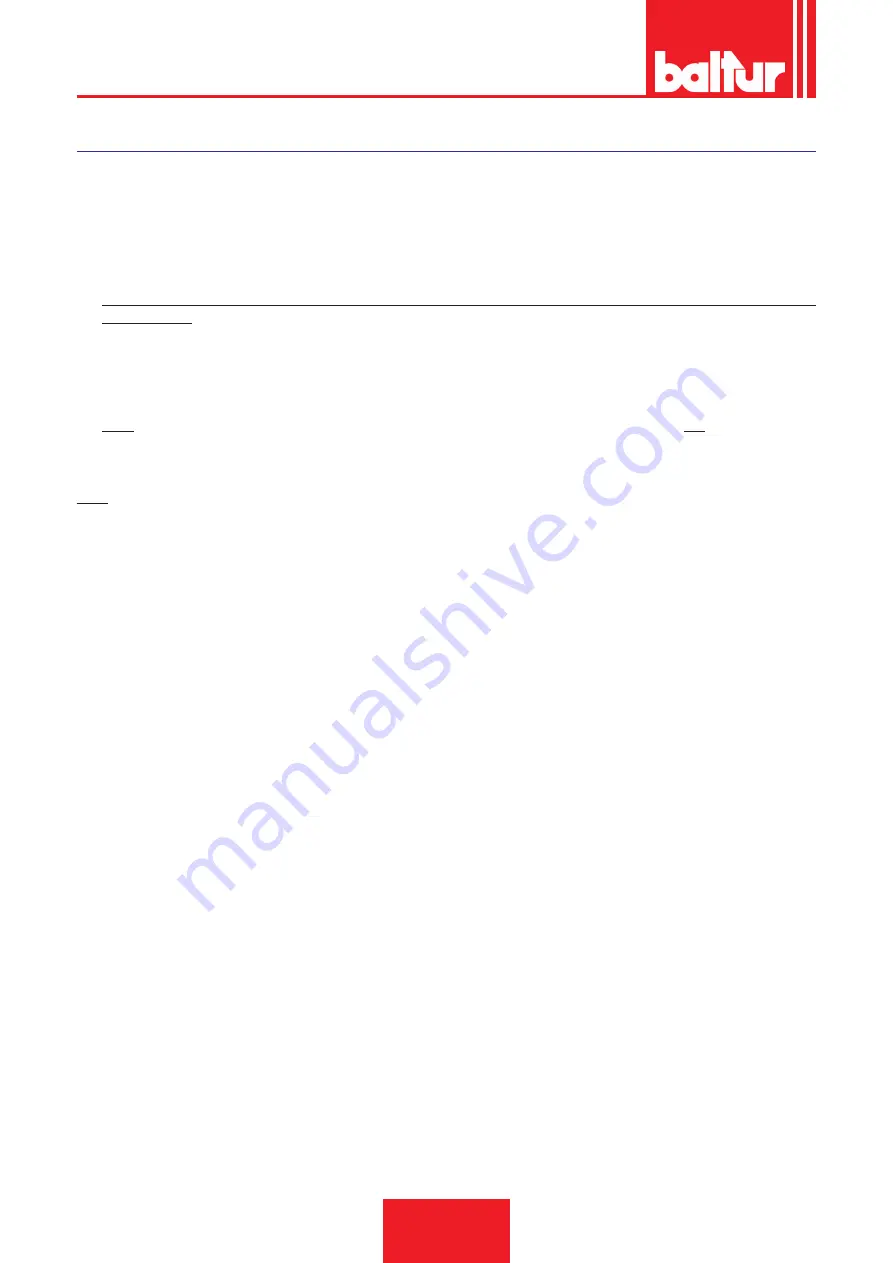
IGNITION AND ADJUSTMENT
Before igniting make sure that:
a) Connections with the fuel line, thermostats or pressure switches are carried out exactly as illustrated in the
control box wiring diagram.
b) There is fuel in the tank and water in the boiler.
c) That all the sluice valves on the fuel oil suction and return piping are open as is every other part through which
the fuel flows.
d) Combustion fumes discharge occurs freely (boiler flue gates and chimney open).
e)
Make sure the burner head penetrates the combustion chamber in accordance with the boiler manufacturer’s
specifications. To ensure this is so the burner is equipped with a boiler attachment flange which slides with
respect to the combustion head.
f) The burner nozzles are compatible with boiler output; if necessary, replace them.
The quantity of fuel being delivered must never be greater than the maximum boiler-requested quantities or
maximum admissible burner quantities. Bear in mind that the combustion head has been designed for use
with nozzles having a 45° spray angle.
Note
: To ensure good ignition and combustion with the first stage only, fuel delivery must
not
be notably lower
than the minimum flow-rate for the employed burner (see identification plate).
FOR IGNITION PROCEED AS FOLLOWS:
Note
: The burner is equipped with a manual switch to change from the 1
st
to the 2
nd
stage.
1) Switch on the 1
st
and 2
nd
stage switch to prevent ignition of the 2
nd
flame.
2) Slightly open the air gate to obtain the air-flow thought necessary for burner operation with the 1st stage
by acting on the cam which limits the servomotor stroke for the 1
st
stage (see BT 8653/1 or BT 8711/1).
Adjust the air adjustment device on the combustion head to an intermediate position (see, further on, “Air
regulation on the combustion head”).
3) Turn on the main switch and the ON/OFF burner switch.
This switches on all the fuel oil heating elements and simultaneously causes the yellow warning light on the
burner to come on.
4) The minimum thermostat comes on when the fuel contained in the preheater reaches the set temperature.
When the minimum thermostat switches off the control box (if the other boiler thermostats are off) is switched
on; the control box then switches on the devices making up the burner as per the pre-set program.
The unit ignites as illustrated in “Description of Operation”.
5) When the burner is operating with the 1
st
stage adjust, as described in point 2, the air quantity so that good
combustion is ensured. It is better to have a slightly poor 1
st
stage air-flow in order t ensure perfect ignition
even under the most demanding conditions.
6) After regulating the 1
st
stage air-flow stop the burner by cutting power at the main switch. Connect the terminals
of the 2
nd
stage thermostat terminal block together and position the1st-2nd stage switch to 2nd stage.
7) Act on the cam which limits the 2
nd
stage air gate servomotor stroke; adjust to the quantity thought necessary
for the fuel to be burnt (see BT 8653/1 or BT 8711/1).
8) Switch the unit back on; it will now pass automatically to the second stage according to the set program.
9) With the unit now operating with the 2
nd
stage, adjust (by operating on the cam described in point 7) the air-
flow to the quantity needed to ensure good combustion. Combustion checks should be carried out with special
instruments. If suitable instruments are unavailable observe the colour of the flame. We recommend that you
adjust to obtain a soft, light orange flame: avoid a red flame that gives off smoke or a white flame with excess
air. The air regulator must be in a position which gives a percentage of carbon dioxide (CO
2
) in the fumes that
varies from a minimum of 10% to a maximum of 13% with a smoke rating that does not exceed standard limits
(Bacharach scale). We recommend that you adjust to obtain a soft, light orange flame: avoid a red flame that
gives off smoke or a white flam with excess air (see also “Air adjustment on the combustion head”.
10) Adjustment of the preheater thermostats, minimum thermostat and regulation thermostat (max) is effected
by the manufacturer and set at values which may, however, be unacceptable in certain individual cases. It is
therefore necessary, during final testing, to check that these values do not cause problems (poor combustion,
smoke, formation of gas in the preheater, etc.). Where necessary, increase or decrease the settings; bear in
mind that the regulation thermostat must nevertheless be at a temperature approximately 15° higher than the
minimum thermostat setting. The minimum thermostat must close at the minimum temperature needed to ensure
that fuel arrives at the nozzle with viscosity below 2° E. This condition is indispensable for proper atomization.
(As a rough guide see the viscosity-temperature diagram regarding the employed oil type).
ENGLISH
20 / 38
0006080547_201610
Summary of Contents for BT 100 DSN 4T
Page 2: ......
Page 38: ... SOLO PER BT 180 250 300 ITALIANO 36 40 0006080537_201610 ...
Page 39: ...ITALIANO 37 40 0006080537_201610 ...
Page 40: ...ITALIANO 38 40 0006080537_201610 ...
Page 41: ...ITALIANO 39 40 0006080537_201610 ...
Page 76: ... ONLY FOR BT 180 250 300 ENGLISH 34 38 0006080547_201610 ...
Page 77: ...ENGLISH 35 38 0006080547_201610 ...
Page 78: ...ENGLISH 36 38 0006080547_201610 ...
Page 79: ...ENGLISH 37 38 0006080547_201610 ...
Page 116: ... SÓLO PARA BT 180 250 300 ESPAÑOL 36 40 0006080537_201610 ...
Page 117: ...ESPAÑOL 37 40 0006080537_201610 ...
Page 118: ...ESPAÑOL 38 40 0006080537_201610 ...
Page 119: ...ESPAÑOL 39 40 0006080537_201610 ...
Page 121: ......