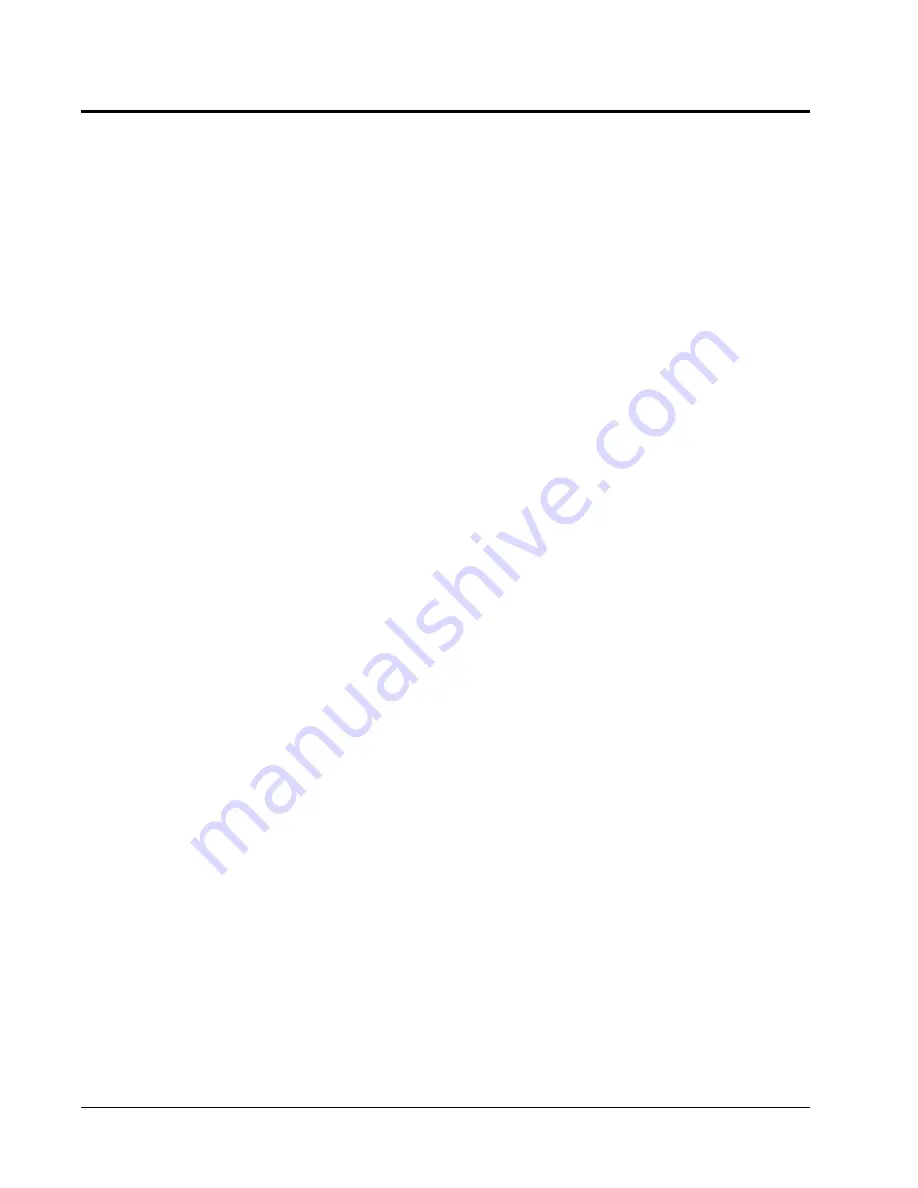
Manual 2100-344
Page
12
START UP AND OPERATION
the reversing valve solenoid constantly whenever the system
switch on subbase is placed in “Heat” position, the “B”
terminal being constantly energized from R. A thermostat
demand for heat completes R-Y circuit, pulling in
compressor contactor starting compressor and outdoor
motor. R-G also make starting indoor blower motor.
DEFROST CYCLE
The defrost cycle is controlled by temperature and time on
the solid state heat pump control.
When the outdoor temperature is in the lower 40° F
temperature range or colder, the outdoor coil temperature is
32°F or below. This temperature is sensed by the coil
sensor mounted near the bottom of the outdoor coil. Once
the coil temperature reaches 32°F or below, the coil sensor
sends a signal to the control logic of the heat pump control
and defrost timer will start.
After 60 (90 or 30) minutes at 32°F or below, the heat pump
control will place the system in the defrost mode.
During the defrost mode, the refrigerant cycle switches back
to the cooling cycle, the outdoor motor stops, electric heaters
are energized, and hot gas passing through the outdoor coil
melts any accumulated frost. When the temperature rises to
approximately 57° F, the coil sensor will send a signal to the
heat pump control which will return the system to heating
operations automatically.
If some abnormal or temporary condition such as a high
wind causes the heat pump to have a prolonged defrost
cycle, the heat pump control will restore the system to
heating operation automatically after 10 minutes.
There are three settings on the heat pump control -- 30
minutes, 60 minutes, and 90 minutes. Most models are
shipped wired on the 60 minutes setting for greatest
operating economy. If special circumstances require a
change to another time, remove wire connected to terminal
60 and reconnect to desired terminal. (See Figure 11.)
There is a cycle speed up jumper on the control. This can be
used to reduce the time between defrost cycle operation
without waiting for time to elapse.
There is an initial defrost (sen jmp) jumper on the control
that can be used at any outdoor ambient during the heating
cycle to simulate a 0° coil temperature. This can be used to
check defrost operation of the unit without waiting for the
outdoor ambient to fall into the defrost region.
START UP NOTES
For improved start up performance, wash the indoor coil
with dishwasher detergent
THREE PHASE SCROLL COMPRESSOR
START UP INFORMATION
Scroll compressors, like several other types of compressors,
will only compress in one rotational direction. Direction of
rotation is not an issue with single phase compressors since
they will always start and run in the proper direction.
However, three phase compressors will rotate in either
direction depending upon phasing of the power. Since there
is a 50-50 chance of connecting power in such a way as to
cause rotation in the reverse direction, verification of proper
rotation must be made. Verification of proper rotation
direction is made by observing that suction pressure drops
and discharge pressure rises when the compressor is
energized. Reverse rotation also results in an elevated
sound level over that with correct rotation, as well as,
substantially reduced current draw compared to tabulated
values.
Verification of proper rotation must be made at the time
the equipment is put into service. If improper rotation is
corrected at this time there will be no negative impact on the
durability of the compressor. However, reverse operation for
over one hour may have a negative impact on the bearing
due to oil pump out.
NOTE: If compressor is allowed to run in reverse
rotation for several minutes the compressor’s
internal protector will trip.
All three phase ZR*3 compressors are wired identically
internally. As a result, once the correct phasing is
determined for a specific system or installation, connecting
properly phased power leads to the same Fusite terminals
should maintain proper rotation direction.
The direction of rotation of the motor may be changed by
reversing any two line connections to the unit.
SEQUENCE OF OPERATION
COOLING
– Circuit R-Y makes at thermostat pulling in
compressor contactor starting the compressor and outdoor
motor. The G (indoor motor) circuit is automatically
completed on any call for cooling operation, or can be
energized by manual fan switch on subbase for constant air
circulation.
HEATING
– A 24V solenoid coil on reversing valve
controls heating cycle operation. Two thermostat options,
one allowing “AUTO” changeover from cycle to cycle and
the other constantly energizing solenoid coil during heating
season and thus eliminating pressure equalization noise
except during defrost, are to be used. On “AUTO” option, a
circuit is completed from R-W1 and R-Y on each heating
“On” cycle energizing reversing valve solenoid and pulling
in compressor contactor starting compressor and outdoor
motor. R-G also make starting indoor blower motor. Heat
pump heating cycle now in operation. The second energizes
Summary of Contents for PH1224
Page 15: ...Manual 2100 344 Page 13 FIGURE 11 HEAT PUMP CONTROL BOARD MIS 1191...
Page 21: ...Manual 2100 344 Page 19 Wiring Diagram 4098 123 printed from CAD to get size needed...
Page 22: ...Manual 2100 344 Page 20 Wiring Diagram 4098 124 printed from CAD to get size needed...
Page 23: ...Manual 2100 344 Page 21 Wiring Diagram 4098 211 printed from CAD to get size needed...