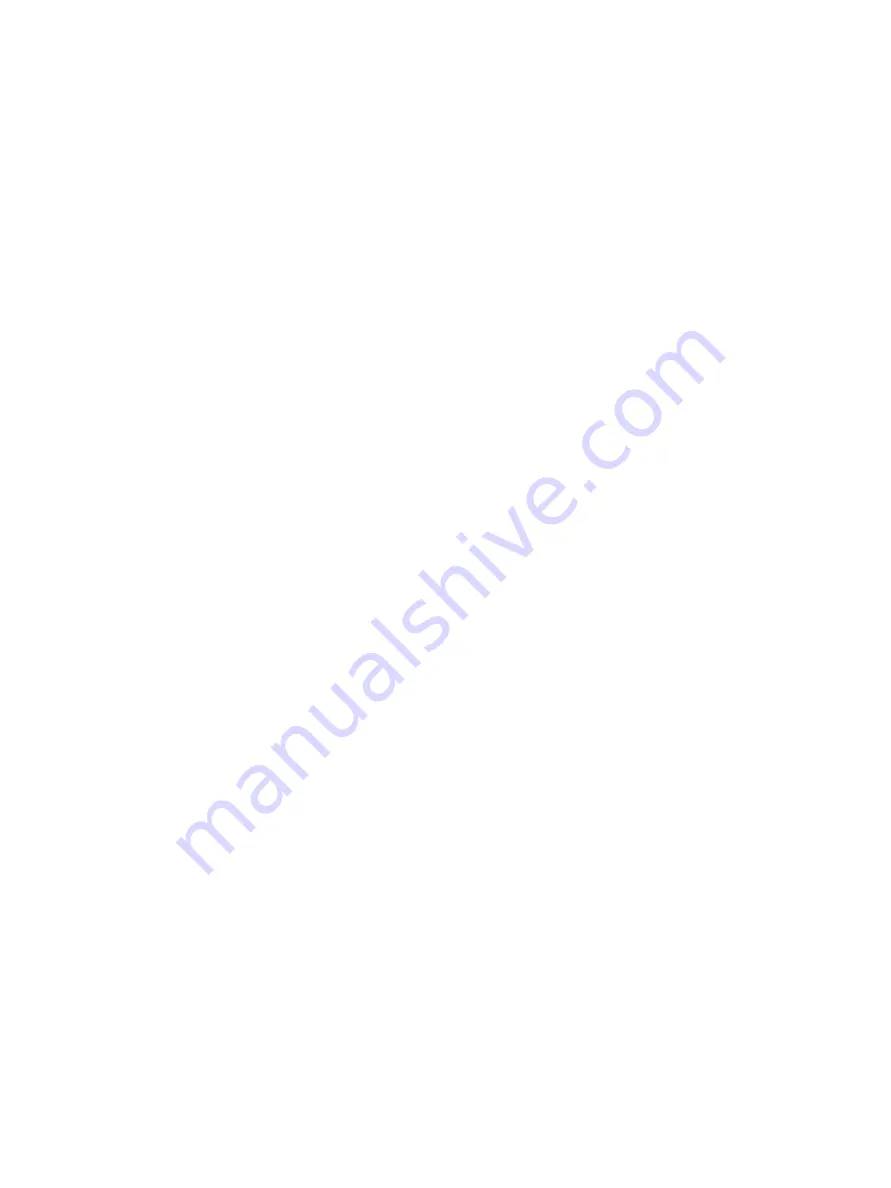
8 |
Baker Hughes
© 2020 Baker Hughes Company. All rights reserved.
V. Valve Terminology (Cont.)
•
Overpressure
Overpressure is a pressure increase over the set
pressure of a safety valve, usually expressed as a
percentage of set pressure.
•
Popping Pressure
Popping pressure is the value of increasing inlet
static pressure at which the disc moves in the
opening direction at a faster rate as compared
with corresponding movement at higher or lower
pressures. It applies only to safety or safety relief
valves on compressible fluid service.
•
Pressure Containing Membe
r
A pressure containing member of a safety valve is a
part which is in actual contact with the pressure media
in the protected vessel.
•
Pressure Retaining Member
A pressure retaining member of a safety valve is a part
which is stressed due to its function in holding one or
more pressure containing members in position.
•
Rated Lift
Rated lift is the design lift at which a valve attains its
rated relieving capacity.
•
Safety Valve
A safety valve is a pressure relief valve actuated
by inlet static pressure and characterized by rapid
opening or pop action.
•
Set Pressure
Set pressure is the value of increasing inlet static
pressure at which a safety valve displays the
operational characteristics as defined under “Popping
Pressure.” It is one value of pressure stamped on the
safety valve.
•
Seat
A seat is the pressure containing contact between the
fixed and moving portions of the pressure containing
elements of a valve.
•
Seat Diameter
Seat diameter is the smallest diameter of contact
between the fixed and moving members of the
pressure containing elements of a valve.
•
Seat Tightness Pressure
Seat tightness pressure is the specific inlet static
pressure at which a quantitative seat leakage test is
performed in accordance with a standard procedure.
•
Simmer
Simmer is the audible or visible escape of fluid
between the seat and disc at an inlet static pressure
below the popping pressure and at no measurable
capacity. It applies to safety valves on compressible
fluid service.
•
Warn
See “Simmer” (definition above).