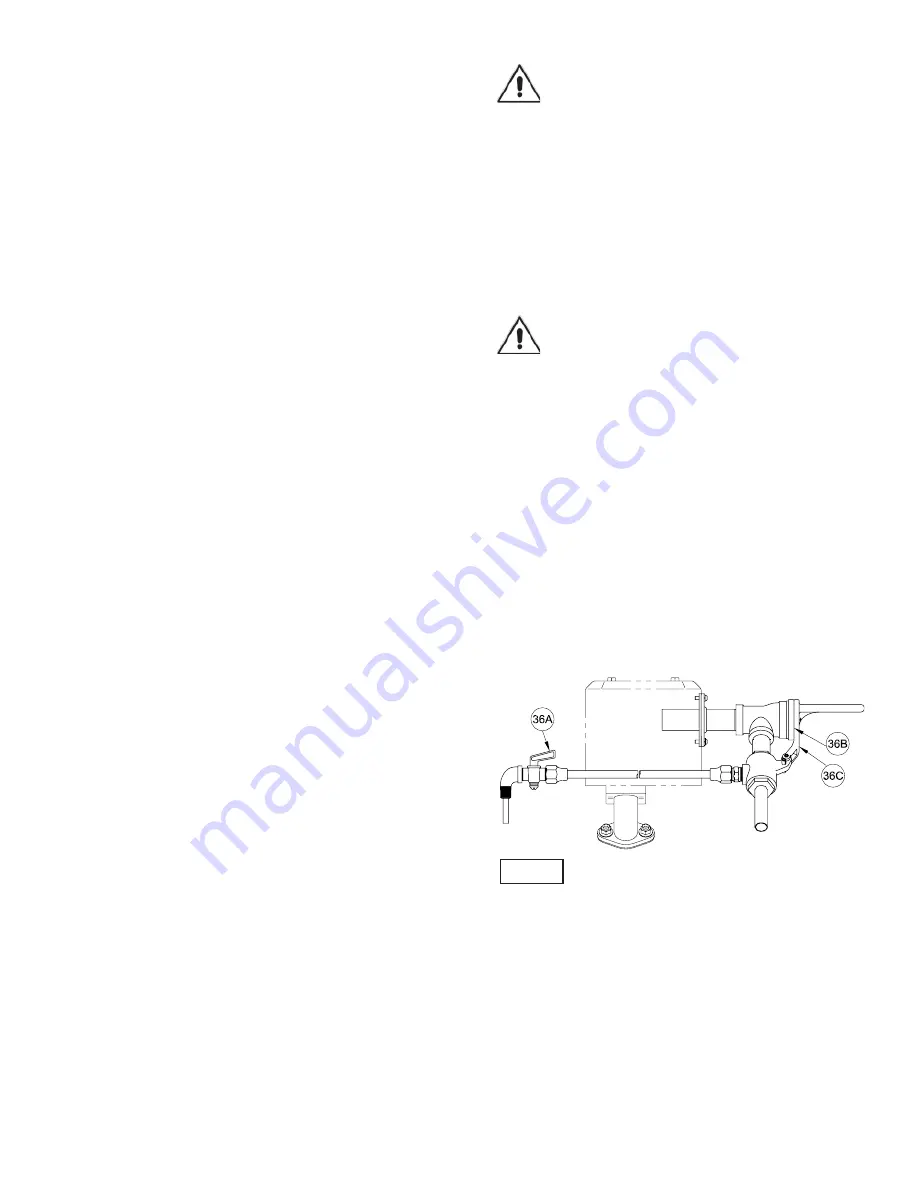
5
SECTION B: GENERAL INFORMATION
B-1) To the Purchaser:
Congratulations!
You are the owner of one of the fi nest
pumps on the market today. Barnes® Pumps are products
engineered and manufactured of high quality components.
Over one hundred years of pump building experience
along with a continuing quality assurance program combine
to produce a pump which will stand up to the toughest
applications.
This manual will provide helpful information concerning
installation, maintenance, and proper service guidelines.
B-2) Receiving:
Upon receiving the pump, it should be inspected for
damage or shortages. If damage has occurred, fi le a claim
immediately with the company that delivered the pump. If
the manual is removed from the packaging, do not lose or
misplace.
B-3) Storage:
Short Term-
Barnes pumps are manufactured for effi cient
performance following short inoperative periods in storage.
For best results, pumps can be retained in storage, as factory
assembled, in a dry atmosphere with constant temperatures
for up to six (6) months.
Long Term-
Any length of time exceeding six (6) months, but
not more than twenty four (24) months. The units should be
stored in a temperature controlled area, a roofed over walled
enclosure that provides protection from the elements (rain,
snow, wind-blown dust, etc.), and whose temperature can be
maintained b40 deg. F and +120 deg. F.
If extended high humidity is expected to be a problem, all
exposed parts should be inspected before storage and all
surfaces that have the paint scratched, damaged, or worn
should be recoated with a water base, air dry enamel paint.
All surfaces should then be sprayed with a rust-inhibiting oil.
Pump should be stored in its original shipping container. On
initial start up, rotate impeller by hand to assure seal and
impeller rotate freely.
B-4) Service Centers:
For the location of the nearest Barnes Service Center, check
your Barnes representative or Crane Pumps & Systems, Inc.,
Service Department in Piqua, Ohio, telephone (937) 778-8947
or Crane Pumps & Systems Canada, Inc., in Bramton, Ontario
(905) 457-6223.
SECTION C: INSTALLATION:
C-1) Location:
The pump should be located as near as possible to the liquid
to be pumped and in no case should the pump be more than
15 feet above the surface of the liquid supply. The pump
should always be as level as possible.
C-2) Suction System:
Connect suction pipe or hose to suction inlet. If hose is used,
it should be of the reinforced type to prevent collapsing under
suction. Make sure all suction system connections are tight
and free of air leaks, as even a very slight leak will greatly
reduce priming ability and pumping effi ciency.
CAUTION! - This pump should not be operated
without a strainer on the end of the suction line
to prevent sticks, stones, rags and other foreign
matter from being drawn into the impeller. The
strainer should be cleaned regularly to insure full fl ow.
C-3) Discharge System:
Connect discharge hose or pipe to discharge opening in
pump.
C-4) Lubrication:
The pump requires no lubrication. It is equipped with a
mechanical shaft seal which is lubricated by the liquid being
pumped. Lubrication of the engine should be as indicated in
the Engine Manual.
CAUTION! - DO NOT operate pump without liquid
in the pump body as operating pump dry will
result in damage to the seal.
SECTION D: OPERATION:
D-1) Priming:
Start engine; holding governor open for maximum speed will
decrease priming time. Open gas cock (36A) in line between
pump suction and exhaust primer (36), (See Figure 1). With
exhaust primer handle (36B) and cap (36C), close exhaust
opening, this diverts engine exhaust gasses through the
venturi which creates a vacuum in the pump. When a steady
spray of water is coming from the primer, open the exhaust
and close the gas cock. (Delay the procedure if spray is
not full and steady or false prime will result.) Full prime
can usually be detected by the engine “LOADING UP” as
pumping action begins.
SECTION E: PUMP SERVICE AND REPAIR:
E-1) Check Valve Service:
Remove cap screws (20) and pull check valve body (19)
from pump body (14).
CAUTION:
Do not pry with sharp
instrument, but rather bump off with a block of wood and
a hammer. This will expose the check valve assembly for
examination or repair.
Examine and replace any part showing wear or damage.
At reassembly. make sure that the LARGE weight is on the
CHECK VALVE BODY side of the gasket and that the HINGE
section of gasket is at TOP.
EXHAUST PRIMER ITEM (36)
Figure 1
Summary of Contents for 2020HC
Page 8: ...8 Figure 3 ...