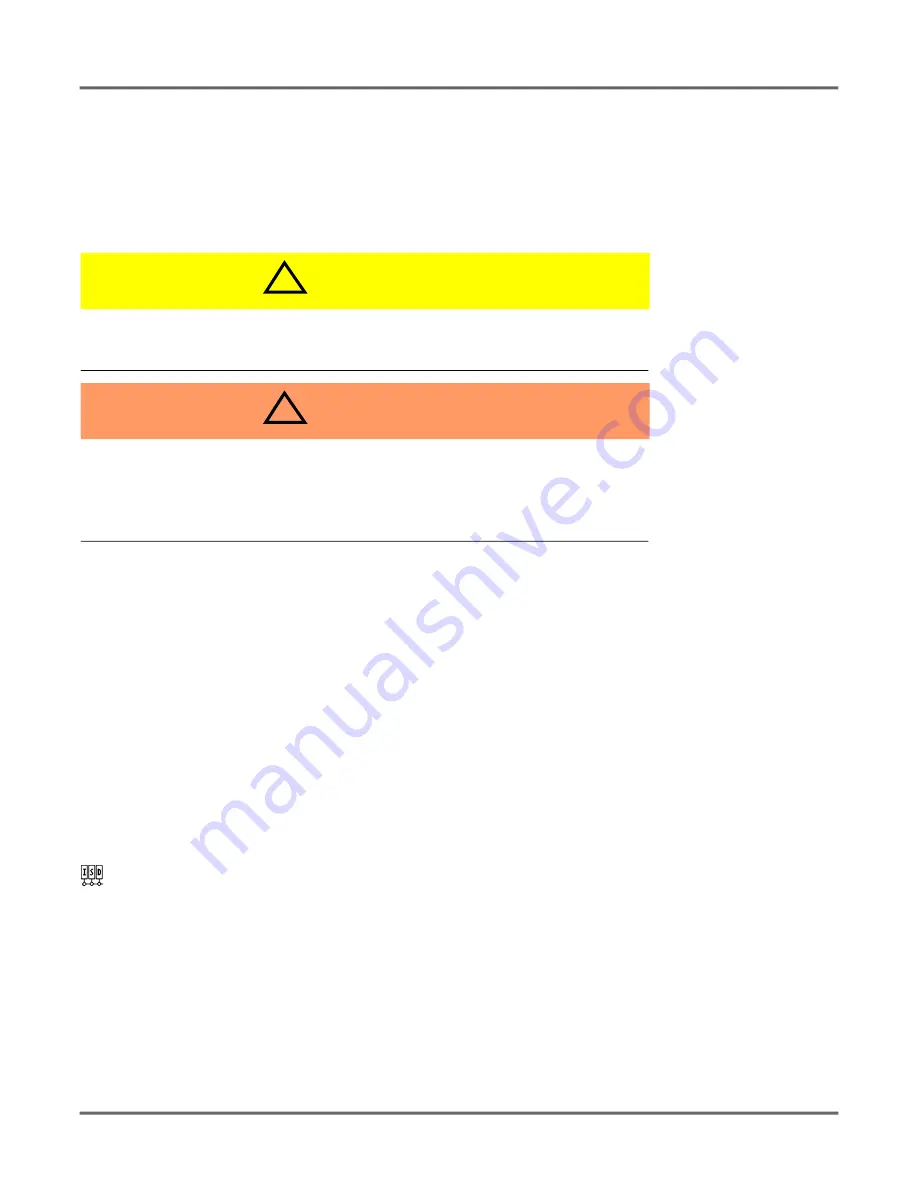
8
© Banner Engineering Corp. www.bannerengineering.com
I
NSTALLATION
I
NSTRUCTIONS
3.5. Resetting the Inputs
The reset function forces a local confirmation that the safety outputs are switched on after closing the movable safety guard.
If the moveable guard is opened using a sensor with a reset function, close and open the reset button within 0.25 seconds (minimum) to 1 second
(maximum), after the guard has been closed.
The reset function only applies to the sensor with the reset functionality. This reset feature allows for a local reset at a given guard but does not
allow for an entire safety system reset. If a chain of sensors is cascaded (see
Wire the Switch in Series on page 12
), the reset function only
applies to SI-RF 3. If SI-RF 1 or 2 are opened then closed, the outputs will switch on after the guard is closed, without actuating the reset button.
CAUTION
!
WHEN POWER IS SWITCHED ON AND THE GUARD IS IN THE CLOSED POSITION, THE SAFETY OUT
-
PUTS SWITCH ON WITHOUT ACTUATING THE RESET BUTTON.
•
Automatic reset at power-up must be addressed in the customer's controls.
WARNING
!
USE OF AUTO OR MANUAL RESTART
Failure to follow these instructions could result in serious injury or death.
•
Application of power to the Banner device, the closing of the movable safety guard, or the reset of a manual
restart condition MUST NOT initiate dangerous machine motion. Design the machine control circuitry so
that one or more initiation devices must be engaged (in a conscious act) to start the machine - in addition
to the Banner device going into Run mode.
3.6. Auxiliary Output/Information
The PNP output models (
SI-RFS
and
SI-RFP
) have a diagnostic PNP output. The PNP Diagnostic is not safety-related.
The PNP Diagnostic output indicates whether the right actuator has been detected (for example, the door is closed).
•
Output high (conducting) - Actuator not detected
•
Output low (open or non-conducting) - Actuator detected
When the
SI-RFS
sensors are cascaded, the output only signifies the actuator status of its sensor, not the others in the string. With manual reset
models (
SI-RFSL
), the auxiliary output changes back to the low state when the actuator is sensed (does not wait for the reset).
Note that the switching point of the auxiliary output might not match the switching point of the safety outputs.
The ISD models (
SI-RFD
) do not have an auxiliary output.
3.7. In-Series Diagnostic Information
The information transmitted via the In-Series Diagnostic (ISD) interface is not safety-related. The diagnostic technology allows a wide range of
sensor information to be loaded into the machine control system.
To interpret the information, Banner diagnostic modules are available, including the
SI-RF-DM1
and
-DM2
Diagnostic Modules and the
SC10-2roe
or
XS26-ISDx
Safety Controller. Refer to the instruction manuals for detailed information on the diagnostic devices. By means of
diagnostics, the following information can be transmitted, among others:
•
Door status (open, closed, or faulted)
•
Detection of misalignment (marginal signal strength of RF field)
•
Detection of under-voltages in the series connection
•
Attempts to defeat an RF gate switch
For a complete list of the diagnostics information, see
Information Available via ISD on page 21
At this time this information can be refined via the following interfaces: