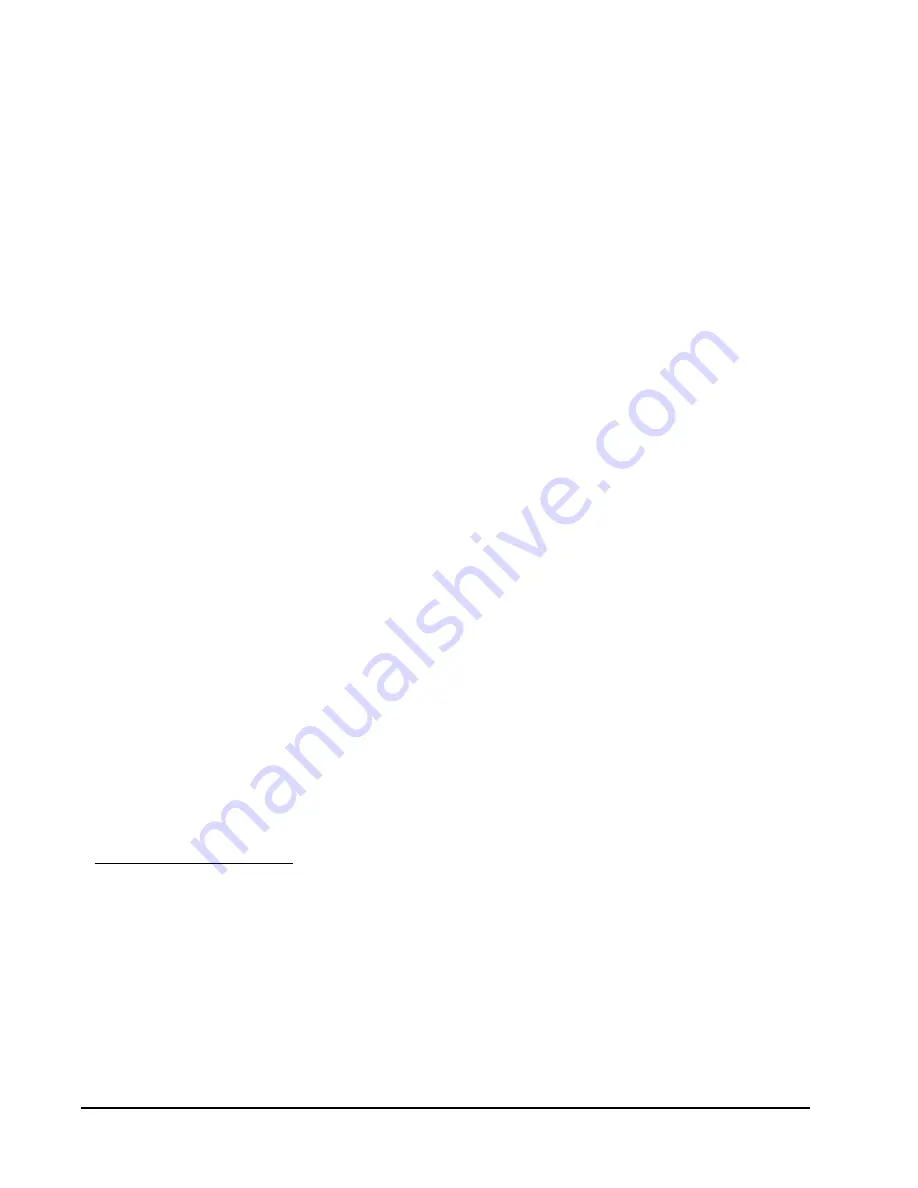
Manual 2100-719
Page
16 of 25
SEQUENCE OF OPERATION
COOLING STAGE 1
– Circuit R-Y makes at thermostat
pulling in compressor contactor, starting the compressor and
outdoor motor. The G (indoor motor) circuit is automatically
completed on any call for cooling operation or can be
energized by manual fan switch on subbase for constant air
circulation.
COOLING STAGE 2
– Circuit R-Y1 makes at the
thermostat energizing the 2nd stage solenoid in the
compressor. Default position is not energized. Compressor
will run at low capacity until this solenoid is energized.
HEATING STAGE 1
– A 24V solenoid coil on reversing
valve controls heating cycle operation. Two thermostat
options, one allowing “Auto” changeover from cycle to cycle
and the other constantly energizing solenoid coil during
heating season and thus eliminating pressure equalization
noise except during defrost, are to be used. On “Auto” option
a circuit is completed from R-B and R-Y on each heating
“on” cycle, energizing reversing valve solenoid and pulling
in compressor contactor starting compressor and outdoor
motor. R-G also make starting indoor blower motor. Heat
pump heating cycle now in operation. The second option
has no “Auto” changeover position, but instead energizes
the reversing valve solenoid constantly whenever the system
switch on subbase is placed in “Heat” position, the “B”
terminal being constantly energized from R. A thermostat
demand for Stage 1 heat completes R-Y circuit, pulling in
compressor contactor starting compressor and outdoor motor.
R-G also make starting indoor blower motor.
HEATING STAGE 2
– Circuit R-Y2 makes at the
thermostat energizing the 2nd stage solenoid in the
compressor.
PRESSURE SERVICE PORTS
High and low pressure service ports are installed on all units
so that the system operating pressures can be observed.
Pressure tables can be found later in the manual covering all
models. It is imperative to match the correct pressure table
to the unit by model number. See Tables 5A & 5B.
This unit employs high-flow Coremax valves instead of the
typical Shrader type valves.
WARNING! Do NOT use a Schrader valve core removal
tool with these valves. Use of such a tool could result in
eye injuries or refrigerant burns!
To change a Coremax valve without first removing the
refrigerant, a special tool is required which can be obtained
at www.fastestinc.com/en/SCCA07H. See the replacement
parts manual for replacement core part numbers.
DEFROST CYCLE
The defrost cycle is controlled by temperature and time on
the solid state heat pump control.
When the outdoor temperature is in the lower 40°F
temperature range or colder, the outdoor coil temperature is
32°F or below. This coil temperature is sensed by the coil
temperature sensor mounted near the bottom of the outdoor
coil. Once coil temperature reaches 30°F or below, the
coil temperature sensor sends a signal to the control logic
of the heat pump control and the defrost timer will start
accumulating run time.
After 30, 60 or 90 minutes of heat pump operation at 30°F
or below, the heat pump control will place the system in the
defrost mode.
During the defrost mode, the refrigerant cycle switches back
to the cooling cycle, the outdoor motor stops, electric heaters
are energized, and hot gas passing through the outdoor coil
melts any accumulated frost. When the temperature rises to
approximately 57°F, the coil temperature sensor will send a
signal to the heat pump control which will return the system
to heating operations automatically.
If some abnormal or temporary condition such as a high wind
causes the heat pump to have a prolonged defrost cycle, the
heat pump control will restore the system to heating operation
automatically after 8 minutes.
The heat pump defrost control board has an option of 30, 60
or 90-minute setting. By default, this unit is shipped from
the factory with the defrost time on the 60 minute pin. If
circumstances require a change to another time, remove the
wire from the 60-minute terminal and reconnect to the desired
terminal. Refer to Figure 8.
There is a cycle speed up jumper on the control. This can be
used for testing purposes to reduce the time between defrost
cycle operation without waiting for time to elapse.
Use a small screwdriver or other metallic object, or another
¼ inch QC, to short between the
SPEEDUP
terminals to
accelerate the HPC timer and initiate defrost.
Be careful not to touch any other terminals with the
instrument used to short the
SPEEDUP
terminals. It may
take up to 10 seconds with the
SPEEDUP
terminals shorted
for the speedup to be completed and the defrost cycle to start.
As soon as the defrost cycle kicks in remove the shorting
instrument from the SPEEDUP terminals.
Otherwise the
timing will remain accelerated and run through the 1-minute
minimum defrost length sequence in a matter of seconds and
will automatically terminate the defrost sequence.
There is an initiate defrost jumper (sen jump) on the control
that can be used at any outdoor ambient during the heating
cycle to simulate a 0° coil temperature.
This can be used to check defrost operation of the unit without
waiting for the outdoor ambient to fall into the defrost region.
By placing a jumper across the
SEN JMP
terminals (a ¼ inch
QC terminal works best) the defrost sensor mounted on the
outdoor coil is shunted out & will activate the timing circuit.
This permits the defrost cycle to be checked out in warmer
weather conditions without the outdoor temperature having to
fall into the defrost region.
In order to terminate the defrost test the
SEN JMP
jumper
must be removed. If left in place too long, the compressor
could stop due to the high pressure control opening because
of high pressure condition created by operating in the cooling
mode with outdoor fan off. Pressure will rise fairly fast
as there is likely no actual frost on the outdoor coil in this
artificial test condition.
There is also a 5-minute compressor time delay function built
into the HPC. This is to protect the compressor from short
cycling conditions. The board’s LED will have a fast blink
rate when in the compressor time delay. In some instances, it
is helpful to the service technician to override or speed up this
timing period, and shorting out the
SPEEDUP
terminals for a
few seconds can do this.