place pump on it’s side, remove cap screws (6), lift
conduit box assembly (10) from motor housing (2) and
drain oil into a clean, dry container. In separate
container drain seal chamber by removing pipe plug (22).
2. Check oil for contamination using an oil tester with a
range to 30 Kilovolts breakdown.
3. If oil is found to be clean and uncontaminated (measure
above 15 KV. breakdown), refi ll the motor housing
and seal chamber as per section F-1.3.
4. If oil is found to be dirty or contaminated (or measures
below 15 KV. breakdown), the the pump must be
carefully inspected for leaks at the shaft seal (46),
conduit box assembly (10), diaphragm (32), O-rings (42),
pipe plugs (22) and (45) and pressure valve (5) before
refi lling with oil. To locate the leak, perform a pressure
test as per section F-1.4. After leak is repaired, refi ll with
new oil as per section F-1.3.
F-1.3) Replacing Oil:
Motor Housing -
Drain all oil from motor housing and
dispose of properly. Refi ll with (see parts list for amount) new
cooling oil as per Table 1. An air space must remain in the top
of the motor housing to compensate for oil expansion (see
Fig. 9). Set unit upright and fi ll only until the motor, as viewed
through the conduit box opening, is just covered and no
more. Reassemble the O-ring (11), conduit box assembly (10)
and cap screws (6), apply thread locking compound to each
cap screw (6) thread before installing. Torque cap screws (6)
to 15 ft., lb.
Seal Chamber -
Refi ll chamber completely full with new
cooling oil per Table 1 or reuse the uncontaminated oil.
WARNING ! - DO NOT overfi ll oil.
Overfi lling of motor housing with oil can
create excessive and dangerous hydraulic
pressure which can destroy the pump and
create a hazard. Overfi lling oil voids warranty.
WARNING ! - Motor housing is supplied with
pressure relief valve (5), look for signs that the
valve may have been activated. The motor may
have overheated causing a very high temperature
condition, thus causing the valve to release pressure.
The pump and/or motor may need servicing.
F-1.4) Pressure Test:
Motor Housing- Before checking the pump for leaks around
the shaft seal, square rings, and cord inlet, the oil level should
be full as described in section F-1.3. Remove pressure valve
(5) from motor housing (2). Apply pipe sealant to pressure
gauge assembly and tighten into pressure valve hole (see
Fig. 2). Pressurize motor housing to 10 P.S.I. Use a soap
solution around the sealed areas and inspect joints for “air
bubbles”. If, after fi ve minutes, the pressure is still holding
constant, and no “bubbles” are observed, slowly bleed the
pressure and remove the gauge assembly. Replace the
Pressure valve using a sealant. If the pressure does not hold,
then the leak must be located.
Seal Chamber-
Remove pipe plug (22) from Bearing Bracket
(21) and check that seal chamber is full of oil. Apply pipe
sealant to pressure gauge assembly and tighten into hole in
bearing bracket (21). Pressurize seal chamber to 20-25 PSI
and check for leaks as outlined above.
CAUTION ! - Pressure builds up extremely
fast, increase pressure by “TAPPING” air
nozzle. Too much pressure will damage
seal. DO NOT exceed 10 P.S.I. in motor
housing & 20-25 P.S.I. in seal chamber
TABLE 1 - COOLING OIL - Dielectric
SUPPLIER
GRADE
BP
Enerpar SE100
Conoco
Pale Paraffi n 22
Mobile
D.T.E. Oil Light
G & G Oil
Circulating 22
Imperial Oil
Voltesso-35
Shell Canada
Transformer-10
Texaco
Diala-Oil-AX
Woco
Premium 100
FIGURE 2
Manual Index