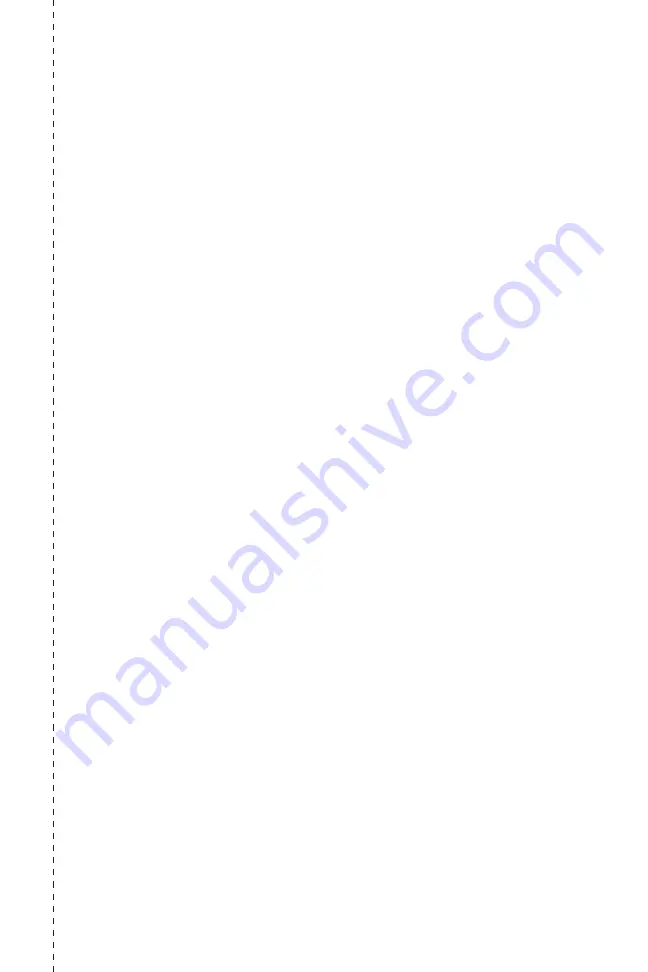
All of the employees that build your equipment strive to manufacturer the
very best
quality
product on
the market. We would appreciate your efforts in letting us know how we are doing.
We would like you to operate your machine for thirty (30) days and then fill out this questionnaire and mail it to us.
This will help us to keep producing a good product and improving our products through your recommendations.
DATE PURCHASE: ______________________
MODEL: ________________________________
SERIAL NUMBER: _______________________
DEALER NAME: ________________________
_______________________________________
Copyright 2-17 FORM #Q-111
TO BE RETURNED AFTER THIRTY (30)
DAYS OF OPERATION
Please return to: Customer Data Department
6750 Millbrook Road
Remus, MI 49340
Phone: (800) 952-0178 in USA
Phone: (989) 561-2270
Fax:
(989) 561-2273
Website: www.banditchippers.com
EQUIPMENT QUALITY REPORT
1. Did your machine perform to your expectations? _______________________________________
2. Was the machine delivered on schedule? _____________________________________________
3. Was the paint color and finish to your satisfaction? ______________________________________
4. Was machine equipment as ordered? ________________________________________________
5. Did all welds appear to be high quality? ______________________________________________
6. Was the overall machine to your liking? ______________________________________________
7. What problems have you experienced? ______________________________________________
8. Have any components regularly loosened that caused problems? __________________________
9. Does the hydraulic system seem to have adequate power for feeding wood into the machine? _____
10. Is the machine manufactured to accommodate service in an adequate manner? If not, please explain:
_______________________________________________________________________________
11. General comments and/or suggestions: ________________________________________________
_______________________________________________________________________________
_______________________________________________________________________________
12. Would you like to be contacted concerning more of our equipment? ________________________
YOUR COMPANY: ________________________________
NAME: __________________________________________
ADDRESS: ______________________________________
CITY: ___________________________________________
STATE & ZIP: _____________________________________
PHONE: ( ____ ) _________________________________
E-MAIL: _________________________________________