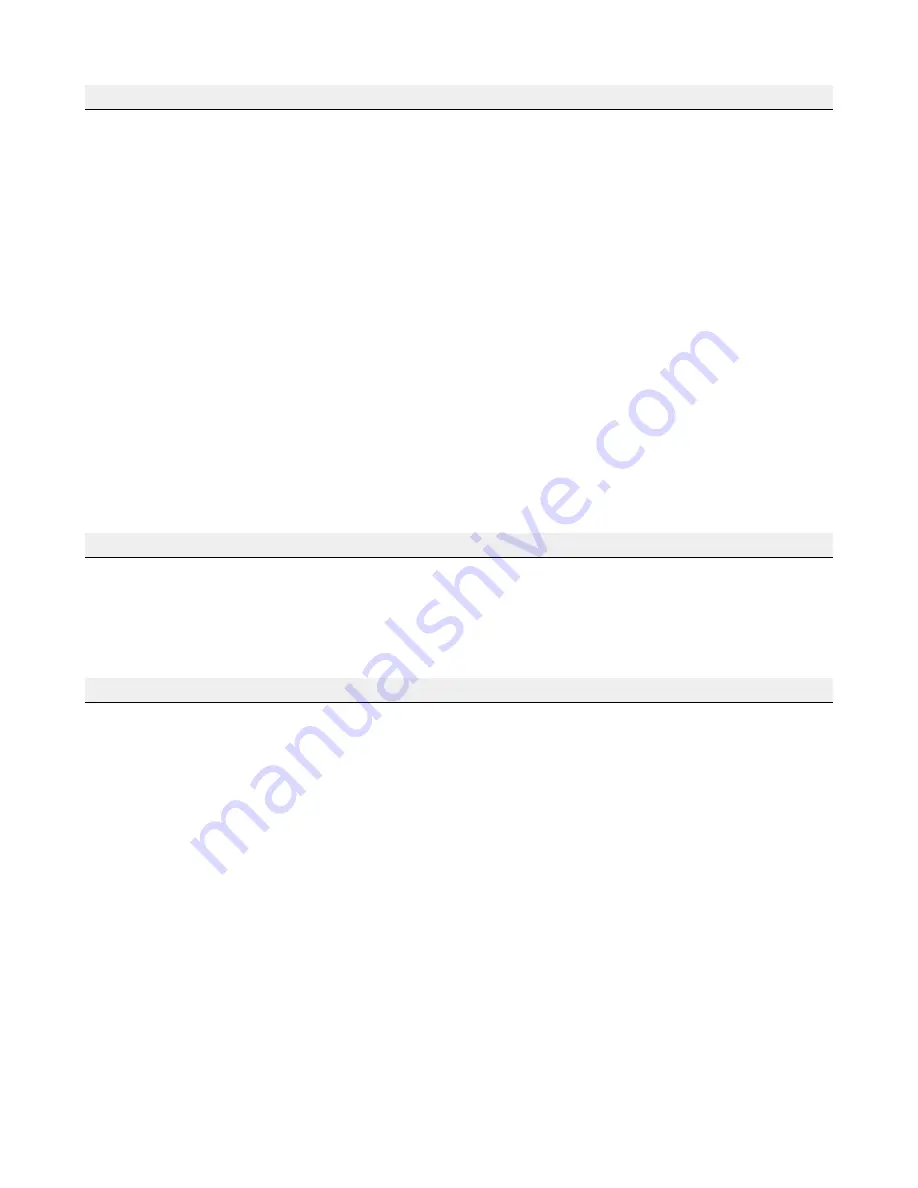
P
Part-Revolution Clutch
A type of clutch that may be engaged or disengaged
during the machine cycle. Part-revolution clutched
machines use a clutch/brake mechanism, which can
arrest machine motion at any point in the stroke or
cycle.
Pass-Through Hazard
A pass-through hazard is associated with
applications where personnel may pass through a
safeguard (which issues a stop command to remove
the hazard), and then continues into the guarded
area, such as in perimeter guarding. Subsequently,
their presence is no longer detected, and the related
danger becomes the unexpected start or restart of
the machine while personnel are within the guarded
area.
Point of Operation
The location of a machine where material or a
workpiece is positioned and a machine function is
performed upon it.
PSDI (Presence-Sensing Device Initiation)
An application in which a presence-sensing device is
used to actually start the cycle of a machine. In a
typical situation, an operator manually positions a
part in the machine for the operation. When the
operator moves out of the danger area, the presence
sensing device starts the machine (no start switch is
used). The machine cycle runs to completion, and
the operator can then insert a new part and start
another cycle. The presence sensing device
continually guards the machine. Single-break mode
is used when the part is automatically ejected after
the machine operation. Double-break mode is used
when the part is both inserted (to begin the
operation) and removed (after the operation) by the
operator. PSDI is commonly confused with "Trip
Initiate." PSDI is defined in OSHA CFR1910.217.
Banner safety light screen systems may not be used
as PSDI devices on mechanical power presses, per
OSHA regulation 29 CFR 1910.217.
Q
Qualified Person
A person who, by possession of a recognized degree
or certificate of professional training, or who, by
extensive knowledge, training and experience, has
successfully demonstrated the ability to solve
problems relating to the subject matter and work.
R
Receiver
The light-receiving component of a safety light
screen system, consisting of a row of synchronized
phototransistors. The receiver, together with the
emitter (placed opposite), creates a "screen of light"
called the defined area.
Reduced Resolution
A feature that allows a safety light screen system to
be configured to produce an intentionally disabled
light beam(s) within the light screen, which increases
the minimum object sensitivity. The disabled beam(s)
appears to move up and down (float) to allow the
feeding of an object through the defined area at any
point without tripping the safety outputs (for
example, OSSDs) and causing a Auto Start/Restart
(Trip) or Manual Start/Restart (Latch) condition.
Sometimes called Floating Blanking.
Reset
The use of a manually operated switch to restore the
safety outputs to the On state from a lockout or a
Manual Start/Restart (Latch) condition.
Resolution
See Minimum Object Sensitivity.
EZ-SCREEN
®
14/30 mm Safety Light Screen
98
www.bannerengineering.com - Tel: + 1 888 373 6767