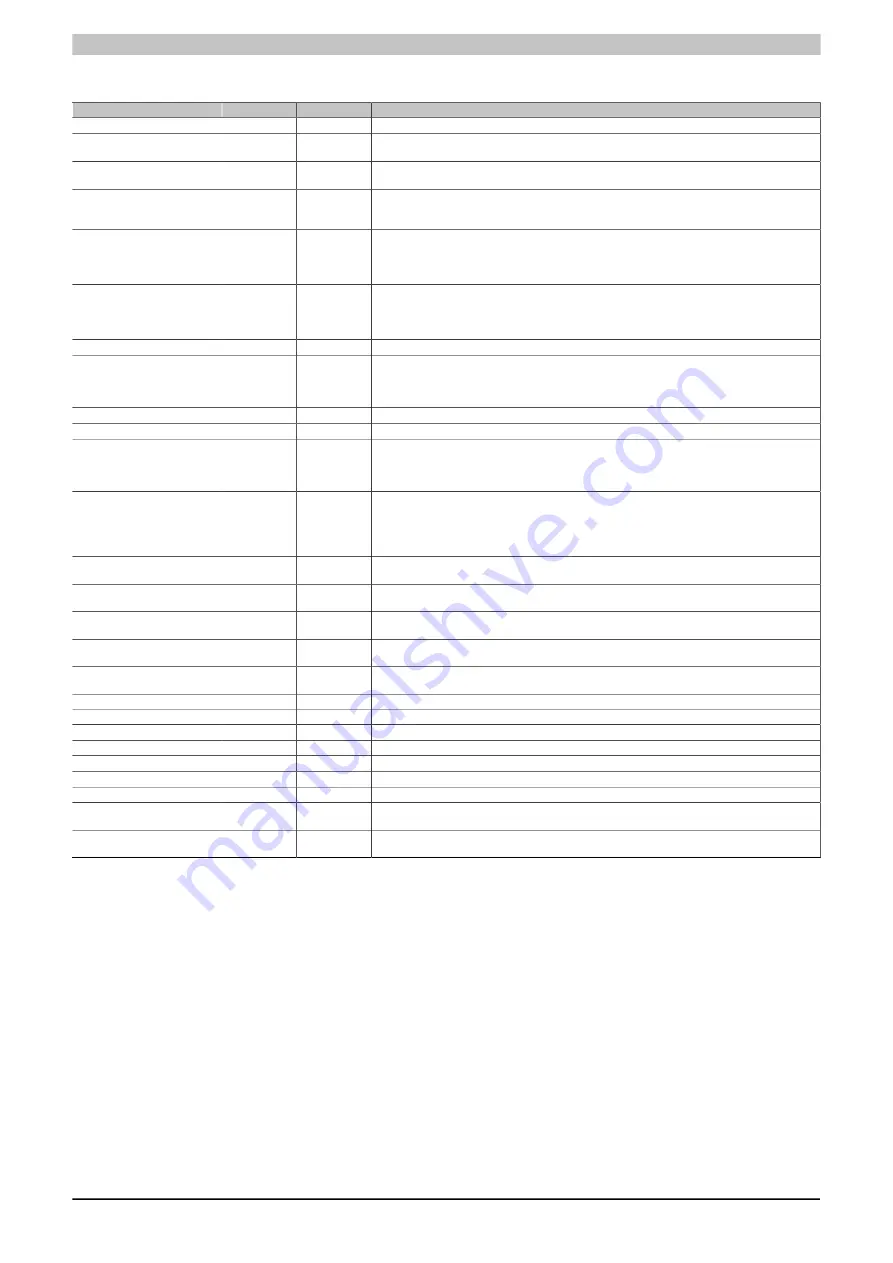
Technical data • General motor data
24
8JSA user's manual V1.00
10.2 Formula symbols
Term
Symbol
Unit
Description
Nominal speed
n
N
rpm
Nominal speed of the motor
Nominal torque
M
N
Nm
The nominal torque is output by the motor (n = n
N
) when the nominal current is being drawn. This
is possible for any length of time if the ambient conditions are correct.
Nominal power
P
N
kW
The nominal power is supplied by the motor when n = n
N
. This is possible for any length of time
if the ambient conditions are correct.
Nominal current
I
N
A
The nominal current is the RMS value for the phase current (current in the motor supply line)
when generating the nominal torque at the nominal speed. This is possible for any length of time
if the ambient conditions are correct.
Stall torque
M
0
Nm
The stall torque is output by the motor at the speed n
0
and when the stall current is being applied.
This is possible for any length of time if the ambient conditions are correct. Speed n
0
must be high
enough for the temperature in all windings to be homogeneous and stationary (for B&R motors,
n
0
= 50 rpm). The continuous torque is reduced when the motor is at a complete standstill.
Stall current
I
0
A
The stall current is the RMS value of the phase current (current in the motor supply line) for
generating the stall torque at speed n
0
. This is possible for any length of time if the ambient
conditions are correct. Speed n
0
must be high enough for the temperature in all windings to be
homogeneous and stationary (for B&R motors, n
0
= 50 rpm).
Peak torque
M
max
Nm
The peak torque is briefly output by the motor when the peak current is being drawn.
Peak current
I
max
A
The peak current is the RMS value of the phase current (current in the motor supply line) for
generating the peak torque. This is only permitted for a short time. The peak current is determined
by the magnetic circuit. Exceeding this value for a short time can cause irreversible damage
(demagnetization of the magnet material).
Maximum speed
n
max
rpm
Maximum motor speed. This is a mechanical condition (centrifugal force, bearing wear).
Average speed
n
average
rpm
Average speed for one cycle
Torque constant
K
T
Nm/A
The torque constant specifies the torque generated by the motor at 1 Arms phase current. This
value applies at a motor temperature of 20°C. If the temperature increases, the torque constant is
reduced (typically down to 10%). If the current increases, the torque constant is reduced (typically
starting at twice the value of the nominal current).
Voltage constant
K
E
V/1000 rpm
The voltage constant specifies the RMS value (phase-phase) of the reverse voltage induced by
the motor at a speed of 1000 rpm (EMF). This value applies at a motor temperature of 20°C.
When the temperature increases, the voltage constant is reduced (usually down to 5%). If the
current increases, the voltage constant is reduced (typically starting at twice the value of the
nominal current).
Stator resistance
R
2ph
Ohm
Resistance measured in ohms between two motor leads (phase-phase) at 20°C winding temper-
ature. On B&R motors, the windings use a star connection.
Stator inductance
L
2ph
mH
Winding inductance measured between two motor leads. Stator inductance depends on the rotor
position.
Electrical time constant
t
el
ms
Corresponds to 1/5 of the time needed for the stator current to stabilize with constant operating
conditions.
Thermal time constant
t
therm
Min
Corresponds to 1/5 of the time needed for the motor temperature to stabilize with constant op-
erating conditions.
Moment of inertia without
brake
J
kgcm²
Moment of inertia for a motor without a holding brake
Weight without brake
m
kg
Mass of motor without holding brake
Moment of inertia of brake
J
Br
kgcm²
Moment of inertia for the built-in holding brake
Mass of brake
m
Br
kg
Mass of built-in holding brake
Brake holding torque
M
Br
Nm
Minimum torque required to hold the rotor when the brake is activated
Installed load
P
on
W
Installed load for the built-in holding brake
Installed current
I
on
A
Installed current for the built-in holding brake
Connection voltage
U
on
V
Operating voltage for the built-in holding brake
Activation delay
t
on
ms
Delay time required for the holding torque of the brake to be established after the operating
voltage has been removed from the holding brake
Release delay
t
off
ms
Delay time required until the holding torque of the holding brake is reduced by 90% (the brake is
released) after operating voltage has been returned to the holding brake