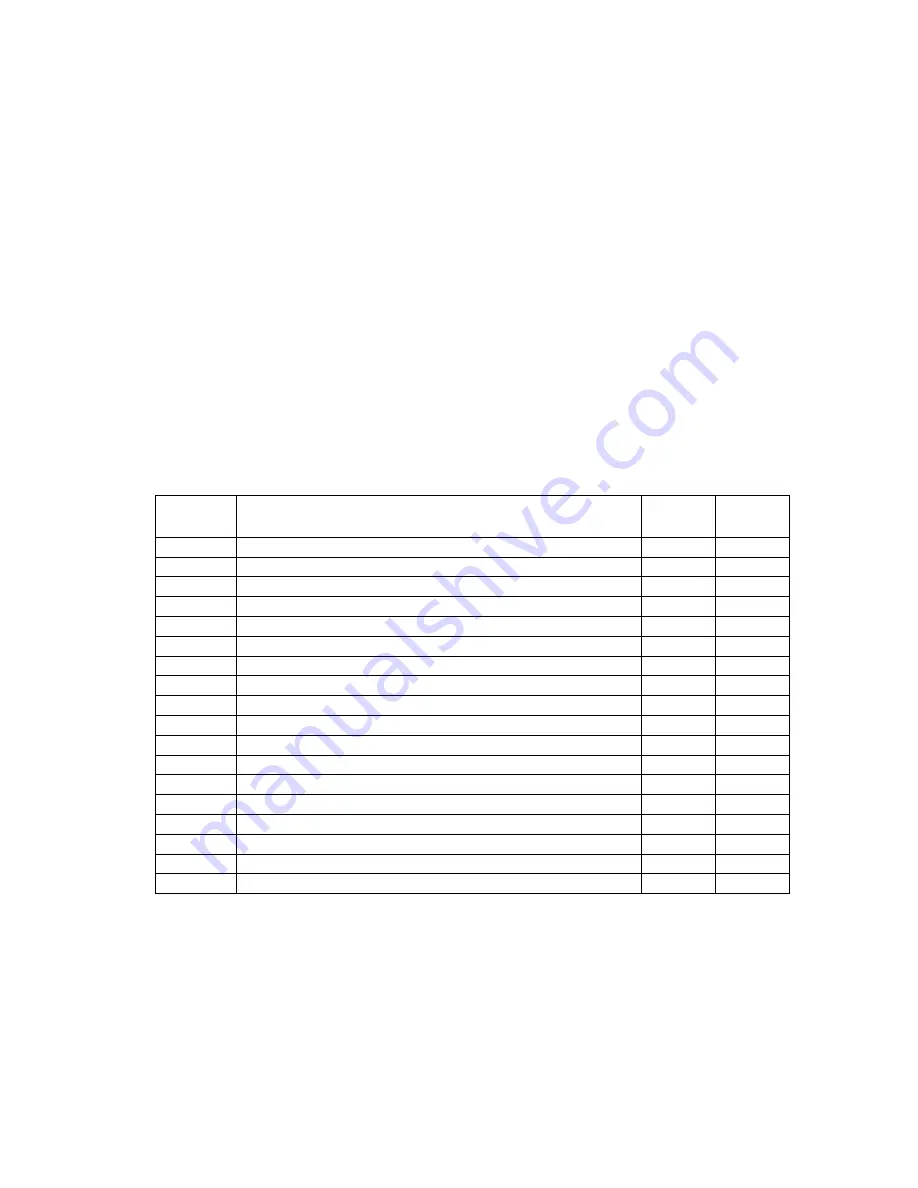
Document: 333D012G
5-18-2007
- 51 -
Installation of Exhaust Transition Systems for SterilGARD
®
III Cabinets
Tools required:
5/16
-
Hex wrench and nut driver
11/32 - Hex wrench and nut driver
3/8 - Hex wrench and nut driver
7/16 - Hex wrench and nut driver
11/32 - Combination wrench
Unpacking the Transition:
1)
Remove contents from the shipping packaging and examine for damage. (
Be careful not to damage
the gasket on the bottom flange of the exhaust transition
)
2)
Check the quantity of the components to the following packing lists and illustrations:
Item #
Description
Qty
SG403A
Qty
SG 603A
1
Exhaust transition
1
1
2
Exhaust filter access cover (closed face)
1
1
3
¼”-20 x ¾” Washer head bolt
4
6
4
¼” Seal washer
6
8
5*
¼”-20 x 1” Hex head bolt
4
4
6*
¼” Flat washer
6
6
7*
¼” Lock washer
6
6
8*
¼”-20 Double ended transition mounting bolt
2
2
9*
¼”- 20 Hex nut
2
2
10*
Exhaust transition mounting clip
2
2
11*
Air tight damper assembly (ATD)
1
1
12*
Short exhaust collar (Optional)
1
1
13*
#8-32 Cap nut
8
8
14*
#8 Flat washer
8
8
15*
#8 Lock washer
8
8
16
Exhaust transition gasket, ¼” x ½”
8.3 ft
10.3 ft
17
Access cover gasket, ¼” x ½”
6.2 ft
8.2 ft
18
Exhaust collar gasket, 1/8”
1
1
Packing List for Hard Exhaust Connection (HEC)
* = Items shipped loose in the packaging.
Summary of Contents for SG403A
Page 35: ...Document 333D012G 5 18 2007 34 Appendix ...
Page 38: ...Document 333D012G 5 18 2007 37 Dimensional Drawing Standard Configuration SG403A ...
Page 39: ...Document 333D012G 5 18 2007 38 Dimensional Drawing Standard Configuration SG603A ...
Page 41: ...Document 333D012G 5 18 2007 40 Interior View Exterior View Cable port plug not shown ...
Page 42: ...Document 333D012G 5 18 2007 41 Ladder Schematic SG403A ...
Page 43: ...Document 333D012G 5 18 2007 42 Ladder Schematic SG603A ...