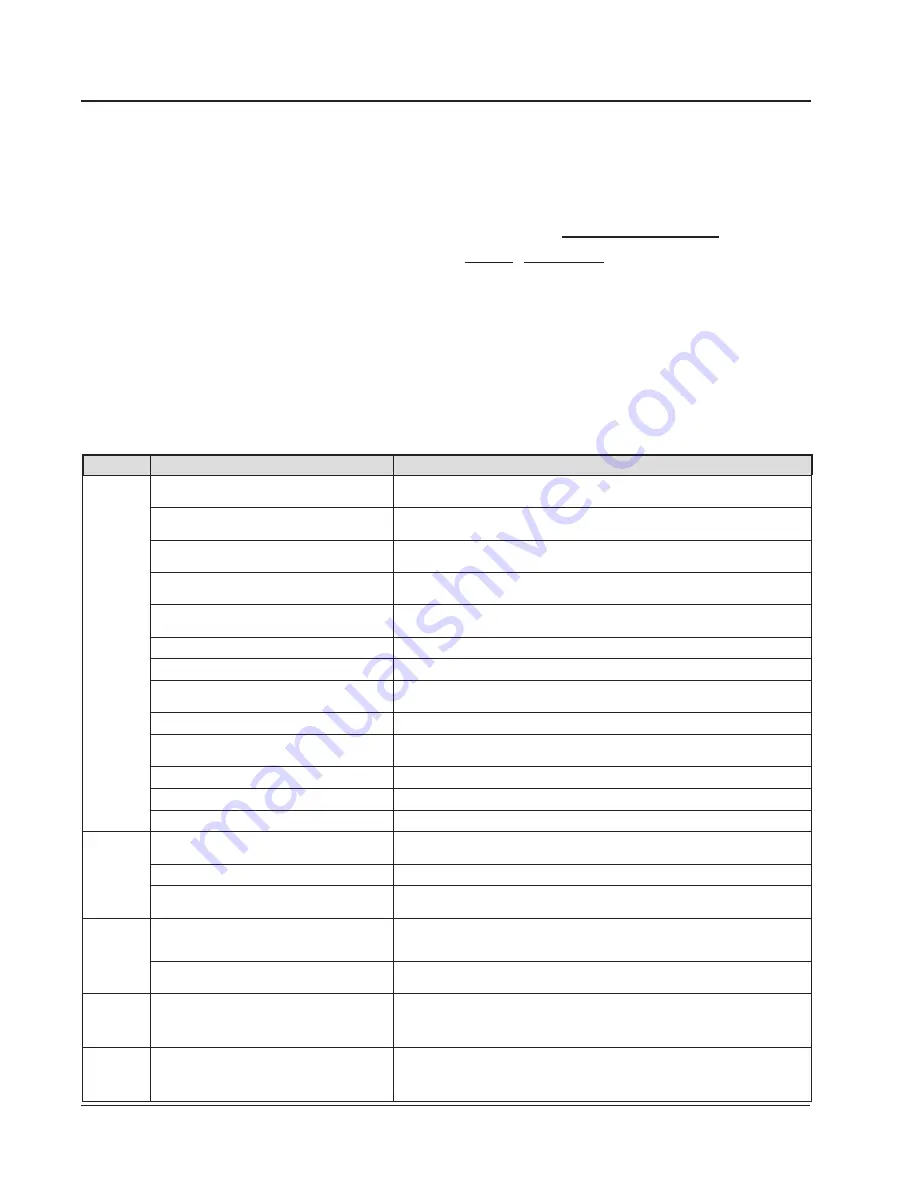
Manual 2100-541D
Page 20 of 28
TROUBLESHOOTING
TABLE 3
TROUBLESHOOTING
Sympton
Description, Check & Possible Causes
What & How to Check / Repair
Compressor
will not start
(heating or
cooling)
1. Check for LED illumination.
Is there an LED illuminated on the board (flashing)?
Yes = go to Step #2; No = go to Step #3
2. Check for error codes.
Is the LED flashing a Code?
Yes = go to Step #4; No = go to Step #8
3. Check for power at board.
Is there 24 volts AC between R and C?
Yes = go to Step #13; No = go to Step #9
4. Check codes.
What code is blinking?
Code "1", go to Step #6; Code "2", go to Step#7; Fast Blink, go to Step #5
5. Compressor delay active.
Wait for 5 minute delay or jump board's "speed up pins". Check for proper operation; if still needed, go back to Step #1.
6. Low pressure fault.
Check wiring circuit and unit pressures.
7. High pressure fault.
Check wiring circuit and unit pressures.
8. Check for Compressor input signal.
Is there 24 volts AC between Y and C?
Yes = go to Step #10; No = go to Step #11
9. No power to board.
The unit either does not have unit voltage, the transformer is bad or the unit wiring is incorrect.
10. Check for Compressor output signal.
Is there 24 volts AC between CC & C?
Yes = go to Step #12; No = go to Step #13
11. No "Y" compressor input signal.
Check thermostat wiring, incorrect phase of unit (see section on Phase Monitor), and finally unit wiring.
12. No "CC" compressor output signal.
Check compressor contactor for proper operation and finally check compressor.
13. Faulty board.
Replace defrost board.
Fan outdoor
motor does
not run
(cooling or
heating except
during defrost)
Heat pump control defective
Check across fan relay on heat pump control. (Com-NC)
Replace heat pump control.
Motor defective
Check for open or shorted motor winding. Replace motor.
Motor capacitor defective
Check capacitor rating. Check for open or shorted capacitor. Replace capacitor.
Reversing
valve does not
energize
(heating only)
Heat pump control defective
Check for 24V between RV-C and B-C.
1. Check control circuit wiring.
2. Replace heat pump control.
Reversing valve solenoid coil defective
Check for open or shorted coil.
Replace solenoid coil.
Unit will not go
into defrost
(heating only)
Temperature sensor or heat pump control defective
Disconnect temperature sensor from board and jumper across "SPEEDUP" terminals and "SEN
JMP" terminals. This should cause the unit to go through a defrost cycle within one minute.
1. If unit goes through defrost cycle, replace temperature sensor.
2. If unit does not go through defrost cycle, replace heat pump control.
Unit will not
come out of
defrost
(heating only)
Temperature sensor or heat pump control defective
Jumper across "SPEEDUP" terminal.
This should cause the unit to come out of defrost within one minute.
1. If unit comes out of defrost cycle, replace temperature sensor.
2. If unit does not come out of defrost cycle, replace heat pump control.
SOLID STATE HEAT PUMP CONTROL
TROUBLESHOOTING PROCEDURE
1.
NOTE:
A thorough understanding of the defrost
cycle sequence is essential. Review that section
earlier in this manual prior to troubleshooting the
control.
Turn on AC power supply to unit.
2. Turn thermostat blower switch to “fan on” – the
indoor blower should start. (If it doesn’t,
troubleshoot indoor unit and correct problem.)
3. Turn thermostat blower to “auto” position. Indoor
blower should stop.
NOTE:
Many models have a
1-minute blower time delay on “off” command;
wait for this to time-out.
4. Set system switch to “heat” or “cool”. Adjust
thermostat to call for heat or cool. The indoor
blower, compressor and outdoor fan should start.
NOTE: If there was no power to 24 volt transformer,
the compressor and outdoor fan motor will
not start for 5 minutes. This is because of
the compressor short cycle protection.
LED BLINK CODES
BLINK FUNCTION
Slow
Normal function (1.0 sec on/1.0 sec off)
Fast
Compressor Delay timer active (0.1 sec on/0.1 sec off)
1
Low pressure switch failure
2
High pressure switch failure/“Soft” Lockout
3
Defrost mode active
4
High pressure switch failure/“Hard” Lockout