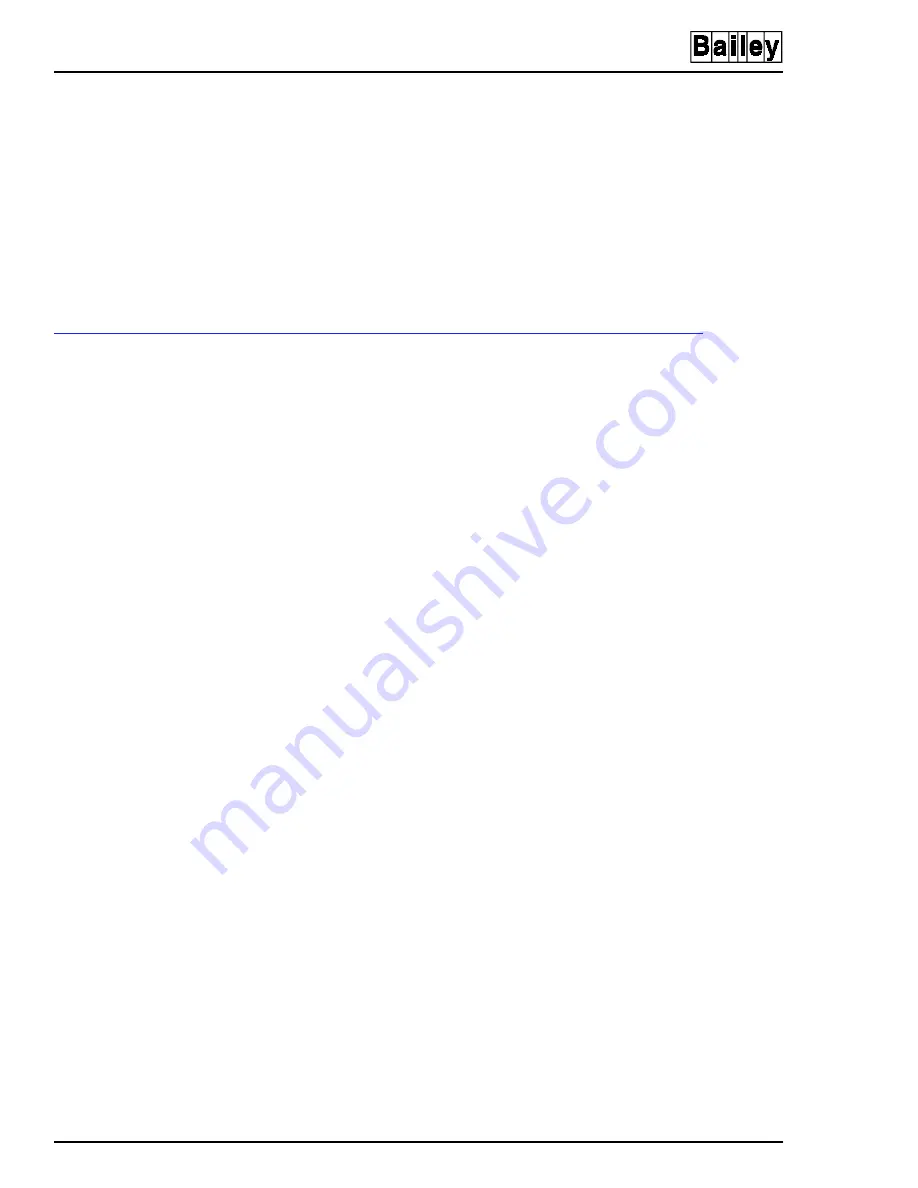
DESCRIPTION AND OPERATION
2 - 4
I-E96-217A
®
modules. The MFT is a one-shot timer that is reset periodically
by the CPU. A
time out
:
•
Resets the microprocessor.
•
Disables the module bus interface circuit.
•
Disables the Clear To Send (CTS) handshaking output.
Refer to
in this section for further
explanation of
time out
.
I/O Interface Functions
Commands from a computer are directed to the microproces-
sor through the RS-232C serial port interface circuits. Module
bus data transfer between the SPM and an addressed module
is controlled by the module bus interface circuits. The CPU
block directs these functions.
Module Bus Interface
Block
The module bus interface used by the SPM consists of a bus
driver circuit, control register and Universal Asynchronous
Receiver/Transmitter (UART). The microprocessor directs the
module bus interface functions through the control register.
This circuitry allows the SPM to communicate with other INFI
90 modules that have the same basic module bus interface cir-
cuitry.
The different data and command messages transmitted serially
on the module bus vary in length (i.e., number of bytes). An
open collector bus driver circuit is the receive and transmit
point for these serial module bus messages entering or leaving
the SPM.
A UART performs serial to parallel and parallel to serial conver-
sion on data received or transmitted by the SPM. UART data
registers hold this data during a microprocessor initiated
transmit or receive sequence. The UART adds the required data
format framing bits to messages it transmits, and checks and
removes these bits from received messages. The data format
(i.e., number of start bits, data bits and stop bits and type of
parity) is fixed for module bus messages. The UART uses a
clock signal from the frequency divider network to transmit
serial data at 83.3 Kbaud, and to synchronize received serial
data.
RS-232C Serial Port
Interface
The RS-232C serial port interface block consists of two ACIA
circuits and related circuitry, and a frequency multiplier cir-
cuit. These circuits provide the port interface functions and
allow other peripheral equipment having RS-232C port capa-
bility to connect and communicate with the SPM.