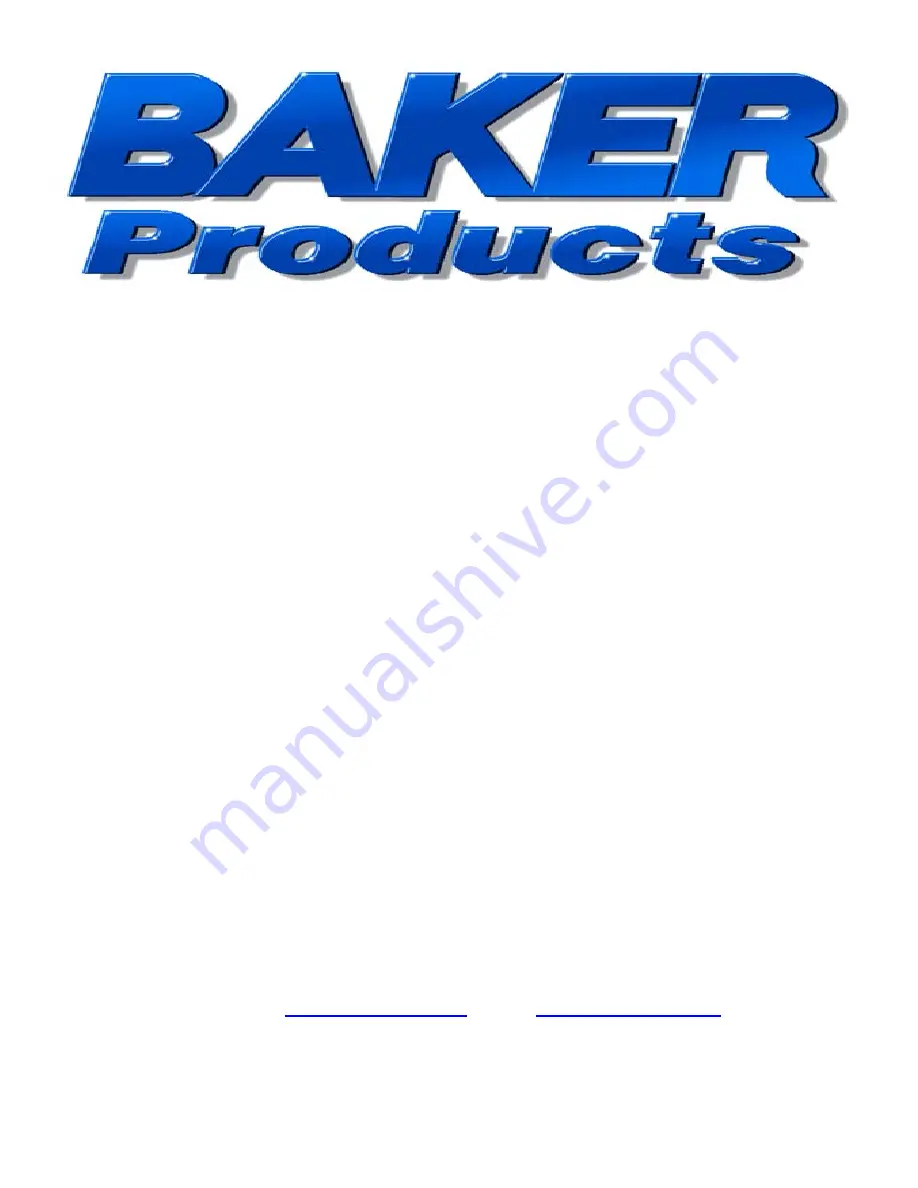
66
B
B
l
l
u
u
e
e
S
S
t
t
r
r
e
e
a
a
k
k
M
M
o
o
d
d
e
e
l
l
3
3
6
6
4
4
0
0
E
E
P
P
o
o
r
r
t
t
a
a
b
b
l
l
e
e
o
o
r
r
S
S
t
t
a
a
t
t
i
i
o
o
n
n
a
a
r
r
y
y
B
B
a
a
n
n
d
d
S
S
a
a
w
w
m
m
i
i
l
l
l
l
U
U
s
s
e
e
r
r
M
M
a
a
n
n
u
u
a
a
l
l
Ellington Industrial Supply, Inc.
P. O. Box 128
Ellington, Missouri 63638 USA
Web site:
www.baker-online.com
E-mail:
Phone: (573) 663 – 7711 Fax: (573) 663 – 2787
Equipment Photo
T
T
M
M