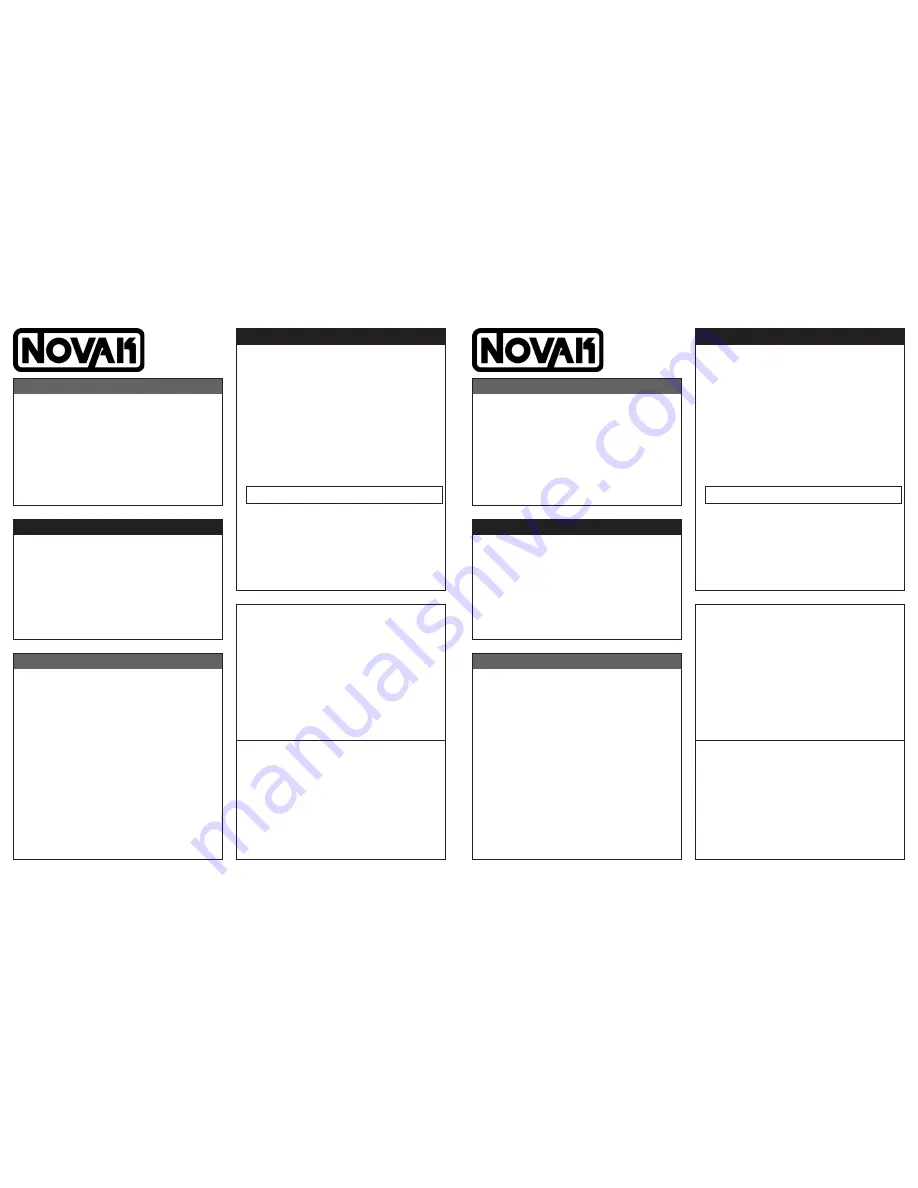
#55-3555-1 Rev.1
Printed 11-2007
PRECAUTIONS
• WATER & ELECTRONICS DON’T MIX
Never allow water, moisture, or
other foreign materials to get inside motor, or on PCBs.
• CHECK MOTOR SCREWS
Remember to check all motor screws
for loosening after a few runs of the motor.
• INSULATE WIRES
Always insulate exposed wiring with heat shrink
tubing to prevent short circuits.
• NO SOLVENTS
Do NOT expose the motor to any type of solvents.
• MOTOR CAPACITORS
Brush motors generate electrical noise. Keep
all 3 capacitors on the motor to help prevent radio interference.
• NO SCHOTTKY DIODES WITH REVERSIBLE ESCs
NEVER use Schottky
diodes on the motor with reversible ESCs--ESC damage will occur.
• SET GEAR MESH PROPERLY
Too tight of a gear mesh can result
in motor pinion shaft breakage--be sure to adjust mesh properly.
MOTOR MAINTENANCE
• CHECK MOTOR SCREWS
Check all motor screws for loosening at regular intervals, just like
other hardware on your vehicle.
• CHECK MOTOR BEARING & BRUSH WEAR
After extensive use, your motor’s bearings or commutation brushes
may need replacement. A small drop of light oil on the bearings
periodically can help extend bearing life
--however, too much oil will
attract dirt and will cause problems, so apply sparingly & wipe clean
.
• CLEAN INSIDE MOTOR
Periodically remove the end bell of your motor, remove the rotor,
and blow out the inside of the motor with compressed air.
Be sure
not to lose any small shim washers that may be on the shaft ends &
keep them in the correct location.
INSTALLATION INSTRUCTIONS
1. CHECK MOTOR SCREW LENGTH & INSTALL MOTOR
• Insert the M3 motor mounting screws that came with your
vehicle through the motor mounting plate.
You need no more
than 1/8” of screw extending past the vehicle’s mounting plate
(2-4mm)--
Too little can strip the motor’s threads, too much may
cause internal motor damage & will void warranty.
• Attach motor to vehicle’s motor mount using one of the sets of
threaded mounting holes--
select a mounting position that keeps the
wire tabs clear of conductive surfaces like aluminum or graphite
.
2. INSTALL PINION GEAR
Install pinion on motor and align pinion and spur gears. Tighten
pinion’s set screw on the flat of motor shaft.
3. ADJUST MOTOR FOR PROPER GEAR MESH
• Adjust the motor position for proper amount of free play.
You
NEED
a small amount of play between the pinion gear and
the spur gear
(about the thickness of piece of paper)
--
check the
free play at several positions around the spur gear to ensure
a proper mesh
(just in case the gears are out of round)
.
MAKE SURE THE PINION/SPUR GEAR MESH IS NOT TOO TIGHT!
If gear mesh is too tight, motor shaft breakage can occur.
• Tighten motor mounting screws--Avoid using excessive force
that could break screws or strip the threaded holes in motor.
4. SOLDER MOTOR POWER WIRES
• Determine the best routing in vehicle for power wires.
Prepare
ends of motor power wires
by stripping 1/8-1/4” of insulation
from end of wire. Tin wire ends with solder.
•
Lay tinned end of the wire flat on the solder tab and solder
wires to proper tabs of the motor
. Apply heat with soldering
iron to the power wire and solder tab--begin adding solder to
tip of iron and to wire--
Add just enough solder to form a clean
& continuous joint from the solder tab up onto the wire.
5460 3 Amp Universal BEC--
6VDC/3A output Battery Eliminator Circuit for 6.3-8.4VDC input.
5463 3A High-Voltage Universal BEC--
6VDC/3A output B.E.C. for up to 26.4VDC input.
5465 5 Amp Universal BEC--
6VDC/5A output Battery Eliminator Circuit for 6.3-8.4VDC input.
5470 Smart-Stop 2-cell Li-Po Cut-Off Module--
Safe 2S Li-Po operation with 6.25V cut-off.
5471 Smart-Stop 4-cell Li-Po Cut-Off Module--
Safe 4S Li-Po operation with 12.5V cut-off.
5472 Smart-Stop 3-cell Li-Po Cut-Off Module--
Safe 3S Li-Po operation with 9.375V cut-off.
5485 4-Cell Transponder Voltage Booster--
Boosts voltage to transponder--No missed laps.
5500 14GA Super-Flex Wire--Black & Red
--3 ft each color, silicone.
5505 14GA Super-Flex Wire--Blue & Red
--3 ft each color, silicone.
5510 16GA Super-Flex Wire--Black & Red
--3 ft each color, silicone.
5515 16GA Super-Flex Wire--Blue & Red
--3 ft each color, silicone.
5530 12GA Super-Flex Wire--Black & Red
--3 ft each color, silicone.
5535 12GA Super-Flex Wire--Blue & Red
--3 ft each color, silicone.
5620 Motor Capacitors--25pcs 0.1µF(50V)
--Non-polarized ceramic capacitors.
5626 Glitch Buster Capacitor
--Stores battery power for receiver to eliminate radio cut-out.
5636 Racing Schottky Motor Module
--36A Schottky module for forward-only ESCs.
5647 Black Cooling Fan--25x25x10mm
--All purpose cooling fan with 2-pin JST connector.
5648 Clear Cooling Fan--30x30x6mm
--GTB replacement fan with 2-pin JST connector.
5810 Gold Battery Cross Bars--7pcs
--Gold plated oxygen-free copper battery bars.
5820 Silver Battery Cross Bars--7pcs
--Oxygen-free copper battery bars, plated for easy soldering.
5830 Lead-Free 3% Silver Racing Solder--10ft
--Low-resistance, high-conductivity solder.
5840 Double-Sided Mounting Tape--10pcs
--1”x1” high-performance clear mounting tape.
ACCESSORIES
#55-3555-1 Rev.1
Printed 11-2007
PRECAUTIONS
• WATER & ELECTRONICS DON’T MIX
Never allow water, moisture, or
other foreign materials to get inside motor, or on PCBs.
• CHECK MOTOR SCREWS
Remember to check all motor screws
for loosening after a few runs of the motor.
• INSULATE WIRES
Always insulate exposed wiring with heat shrink
tubing to prevent short circuits.
• NO SOLVENTS
Do NOT expose the motor to any type of solvents.
• MOTOR CAPACITORS
Brush motors generate electrical noise. Keep
all 3 capacitors on the motor to help prevent radio interference.
• NO SCHOTTKY DIODES WITH REVERSIBLE ESCs
NEVER use Schottky
diodes on the motor with reversible ESCs--ESC damage will occur.
• SET GEAR MESH PROPERLY
Too tight of a gear mesh can result
in motor pinion shaft breakage--be sure to adjust mesh properly.
MOTOR MAINTENANCE
• CHECK MOTOR SCREWS
Check all motor screws for loosening at regular intervals, just like
other hardware on your vehicle.
• CHECK MOTOR BEARING & BRUSH WEAR
After extensive use, your motor’s bearings or commutation brushes
may need replacement. A small drop of light oil on the bearings
periodically can help extend bearing life
--however, too much oil will
attract dirt and will cause problems, so apply sparingly & wipe clean
.
• CLEAN INSIDE MOTOR
Periodically remove the end bell of your motor, remove the rotor,
and blow out the inside of the motor with compressed air.
Be sure
not to lose any small shim washers that may be on the shaft ends &
keep them in the correct location.
INSTALLATION INSTRUCTIONS
1. CHECK MOTOR SCREW LENGTH & INSTALL MOTOR
• Insert the M3 motor mounting screws that came with your
vehicle through the motor mounting plate.
You need no more
than 1/8” of screw extending past the vehicle’s mounting plate
(2-4mm)--
Too little can strip the motor’s threads, too much may
cause internal motor damage & will void warranty.
• Attach motor to vehicle’s motor mount using one of the sets of
threaded mounting holes--
select a mounting position that keeps the
wire tabs clear of conductive surfaces like aluminum or graphite
.
2. INSTALL PINION GEAR
Install pinion on motor and align pinion and spur gears. Tighten
pinion’s set screw on the flat of motor shaft.
3. ADJUST MOTOR FOR PROPER GEAR MESH
• Adjust the motor position for proper amount of free play.
You
NEED
a small amount of play between the pinion gear and
the spur gear
(about the thickness of piece of paper)
--
check the
free play at several positions around the spur gear to ensure
a proper mesh
(just in case the gears are out of round)
.
MAKE SURE THE PINION/SPUR GEAR MESH IS NOT TOO TIGHT!
If gear mesh is too tight, motor shaft breakage can occur.
• Tighten motor mounting screws--Avoid using excessive force
that could break screws or strip the threaded holes in motor.
4. SOLDER MOTOR POWER WIRES
• Determine the best routing in vehicle for power wires.
Prepare
ends of motor power wires
by stripping 1/8-1/4” of insulation
from end of wire. Tin wire ends with solder.
•
Lay tinned end of the wire flat on the solder tab and solder
wires to proper tabs of the motor
. Apply heat with soldering
iron to the power wire and solder tab--begin adding solder to
tip of iron and to wire--
Add just enough solder to form a clean
& continuous joint from the solder tab up onto the wire.
PRODUCT WARRANTY
Novak products are guaranteed to be free from defects in materials or work-
manship for a period of 120 days from the original date of purchase
(verified
by dated, itemized sales receipt)
. Warranty does not cover incorrect installation,
components worn by use, cross-connection of battery/motor power wires,
overheating solder tabs, damage resulting from overload, wear or damage
from improper gear mesh, damage from disassembling motor or incorrect
re-assembly of motor, tampering with motor, allowing water, moisture, or any
other foreign material to enter motor, allowing exposed wiring or solder tabs
to short-circuit, or any damage caused by a crash, flooding, or act of God. In
no case shall our liability exceed the product’s original cost. We reserve the
right to modify warranty provisions without notice.
Because Novak Electronics, Inc. has no control over the connection & use of
motor or other related electronics, no liability may be assumed nor will be ac-
cepted for damage resulting from the use of this product. Every motor is tested
before leaving our facility and is, therefore, considered operational.
By the act of connecting motor to speed control or operating motor, the user ac-
cepts all resulting liability.
Novak Electronics, Inc.
17032 Armstrong Avenue
Irvine, CA 92614
Monday-Friday: 8am-5pm (PST)
(949) 833-8873 • FAX (949) 833-1631
e-mail:
web:
www.teamnovak.com
©2007 Novak Electronics, Inc. Irvine, CA, U.S.A. • All Rights Reserved
No part of these instructions may be reproduced without the
written permission of Novak Electronics, Inc. Motor made in Japan
and tested at the Novak facility in Irvine, CA.
5460 3 Amp Universal BEC--
6VDC/3A output Battery Eliminator Circuit for 6.3-8.4VDC input.
5463 3A High-Voltage Universal BEC--
6VDC/3A output B.E.C. for up to 26.4VDC input.
5465 5 Amp Universal BEC--
6VDC/5A output Battery Eliminator Circuit for 6.3-8.4VDC input.
5470 Smart-Stop 2-cell Li-Po Cut-Off Module--
Safe 2S Li-Po operation with 6.25V cut-off.
5471 Smart-Stop 4-cell Li-Po Cut-Off Module--
Safe 4S Li-Po operation with 12.5V cut-off.
5472 Smart-Stop 3-cell Li-Po Cut-Off Module--
Safe 3S Li-Po operation with 9.375V cut-off.
5485 4-Cell Transponder Voltage Booster--
Boosts voltage to transponder--No missed laps.
5500 14GA Super-Flex Wire--Black & Red
--3 ft each color, silicone.
5505 14GA Super-Flex Wire--Blue & Red
--3 ft each color, silicone.
5510 16GA Super-Flex Wire--Black & Red
--3 ft each color, silicone.
5515 16GA Super-Flex Wire--Blue & Red
--3 ft each color, silicone.
5530 12GA Super-Flex Wire--Black & Red
--3 ft each color, silicone.
5535 12GA Super-Flex Wire--Blue & Red
--3 ft each color, silicone.
5620 Motor Capacitors--25pcs 0.1µF(50V)
--Non-polarized ceramic capacitors.
5626 Glitch Buster Capacitor
--Stores battery power for receiver to eliminate radio cut-out.
5636 Racing Schottky Motor Module
--36A Schottky module for forward-only ESCs.
5647 Black Cooling Fan--25x25x10mm
--All purpose cooling fan with 2-pin JST connector.
5648 Clear Cooling Fan--30x30x6mm
--GTB replacement fan with 2-pin JST connector.
5810 Gold Battery Cross Bars--7pcs
--Gold plated oxygen-free copper battery bars.
5820 Silver Battery Cross Bars--7pcs
--Oxygen-free copper battery bars, plated for easy soldering.
5830 Lead-Free 3% Silver Racing Solder--10ft
--Low-resistance, high-conductivity solder.
5840 Double-Sided Mounting Tape--10pcs
--1”x1” high-performance clear mounting tape.
ACCESSORIES
PRODUCT WARRANTY
Novak products are guaranteed to be free from defects in materials or work-
manship for a period of 120 days from the original date of purchase
(verified
by dated, itemized sales receipt)
. Warranty does not cover incorrect installation,
components worn by use, cross-connection of battery/motor power wires,
overheating solder tabs, damage resulting from overload, wear or damage
from improper gear mesh, damage from disassembling motor or incorrect
re-assembly of motor, tampering with motor, allowing water, moisture, or any
other foreign material to enter motor, allowing exposed wiring or solder tabs
to short-circuit, or any damage caused by a crash, flooding, or act of God. In
no case shall our liability exceed the product’s original cost. We reserve the
right to modify warranty provisions without notice.
Because Novak Electronics, Inc. has no control over the connection & use of
motor or other related electronics, no liability may be assumed nor will be ac-
cepted for damage resulting from the use of this product. Every motor is tested
before leaving our facility and is, therefore, considered operational.
By the act of connecting motor to speed control or operating motor, the user ac-
cepts all resulting liability.
Novak Electronics, Inc.
17032 Armstrong Avenue
Irvine, CA 92614
Monday-Friday: 8am-5pm (PST)
(949) 833-8873 • FAX (949) 833-1631
e-mail:
web:
www.teamnovak.com
©2007 Novak Electronics, Inc. Irvine, CA, U.S.A. • All Rights Reserved
No part of these instructions may be reproduced without the
written permission of Novak Electronics, Inc. Motor made in Japan
and tested at the Novak facility in Irvine, CA.