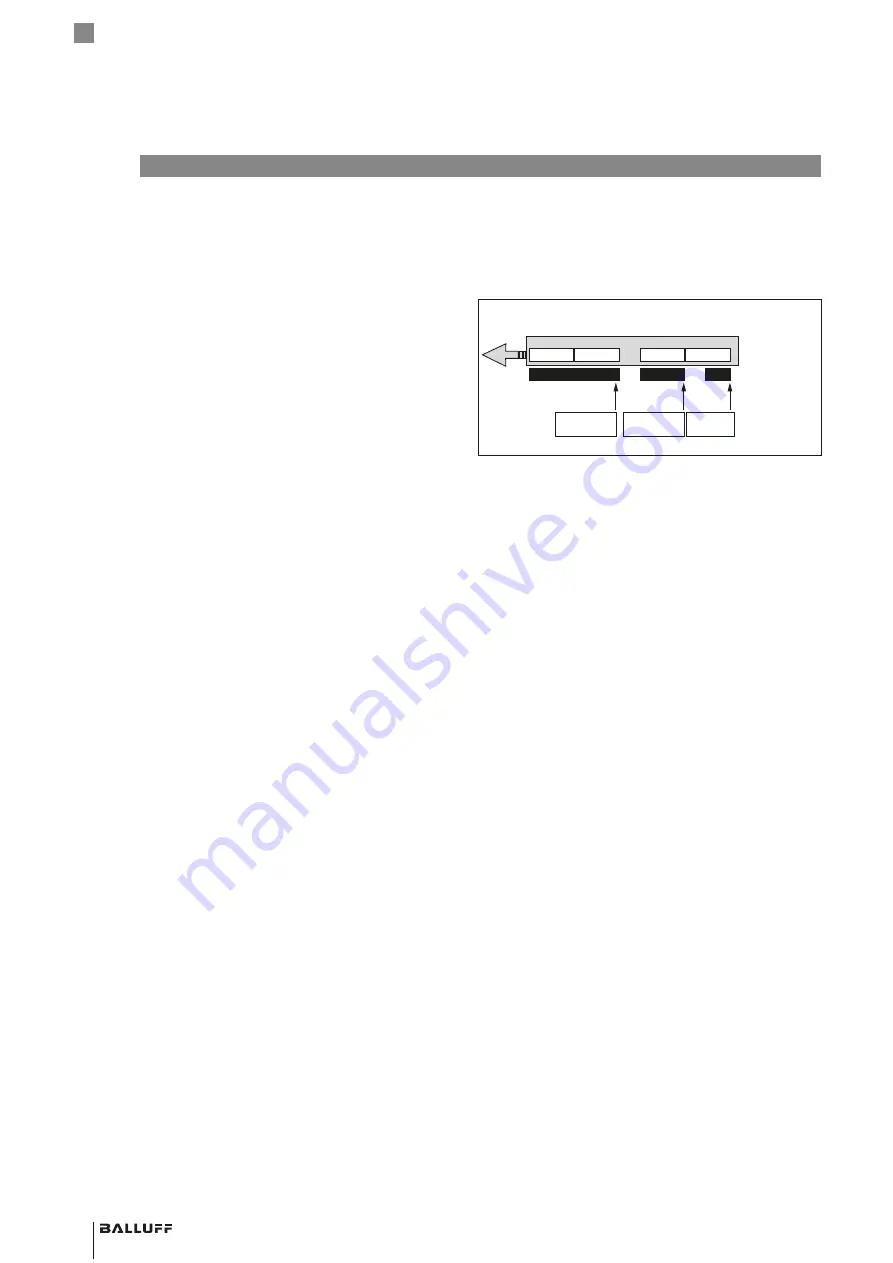
6
english
2.1
General
IO-Link integrates conventional and intelligent sensors and
actuators in automation systems and is intended as a
communication standard below classic field buses. Field-
bus-independent transfer uses communication systems
that are already available (field buses or Ethernet-based
systems).
IO-Link devices, such as sensors and actuators, are
connected to the controlling system using a point-to-point
connection via a gateway, the IO-Link master. The IO-Link
devices are connected using commercially available
unshielded standard sensor cables.
Communication is based on a standard UART protocol
with a 24-V pulse modulation in half-duplex operation. This
allows classic three-conductor physics.
2.2
Protocol
With IO-Link communication, permanently defined frames
are cyclically exchanged between the IO-Link master and
the IO-Link device. In this protocol, both process and on
demand data, such as parameters or diagnostic data, is
transferred. The size and the type of the frame and the
cycle time used result from the combination of master and
device features (see communication properties in section
2.3
Cycle Time
The cycle time used (master cycle time) results from the
minimum possible cycle time of the IO-Link device
(min cycle time, see section 3.2 on page 10) and the
minimum possible cycle time of the IO-Link master. When
selecting the IO-Link master, please note that the larger
value determines the cycle time used.
2.4
Communication parameters
In order to be able to establish a stable communication
connection between master and device, the master
requests some important communication parameters from
the device at the start of communication. Settings for
communication in
Preoperate
and
Operate
modes are
influenced by the parameters and the device is clearly
identified.
Communication parameters are described in chapter 4 on
2
IO-Link Basic Knowledge
2.5
Process Data Flow
The data transfer is based on the general profile
specification (IO-Link Common Profile 1.0, see Fig. 2-1 for
example).
Fig. 2-1:
Byte 0
7
0
39
30
Byte 1
...
7
0
31
24
Byte 3
7
0
15
8
Byte 4
7
0
7
0
n
Data type: UIntegerT
TypeLength: 8
Bit offset: 8
n+1
n+3
n+4
memory address in the PLC
n = baseaddress
Bit offset
PDinput data stream (device view)
Example PDinput data stream
PVinD 2
Data type: IntegerT
TypeLength: 16
Bit offset: 24
PVinD 3
“PDV2“
“PDV1“
“BDC1_2“
Data type: Bool
TypeLength: 2
Bit offset: 0
PVinD 1
Transmission
direction
(“to master”)
Byte stream
Bool
UInteger8
Integer16
Example of a PDinput data flow
The highest value byte (MSB, designated as
Byte 0
) is
transferred first and can be found in the PLC under the
lowest storage address. The lowest value byte (LSB) is
transferred last and has the highest byte number
Byte 4
).
For word-based data types (> 8 bit) this means that the
byte at the lowest address is the highest value byte, while
the highest address contains the lowest value byte.
In the IODD, the description of the data flow is realized
using the skew descriptors. This skew starts
at the right
with the lowest value byte.
Process data variables (in Fig. 2-1: PDV1, PDV2) are
aligned to the byte limits in most cases.
Binary information (BDC) is transferred in the lowest value
byte in most cases.
The process data flow is made up of various process data
objects, which are not only shown in the process data
flow, but are also used for the internal exchange of
information between functions. For example,
PdObjects
can be used to offset random binary information in the
or to display certain information at
the digital output. Therefore, a unique object ID is assigned
to this individual information, which can be used at
different places.
Process data objects are described in the function
chapters under
Process Data
.
BOS R254K-UUI-RH11-S4
Photoelectric Sensors
Summary of Contents for BOS R254K-UUI-RH11-S4
Page 1: ...deutsch Konfigurationsanleitung english Configuration Guide BOS R254K UUI RH11 S4...
Page 2: ...www balluff com...
Page 3: ...BOS R254K UUI RH11 S4 Konfigurationsanleitung deutsch...
Page 4: ...www balluff com...
Page 108: ......
Page 109: ...BOS R254K UUI RH11 S4 Configuration Guide english...
Page 110: ...www balluff com...