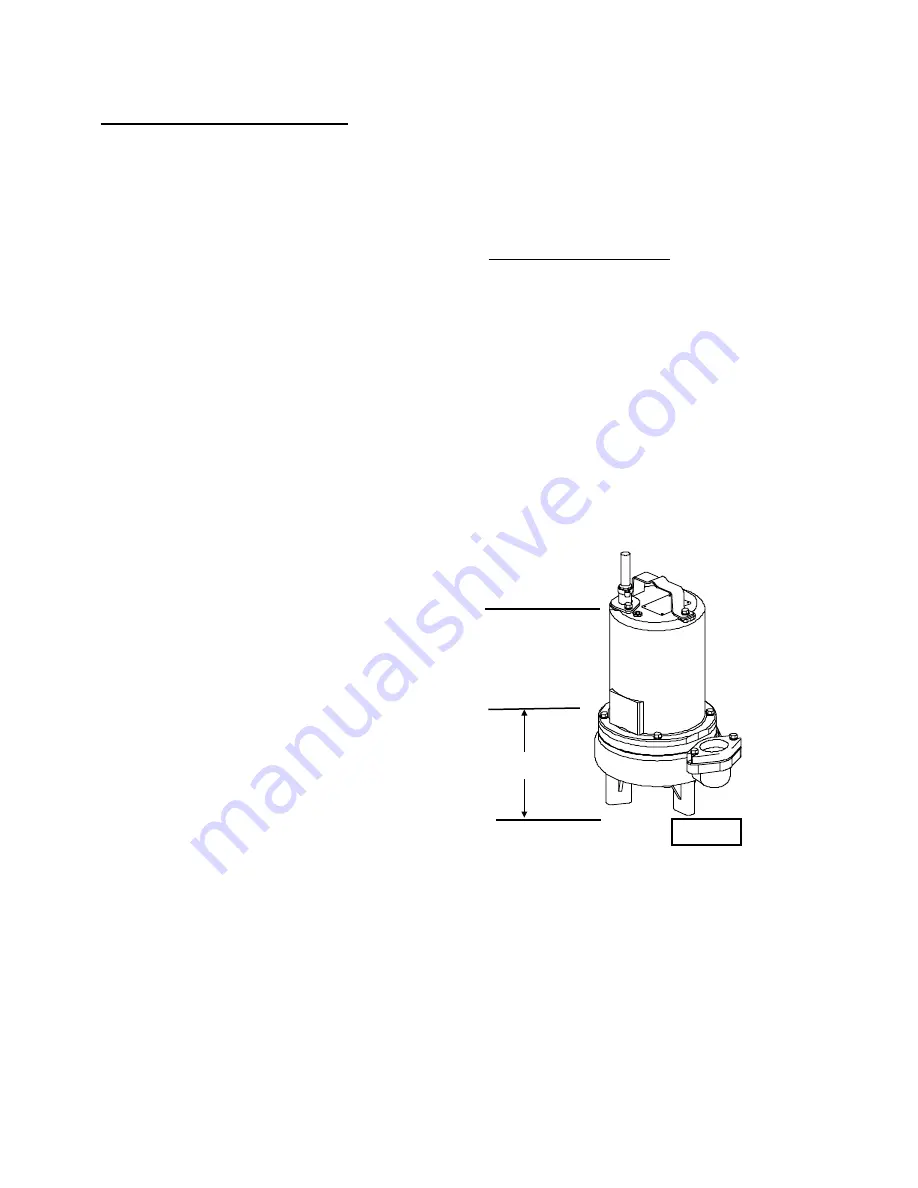
SECTION B: GENERAL INFORMATION
B-1) To the Purchaser:
Congratulations! You are the owner of one of the finest pumps
on the market today. Barnes
®
Pumps are products engineered
and manufactured of high quality components. Over one
hundred years of pump building experience along with a
continuing quality assurance program combine to produce a
pump which will stand up to the toughest applications.
This Barnes Pumps, Inc. manual will provide helpful
information concerning installation, maintenance, and proper
service guidelines.
B-2) Receiving:
Upon receiving the pump, it should be inspected for damage
or shortages. If damage has occurred, file a claim immediately
with the company that delivered the pump. If the manual is
removed from the packaging, do not lose or misplace.
B-3) Storage:
Short Term-
Barnes Pumps are manufactured for efficient
performance following short inoperative periods in storage. For
best results, pumps can be retained in storage, as factory
assembled, in a dry atmosphere with constant temperatures
for up to six (6) months.
Long Term-
Any length of time exceeding six (6) months, but
not more than twenty-four (24) months. The units should be
stored in a temperature controlled area, a roofed over walled
enclosure that provides protection from the elements (rain,
snow, wind-blown dust, etc.), and whose temperature can be
maintained b40 deg. F and +120 deg. F. If extended
high humidity is expected to be a problem, all exposed parts
should be inspected before storage and all surfaces that have
the paint scratched, damaged, or worn should be recoated with
a water base, air dry enamel paint. All surfaces should then be
sprayed with a rust-inhibiting oil.
Pump should be stored in its original shipping container. On
initial start up, rotate impeller by hand to assure seal and
impeller rotate freely. If it is required that the pump be installed
and tested before the long term storage begins, such
installation will be allowed provided:
1.) The pump is not installed under water for more than
one (1) month.
2.) Immediately upon satisfactory completion of the test,
the pump is removed, thoroughly dried, repacked in the
original shipping container, and placed in a temperature
controlled storage area.
B-4) Service Centers:
For the location of the nearest Barnes Pumps Service Center,
check your Barnes Engineered catalog, your Barnes Pumps,
Inc. representative or Barnes Pumps, Inc. Service Department
in Piqua, Ohio, telephone (937) 778-8947 or Crane Pumps &
Systems Canada, Brampton, Ontario,
(905) 457-6223.
SECTION C: INSTALLATION
C-1) Location:
These pumping units are self-contained and are recommended
for use in a sump, lift station or basin. The sump, lift station or
basin shall be vented in accordance with local plumbing codes.
This pump is designed to pump sewage, effluent, or other
nonexplosive or noncorrosive wastewater. and shall NOT be
installed in locations classified as hazardous in accordance with
the National Electrical Code (NEC), ANSI/NFPA 70 or the
Canadian Electrical Code (CEC). Never install the pump in a
trench, ditch or hole with a dirt bottom; the legs will sink into the
dirt and the suction will become plugged.
C-1.1) Submergence:
It is recommended that the pump be operated in the submerged
condition and the sump liquid level should never be less than
10 inches above the pump bottom (see Fig. 1).
C-2) Discharge:
Discharge piping should be as short as possible. Both a check
valve and a shut-off valve are recommended for each pump
being used. The check valve is used to prevent backflow into
the sump. Excessive backflow can cause flooding and/or
damage to the pump. The shut-off valve is used to stop system
flow during pump or check valve servicing.
Barnes Pumps supplies a Stainless Rail Package for the 2"
models and also a variety of 2" and 3" break-away fitting
discharge systems designed to allow the submersible
wastewater pump to be installed or removed without requiring
personnel to enter the wet well. Contact your local Barnes
Pumps distributor for complete details.
Recommended
Submergence
Level
Fig. 1
10"
Minimum
Submergence
Level
Bottom of Feet
6
Summary of Contents for 2SEV
Page 15: ...Fig 13 15...
Page 18: ...Fig 15 2SEV L 3SEV L Series Single Seal 18...
Page 19: ...Fig 16 2SEV L 3SEV L Series Single Seal 19...
Page 20: ...Fig 17 2SEV DS 3SEV DS Series Double Seal 20...
Page 21: ...Fig 18 2SEV DS 3SEV DS Series Double Seal 21...
Page 24: ...NOTES 24...