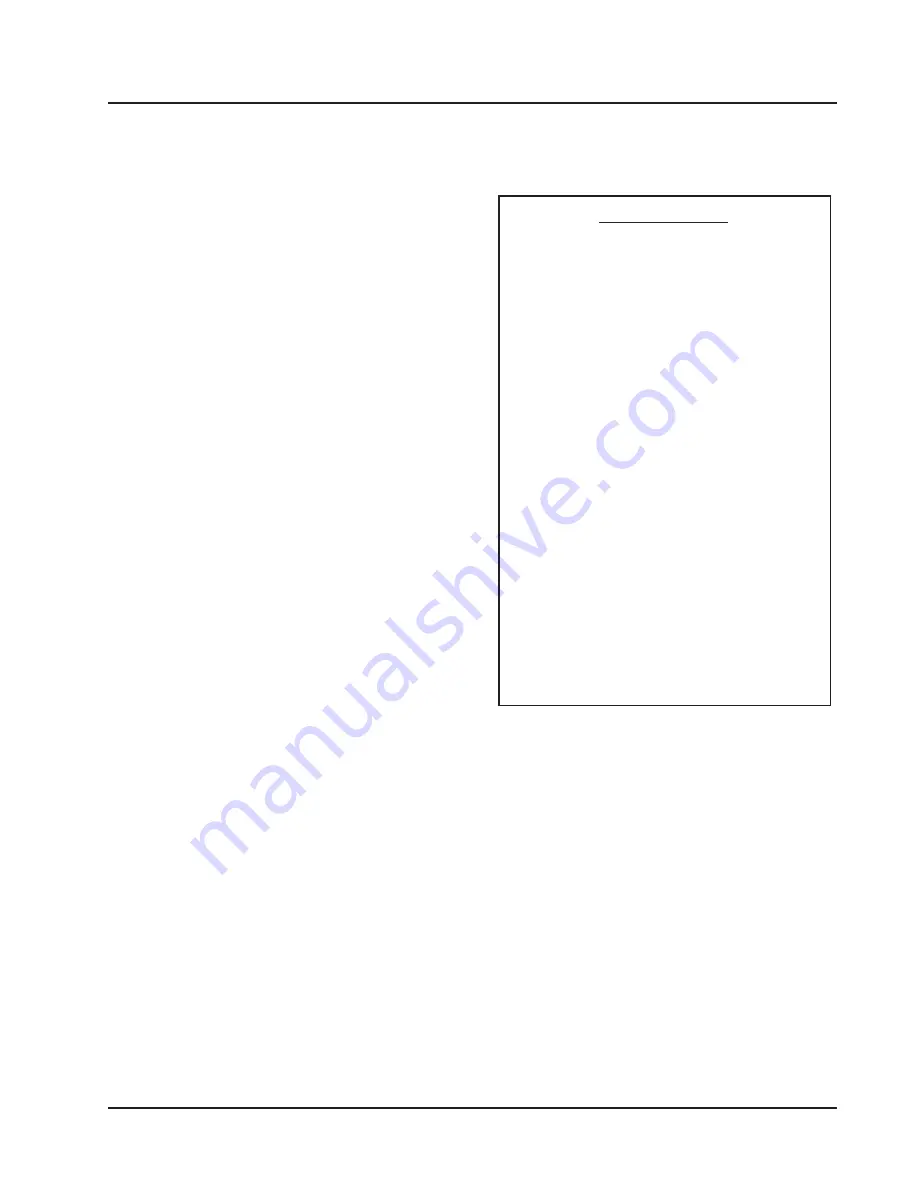
Manual 2100-403
Page 15
START UP
IMPORTANT INSTALLER NOTE
For improved start-up performance, wash the indoor coil
with a dishwashing detergent.
CRANKCASE HEATERS
WH421 units are provided with compressor crankcase
heat. WH483 and WH602 units are not provided with
crankcase heat. These units utilize scroll compressors
which do not require crankcase heat in this application.
The WH421 models have an insertion well-type heater
located in the lower section of the compressor housing
this is a self-regulating type heater that draws only
enough power to maintain the compressor at a safe
temperature on these units.
Some form of crankcase heat is essential to prevent
liquid refrigerant from migrating to the compressor,
causing oil pump out on compressor start-up and
possible valve failure due to compressing a liquid.
The decal in Figure 9 is affixed to all WH421 units
detailing start-up procedure. This is very important.
Please read carefully.
HIGH PRESSURE SWITCH
The models are supplied with a remote reset high
pressure switch. If tripped, this pressure switch may be
reset by turning the thermostat off then back on again.
THREE PHASE SCROLL COMPRESSOR
START UP INFORMATION
Scroll compressors, like several other types of
compressors, will only compress in one rotational
direction. Direction of rotation is not an issue with
single phase compressors since they will always start
and run in the proper direction.
However, three phase compressors will rotate in either
direction depending upon phasing of the power. Since
there is a 50-50 chance of connecting power in such a
way as to cause rotation in the reverse direction,
verification of proper rotation must be made. All three
phase scroll units incorporate a phase monitor to ensure
proper field wiring. See the Phase Monitor" on page 15
of this manual.
Verification of
proper rotation
must be made any time a
compressor is change or rewired. If improper rotation is
corrected at this time there will be no negative impact on
the durability of the compressor. However, reverse
operation for over one hour may have a negative impact
on the bearing due to oil pump out.
FIGURE 10
START UP LABEL
IMPORTANT
THESE PROCEDURES MUST BE FOL-
LOWED AT INITIAL START UP AND AT ANY
TIME POWER HAS BEEN REMOVED FOR
12 HOURS OR LONGER.
TO PREVENT COMPRESSOR DAMAGE
WHICH MAY RESULT FROM THE PRESENCE
OF LIQUID REFRIGERANT IN THE COMPRES-
SOR CRANKCASE:
1.
MAKE CERTAIN THE ROOM THERMOSTAT IS
IN THE “OFF“ POSITION. (THE COMPRESSOR
IS NOT TO OPERATE.)
2.
APPLY POWER BY CLOSING THE SYSTEM
DISCONNECT SWITCH. THIS ENERGIZES THE
COMPRESSOR HEATER WHICH EVAPO-
RATES THE LIQUID REFRIGERANT IN THE
CRANKCASE.
3.
ALLOW 4 HOURS OR 60 MINUTES PER
POUND OF REFRIGERANT IN THE SYSTEM AS
NOTED ON THE UNIT RATING PLATE, WHICH-
EVER IS GREATER.
4.
AFTER PROPER ELAPSED TIME THE THER-
MOSTAT MAY BE SET TO OPERATE THE COM-
PRESSOR.
5.
EXCEPT AS REQUIRED FOR SAFETY WHILE
SERVICING, DO NOT OPEN SYSTEM DISCON-
NECT SWITCH.
7961-411
NOTE: If compressor is allowed to run in reverse
rotation for several minutes, the compressor's
internal protector will trip.
All three phase ZR3 compressors are wired identical
internally. As a result, once the correct phasing is
determined for a specific system or installation,
connecting properly phased power leads to the same
Fusite terminal should maintain proper rotation
direction.
Verification of proper rotation direction is made by
observing that suction pressure drops and discharge
pressure rises when the compressor is energized.
Reverse rotation also results in an elevated sound level
over that with correct rotations, as well as, substantially
reduced current draw compared to tabulated values.
The direction of rotation of the compressor may be
changed by reversing any two line connections to the
unit.