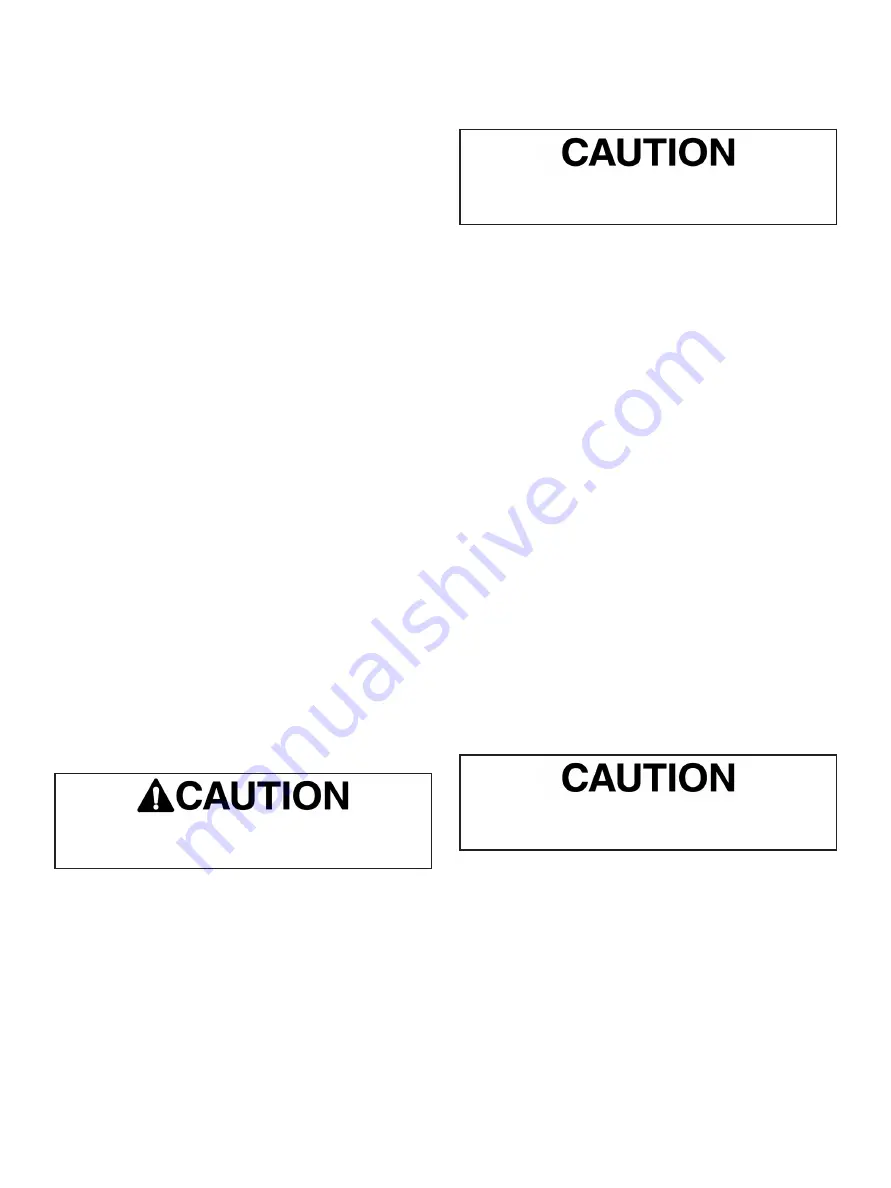
3 | Baker Hughes
Copyright 2020 Baker Hughes Company. All rights reserved.
4. Installation
Before installing, blow out line thoroughly to remove all foreign
matter which might foul the valve. Place the regulator in a
horizontal run of pipe so that the controlled fluid will flow through
the valve in the direction indicated by the arrow on the valve
body or the words IN and OUT marked on the connections. On
steam service, the valve should be installed with the diaphragm
actuator down so that the diaphragm will be protected by a water
seal. If installed otherwise, an adequate water seal must be
incorporated.
Pipe the controlled pressure from a convenient point in the line
6-10 feet from the regulator (or in the discharge line
6-10 feet from the pump on pump pressure applications) to the
½’’ NPT connection in the diaphragm case. Install a gauge and a
needle valve in the control line. The valve permits shutting off the
control line and also serves as an adjustable choke to prevent
cycling of the regulator, which may result from the pulsation of a
pump in the system.
A three-valve bypass around the regulator permits removing the
regulator from the line without shutting down the system.
5. Adjustment
When pressure setting is specified, the regulator is set
accordingly at the factory; otherwise it is set at the minimum of
the range shown on the serial plate.
Open stop valve on the outlet side of the regulator and partially
open stop valve on the inlet side, allowing pressure in the system
to build up slowly. Then open control line valve and check setting
by means of the gauge. To increase pressure setting, turn
adjusting screw clockwise to compress the spring. To decrease
the setting, turn adjusting screw counterclockwise to relieve
spring compression. Fully open stop valve on the inlet side of
the regulator.
6. Body Disassembly
Access to the internal components of the body should be
accomplished with the actuator removed. To remove the actuator
from the body, refer to the Instruction Manual 31593 for 10900
Series Actuators.
Prior to performing maintenance on the valve, isolate
the valve and vent the process pressure.
6.1 525 (Reducing Service)
After removing the actuator, disassemble the body using the
following procedure:
A. If there is a leak detector connection on the lateral NPT port
of the bonnet, disconnect this piping as well.
B. Remove body stud nuts (21).
C. Remove bonnet (10), and plug stem (5) and plug (4) sub-
assembly together as one unit.
Note: Spiral wound body gaskets (22) are standard in
the 500 Series design and it is imperative that a new
gasket be installed each time the valve is disassembled.
D. Remove packing flange stud nuts (15), packing flange (13)
and packing follower (12).
E. Remove plug (4) and plug stem (5) sub-assembly from the
bonnet (10).
Care must be taken to avoid damage to the plug and
plug guide.
F. Remove old packing (16) [and optional lantern ring (17) if
a leak detection connection has been installed]. Refer to
Figure 2.
G. Remove blind head (9) [including lower bushing(23)]
Note: Spiral wound body gaskets (22) are standard in
the 500 Series design and it is imperative that a new
gasket be installed each time the valve is disassembled.
H. Bonnet (10), plug (4), bushings (23) and seat rings (2 &
3) may now be inspected for wear and service damage.
After determining the maintenance required, proceed to the
appropriate Section of this instruction manual.
6.2 526 (Back Pressure Service)
After removing the actuator, disassemble the body using the
following procedure:
A. If there is a leak detection connection on the lateral NPT port
of the bonnet, disconnect this piping as well.
B. Remove body stud nuts (19).
C. Remove packing flange stud nuts (15), packing flange (13)
and packing follower (12)
D. Remove bonnet (10)
E. Remove blind head (9) [including lower bushing(23)]
Note: Spiral wound body gaskets (22) are standard in
the 500 Series design and it is imperative that a new
gasket be installed each time the valve is disassembled
F. Plug stem (5) and plug (4) sub-assembly can now be
removed together as one unit from the bottom of the valve.
Care must be taken to avoid damage to the plug and
upper bushing (23).
G. Remove old packing (16) [and optional lantern ring (17) if
a leak detection connection has been installed]. Refer to
Figure 2.
H. All components may now be inspected for wear and service
damage. After determining the maintenance required,
proceed to the appropriate Section of this instruction manual.