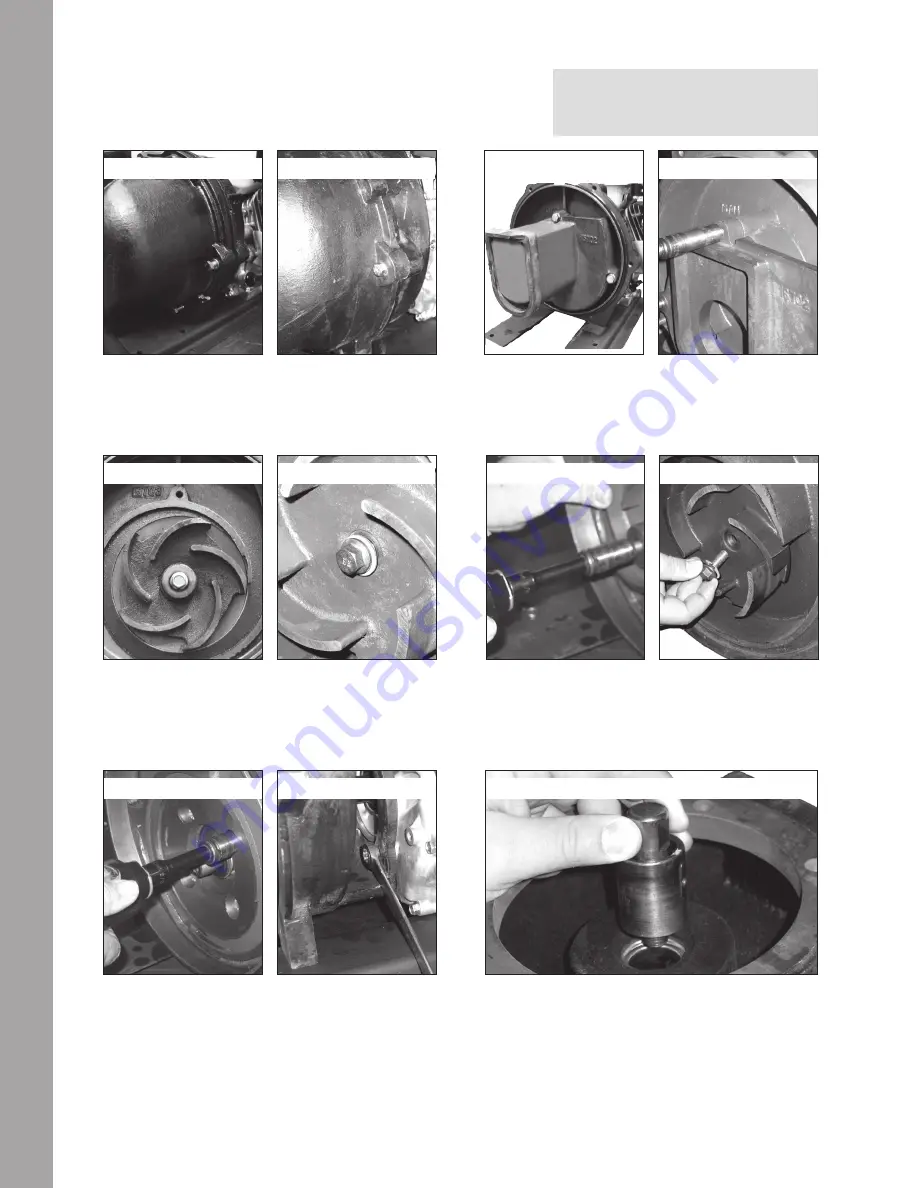
C O N N E C T W I T H C O N F I D E N C E
™
4
222 SERIES
333 & 444 SERIES
DISASSEMBLY INSTRUCTIONS:
Remove the (6) bolts (222: 12715A, 333/444: V20011SS) and lock
washers (222: V10118, 333/444: V20018) that hold the pump body
assembly onto the rear bracket. Remove the body from the remaining
pump assembly.
2
1
3
4
Remove the (4) bolts (222: 12715A, 333/444: 18027) and lock
washers (222: 12901, 333/444: V20018) that hold the rear bracket
to the drive unit. With the 4 bolts removed, the rear bracket can be
removed from the drive unit. With the pump completely disas-
sembled, clean all of the reusable parts thoroughly removing any
traces of gasket material with a scraper or wire brush. Remove any
corrosion on the sealing surfaces of the pump components.
5
222 SERIES
333 & 444 SERIES
222 SERIES
333 & 444 SERIES
222 SERIES
333 & 444 SERIES
222 SERIES
333 & 444 SERIES
NOTE:
If bracket shims have been installed from the factory,
the same number of shims will need to be reinstalled
Remove the impeller bolt (222: 12765A, 333/444: 16765) from the
impeller (222: 15772, 333/444: 16772). Remove the impeller bolt
gasket from the impeller.
Remove the cup seal half from the rear bracket. This may be done
by using a round object such as a socket and tapping it with a
hammer as shown in the photo. If necessary, remove the inlet and
outlet flanges, the flange gaskets by removal of the flange screws
and lock washers.
6
5
222, 333 & 444 SERIES
Remove the (3) bolts (222: 12715A, 333/444: V20011SS) and lock
washers (222: V10118, 333/444: V20018) holding the volute to the
rear bracket. Remove the volute (222: 15702, 333/444: 16702) from
the remaining pump assembly. Replace checkvalve if needed.
Screw the supplied (222: 7/16″-14, 333/444: 9/16″-12) hex head cap
screw (16099) into the threaded hole in the impeller. As it tightens,
the impeller will pull off the shaft. Remove the hex head cap screw
once the impeller is removed. If reusing the pump impeller, remove
the primary ring of the seal (222: 12733V, 333/444: 16713) and the
impeller key (222: 12902A, 333/444: 16901).