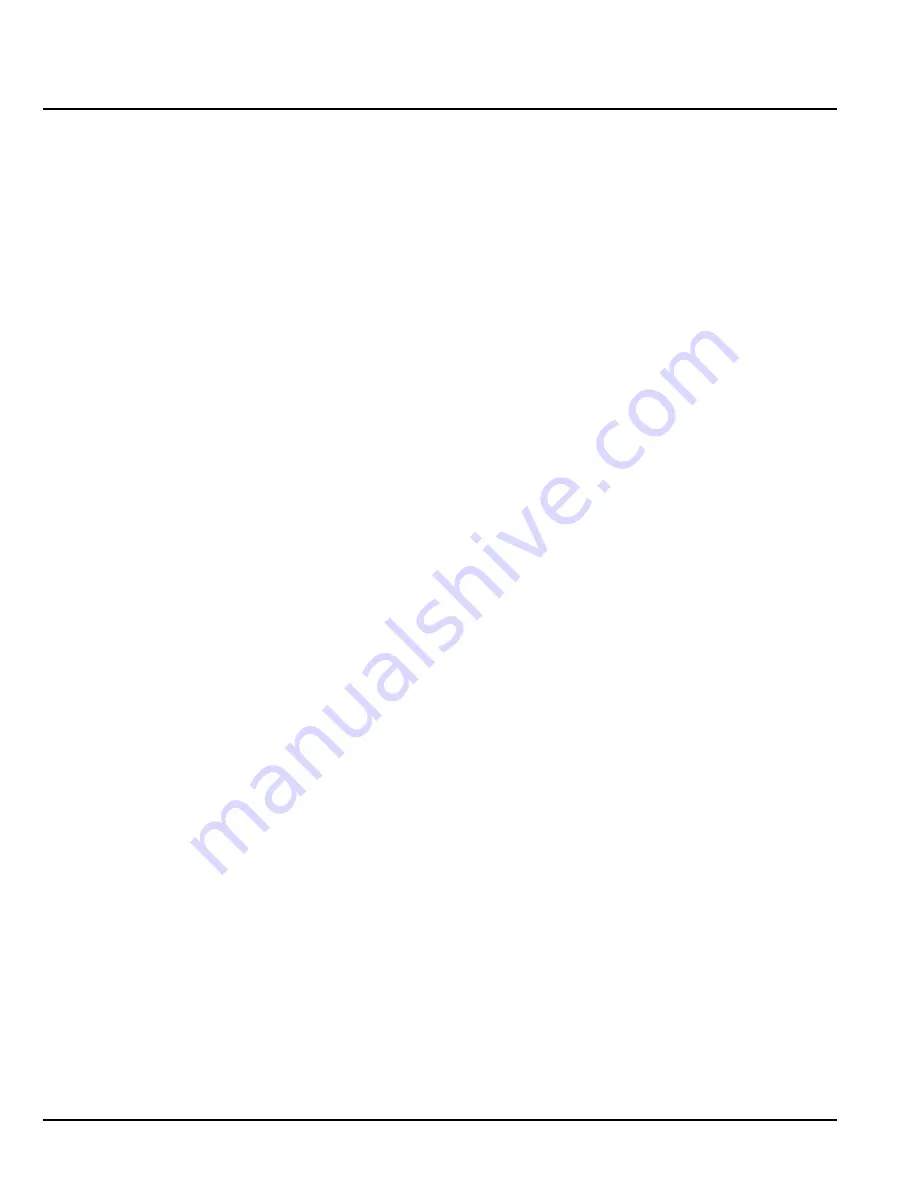
3-6
MN605
Troubleshooting
Armature Overheating
Excessive overloads will cause a noticeable odor of overheated varnish or charred insulation. The commutator
may eventually become blackened and pitted and the brushes burned. This overheating may be general and
uniform. To cure, remove the overload and rewind or replace armature if damaged beyond use.
An open-circuited armature coil will cause flashing at the commutator. Two adjacent bars will show severe
burning and a resulting overheated armature. Short-circuited coils or commutator bars may cause local heating
that could destroy the insulation at that spot. This may result in the burning of the armature coils, banding or
commutator bars.
Grounds in the armature circuit may be found by measuring the motor winding resistance. If the armature s
grounded, less than 1 meg ohm is measured. These tests should be done by experienced and qualified
personnel.
Field Coil Overheating
The blowers or external cooling systems should be left in operation if the main field windings remain fully
energized with the motor at standstill. Failure to do so may cause too much heat build-up which could cause
reduced insulation life.
When using field economy circuits to reduce voltage to the main fields during standstill, blowers do not need to
be operating. The most common failure with overheated field coils is a short in one or more of the shunt coils.
Shorted coils show less than half the line voltage for two pole motors. This is with the fields connected for high
voltage (in series). Shorted four pole motor coils will read less than 1/4 of the line voltage with the coils connected
for high voltage (in series).
A grounded coil may cause overheating. This defect may be tested as shown by the ground test for an armature.
With brushes lifted, measure the motor winding resistance. If the armature is grounded, less than 1 meg ohm is
measured.
An open field coil on a motor will cause the armature to have no torque. The motor may run at a very high speed
at no load. The commutator may be flashing. To locate an open coil, apply line voltage to the shunt coils (brushes
lifted). A voltmeter will show no reading across a good coil. It will show about the line voltage across the open
coil.
These tests should be done by experienced and qualified personnel. If you find any of the above defects, don’t
run the motor. First contact your local Baldor District Office or an Authorized Baldor Service Center for repairs.
Excessive Load
Excessive load may be found by checking the DC armature ampere input and comparing it with the rating on
the nameplate. An excessive load may prevent the motor from starting or accelerating to full load speed. It could
finally result in premature failure of the motor or control. Be sure to use an averaging type ammeter if the motor’s
power is coming from a rectifier or SCR control.
Jogging and Repeated Starts
Repeated starts or jogs of motors may reduce the life of the brushes and winding insulation. The heat produced
by excessive starting may be more than what can be dissipated by the motor under a constant full load
conditions. If you must frequently start or jog a motor, you should check the application with the local Baldor
District Office.
Heating
Duty cycle and maximum ambient temperature are shown on the nameplate of the motor. If there is any question
about safe operation, contact the local Baldor District Office.
Motor overheating may be caused by improper ventilation, excessive ambient temperature, dirty conditions or an
inoperable blower or dirty filter. Electrical causes may be due to excess current caused by an overload or over-
voltage to the fields.
Thermostat
Most stock Baldor DC motors 180 frame and above have a standard temperature-sensing thermostat mounted to
their interpole winding. This normally closed thermostat opens when the temperature limit is exceeded. Another
option available is a normally open thermostat that closes with temperature.
On blower cooled or separately ventilated motors, the protection capabilities of the thermostats are greatly
reduced at low speeds. This is because the interpoles have the same amount of heat transfer regardless of
speed. Armature heat transfer is less at low speed. There is less internal air turbulence at low speeds causing
higher temperatures at the armature.
The thermal time constant for interpoles can be as much as five times longer than the armature’s time constant.
Because of this, the thermostat cannot be relied upon to protect the armature during extreme overloads lasting a
short time.
The ripple of the rectified power supply and manufacturing tolerances of mounting the device affect the
thermostat’s accuracy.
For thermostat contact ratings, refer to Thermostats in Section 2 of this manual.
Summary of Contents for MN605
Page 23: ......