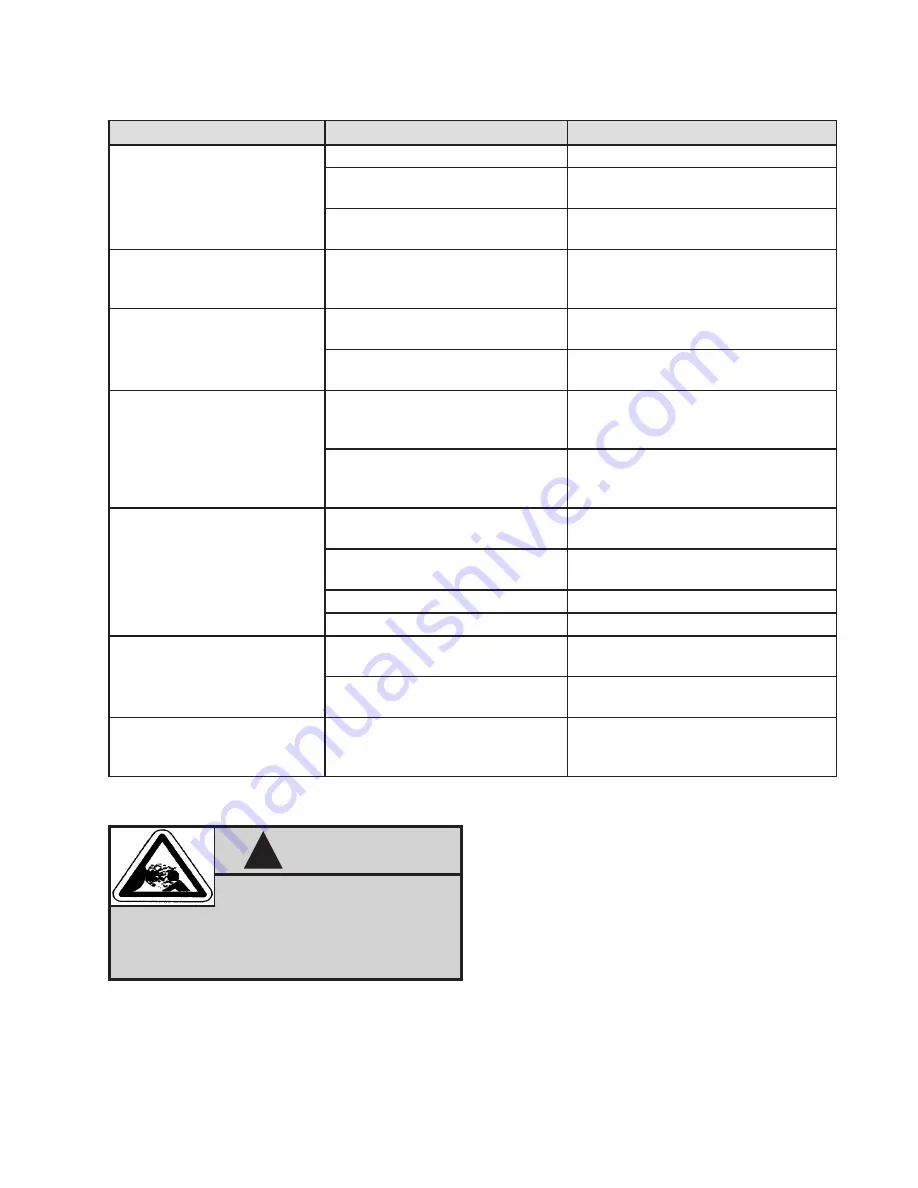
1. Insert the pump in a vice in a horizontal posi-
tion, grasp it by the suction tube.
2.
Unscrew the intake filter tube (42) from the
intake filter head (39) (fig. 1).
3. Unscrew the air motor body from the suction
tube using a threaded rod (fig. 2), and pull it out
until it stops. The union nut should be visible.
4. Introduce an open end wrench in the milling
of the lower part of the air piston and unscrew
the nut (41) and remove the washer (40) (fig. 3).
5. Remove the pin (25) situated in the upper
part of the union nut (fig. 4) and unscrew the air
motor body from the suction tube assembly.
7
TROUBLESHOOTING
Symptom
Possible Cause
Solution
The pump is not working or
there is no grease delivery.
Not enough air supply pressure.
Increase the air supply pressure.
An outlet line component is
clogged or closed.
Clean or open the outlet circuit.
There are air pockets in the
grease inlet area.
Compact the grease.
The pump begins to operate
very fast.
The drum is empty or the grease
level is beneath the suction tube
inlet.
Replace the drum or lower the suction
tube until the inlet reaches the grease
level.
The pump keeps on operating
although the grease outlet is
closed.
There is a grease leakage in some
point of the outlet circuit.
Verify and tighten or repair.
Impurities in the upper valve or in
the foot valve.
Remove and clean. Replace in case of
damage.
Grease leakage through the
air outlet muffler.
Grease has by-passed to the air
motor caused by worn or dam-
aged seals (22, 23) or O-ring (21).
Replace the worn or damaged parts.
The suction tube is not tightened
enough to the motor body.
Tighten the threaded union. Verify that
the O-ring (21) is in its correct posi-
tion.
Air leakage through the air
outlet muffler.
The sliding valve (12) does not
close correctly.
Remove and clean. Replace in case of
damage.
The valve support (13) or the
spring (19) are damaged.
Replace the items.
The air piston (3) is damaged.
Replace it.
The O-ring (5) is damaged.
Replace the Gland housing assembly.
Reduction in grease delivery.
There are air pockets in the
grease inlet area.
Compact the grease.
Impurities in the upper valve or in
the foot valve.
Remove and clean. Replace in case of
damage.
Reduction in grease pressure. The high pressure cylinder (33)
or the high pressure piston (29)
scratched.
Replace the items.
MAINTENANCE
WARNING
!
Before starting any kind of
maintenance or repair, Follow the pressure
relief procedure on page 2 of this service
bulletin.
Foot valve kit