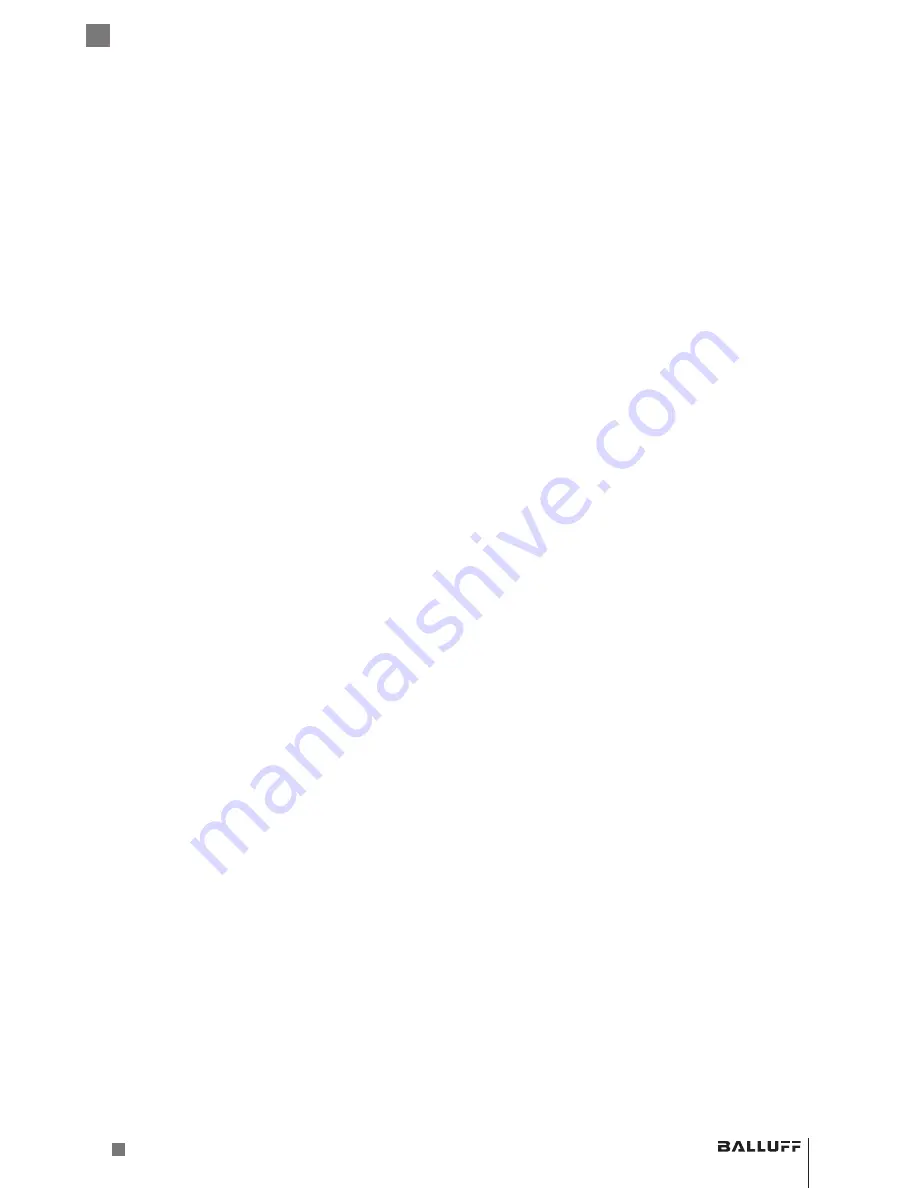
4.3 Measures against simple circumvention
The safety sensor responds to metallic objects, e.g. the frame of a
safety door. Other metallic objects which are not supposed to result
in release of the sensor must not cause an unintended release of the
safety sensor.
In addition, the sensor has the following switching behavior for
making simple circumvention of its safety function more difficult:
1.
Slow approach of a metallic object into the release zone causes
the outputs to switch without delay but the Signal LED does not
come on until approx. 3 sec. later (see Section 7.1 Operating
mode on page 29). This means in general the object is in the
close zone before the Signal LED comes on. The technical requi-
rements with respect to restarting the system must be observed.
2.
If the object remains in the close zone for more than approx.
2 sec., the outputs are completely locked and not released when
there is damping in the close zone. If the object remains in the
close zone longer than 5 sec., the adjustment mode is activated
(see Section 6.1 Calibration aid on page 24).
www.balluff.com
21
BES M/Q…-D12 Inductive Safety Sensors