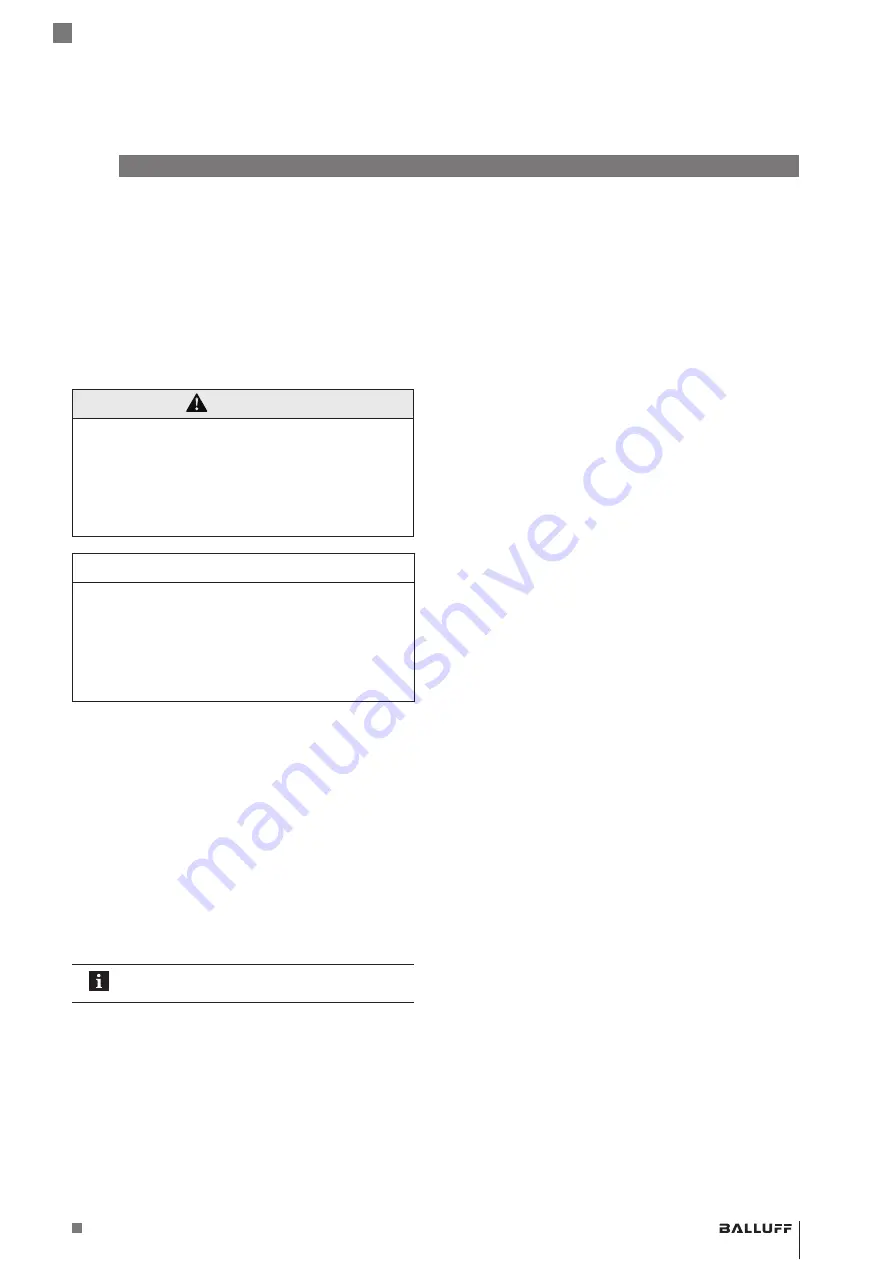
www.balluff.com
9
english
There are three available variants for installation:
– Attachment to a pneumatic cylinder using a C- or T-slot
(see section 4.1).
– Attachment to a round cylinder using hose clamps and
round cylinder holders (see section 4.2).
– Mount the BMP to a surface using mounting screws
and operate it with floating target (see section 4.3).
Important installation notes
CAUTION
Increased housing temperature
In the event of insufficient heat coupling due to the
mounting, the surface temperature of the BMP can
increase and cause burns when touched.
►
Correct the heat coupling of the installation.
►
Reduce the load.
NOTICE
Interference in function
Improper installation can compromise the function of the
BMP and result in increased wear.
►
The target must not contact the BMP.
►
Shield any magnetic fields that can influence the
measurement.
Position the BMP so that the measuring range can detect
the entire range of movement of the target.
The target must be polarized axially. The orientation (whe-
ther the cable end points in the direction of the North or
South Pole) does not matter.
The position detected by the BMP is in the middle of the
target.
Only the cylinder which has a permanent magnet installed
as the target is eligible when mounting to a pneumatic
cylinder.
A rotating cylinder head causes inaccuracy that is too
large!
For fastening screws and slot nuts, see
4
Installation and connection
BMP 01- EL1PP _ 1A- _ _ _ _ -00 -P _ _ /P _ _ -S4/P _ _ -S75
Magnetic Field Positioning System
Summary of Contents for BMP 01-EL1PP 1A Series
Page 2: ...www balluff com...