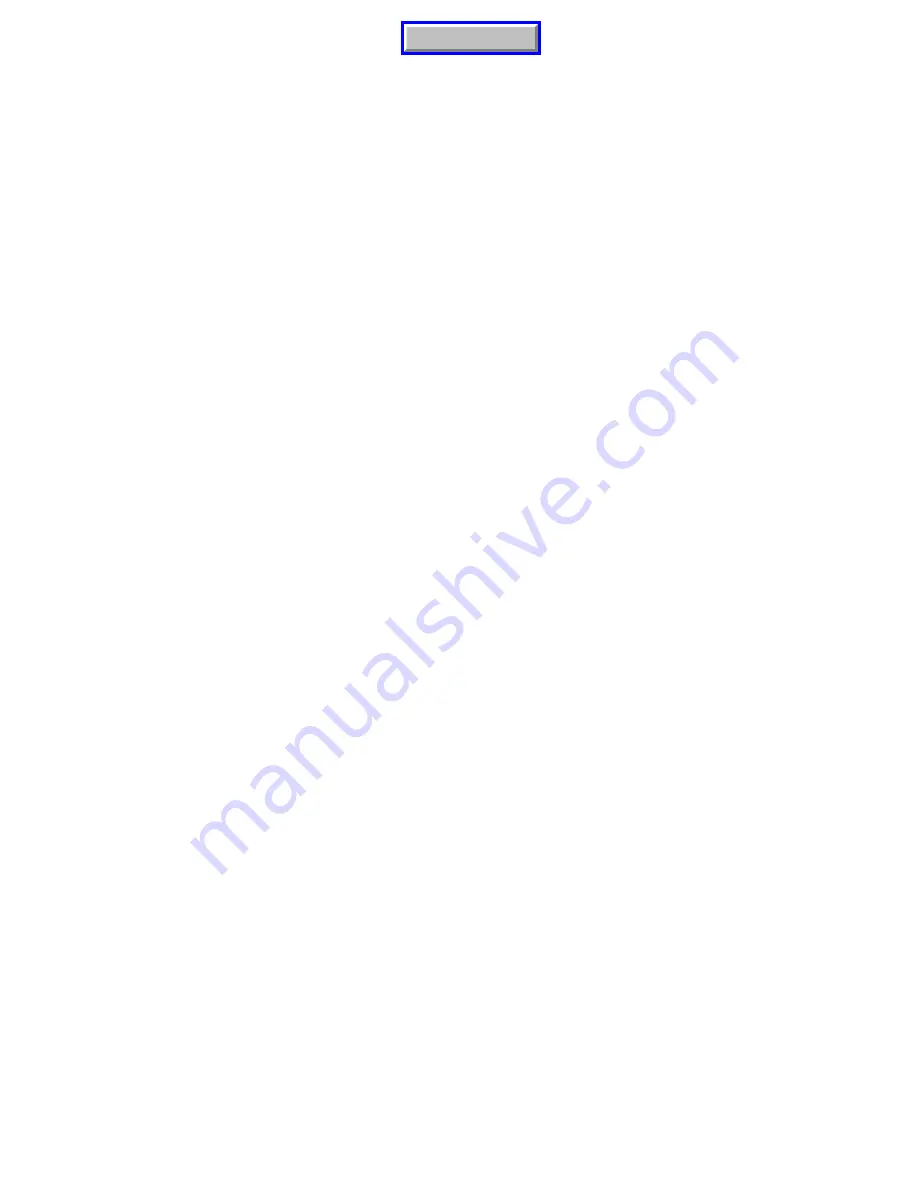
6
SECTION B: GENERAL INFORMATION
B-1) To the Purchaser:
Congratulations! You are the owner of one of the fi nest pumps
on the market today. CP&S pumps are products engineered
and manufactured of high quality components. Over one
hundred years of pump building experience along with a
continuing quality assurance program combine to produce a
pump which will stand up to the toughest applications. This
manual will provide helpful information concerning installation,
maintenance, and proper service guidelines.
B-2) Receiving:
Upon receiving the pump, it should be inspected for damage
or shortages. If damage has occurred, fi le a claim immediately
with the company that delivered the pump. If the manual
is removed from the packaging, do not lose or misplace.
B-3) Storage:
Short Term-
CP&S Pumps are manufactured for effi cient
performance following short inoperative periods in storage.
For best results, pumps can be retained in storage, as factory
assembled, in a dry atmosphere with constant temperatures
for up to six (6) months. Long Term- Any length of time
exceeding six (6) months, but not more than twenty-four (24)
months. The unit should be stored in a temperature controlled
area, a roofed over walled enclosure that provides protection
from the elements (rain, snow, wind-blown dust, etc.), and
whose temperature can be maintained b40 deg. F
and +120 deg. F. (4.4 - 49°C). Pump should be stored in its
original shipping container. On initial start up, rotate impeller
by hand to assure seal and impeller rotate freely. If it is
required that the pump be installed and tested before the long
term storage begins, such installation will be allowed provided:
1.) The pump is not installed under water for more than
one (1) month.
2.) Immediately upon satisfactory completion of the test,
the pump is removed, thoroughly dried, repacked in the
original shipping container, and placed in a temperature
controlled storage area.
B-4) Service Centers:
For the location of the nearest Barnes Service Center, check
your Barnes representative or Crane Pumps & Systems, Inc.,
Service Department in Piqua, Ohio, telephone (937) 778-8947
or Crane Pumps & Systems Canada, in Brampton, Ontario,
(905) 457-6223.
SECTION C: INSTALLATION
C-1) Location:
These pumping units are self-contained and are recommended
for use in a sump, lift station or basin. This pump is
designed to pump sewage, effl uent, or other nonexplosive
or noncorrosive wastewater and shall
NOT
be installed in
locations classifi ed as hazardous in accordance with the
National Electrical Code (NEC), ANSI/NFPA 70 or Canadian
Electrical Code. Never install the pump in a trench, ditch or
hole with a dirt bottom; the legs will sink into the dirt and the
suction will become plugged.
C-2) Discharge:
Discharge piping should be as short as possible. Both a
check valve and a shut-off valve are recommended for
each pump being used. The check valve is used to prevent
backfl ow into the sump. Excessive backfl ow can cause
fl ooding and/or damage to the pump. The shut-off valve
is used to stop system fl ow during pump or check valve
servicing.
C-3) Liquid Level Controls:
The level controls are to be supported by a mounting bracket
that is attached to the sump wall, cover or junction box. Cord
grips are used to hold the cords in place on the mounting
bracket. The control level can be changed by loosening
the grip and adjusting the cord length as per the plans and
specifi cations. Be certain that the level controls cannot
hang up or foul in it’s swing and that the pump is completely
submerged when the level control is in the “Off” mode.
C-4) Electrical Connections:
C-4.1) Power & Control Cords:
The cord assembly mounted to the pump must not be
modifi ed in any way except for shortening to a specifi c
application. Any splice between the pump and the control
panel must be made in accordance with all applicable electric
codes. It is recommended that a junction box, if used, be
mounted outside the sump or be of at least Nema 4 (EEMAC-
4) construction if located within the wet well.
DO NOT USE
THE POWER OR CONTROL CORDS TO LIFT PUMP.
NOTE: The White Wire Is Not A Neutral Or Ground Lead,
But a Power Carrying Conductor.
C-4.2) Overload Protection :
C-4.2-1) Three Phase -
The normally closed (N/C) thermal
sensor is embedded in the motor windings and will detect
excessive heat in the event an overload condition occurs.
The thermal sensor will trip when the windings become too
hot and will automatically reset itself when the pump motor
cools to a safe temperature. It is recommended that the
thermal sensor be connected in series to an alarm device to
alert the operator of an overload condition, and/or the motor
starter coil to stop the pump. In the event of an overload, the
source of this condition should be determined and rectifi ed
immediately.
DO NOT LET THE PUMP CYCLE OR RUN IF
AN OVERLOAD CONDITION OCCURS !
C-4.3) Moisture Sensors:
A normally open (N/O) detector is installed in the pump seal
chamber which will detect any moisture present. It is recom-
mended that this detector be connected in series to an alarm
device or the motor starter coil to alert the operator that a
moisture detect has occurred. In the event of a moisture
detect, check the individual moisture sensor probe leads for
continuity, ( ∞ resistance = no moisture ) and the junction
box/control box for moisture content. The above situations
may induce a false signal in the moisture detecting circuit. If
none of the above test prove conclusive, the pump(s) should
be pulled and the source of the failure identifi ed and repaired.
IF A MOISTURE DETECT HAS OCCURRED SCHEDULE
MAINTENANCE AS SOON AS POSSIBLE.
Manual Index