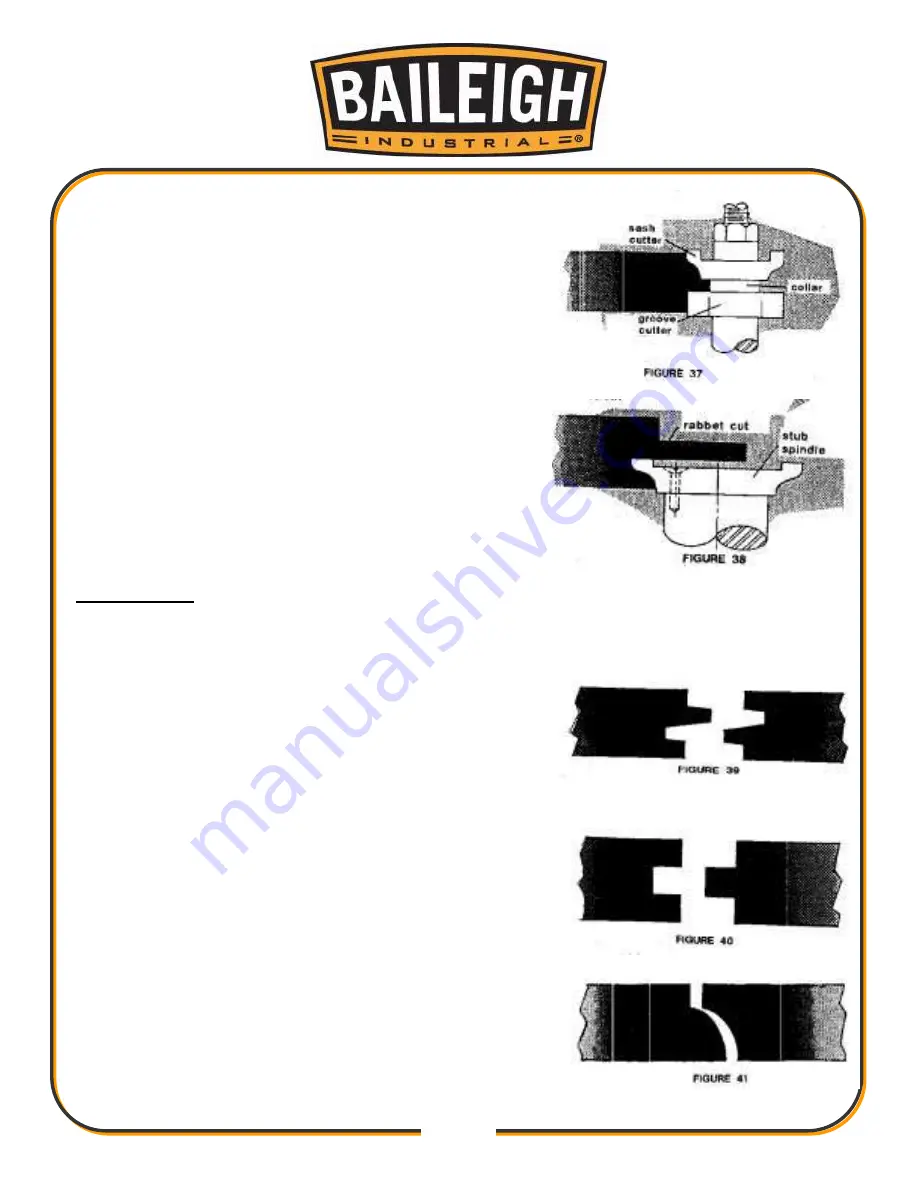
32
32
Figure 37 shows the first shaping out for a window-sash
stile utilizing a sash cutter, collar, collar, and a 1/2" groove
cutter.
Figure 38 shows both cuts required for a window-sash rail
end. The first operation at top is a rabbet cut made with a
groove cutter. The second operation is performed with a
stub spindle and butt head screw.
BUTT JOINTS
All butt type joints require both workpieces to be perfectly square and straight-edged.
Glue Butt Joint: To perform a glue butt joint, both fences
are kept in-line and adjusted for a depth of cut as shown in
Figure 39.
The cuts on both workpieces are part-edge cuts which do
not reduce the stock width during the cutting procedure.
When shaping the two workpieces, one is fed top-side up;
the other is fed bottom-side up.
Tongued Joint : Similar to the glue joint, both fences are
kept in-line for the tongued joint and adjusted for a 1/4"
depth of cut with no reduction in stock width. With this joint,
however, both workpieces are fed with the same side up as
shown in Figure 40.
As shown in Figure 41, the leaf workpiece is shaped with a
drop Leaf Bead cutter; the table workpiece is shaped with a
Drop Leaf Cove cutter. With this type joint, the whole edge
of both workpieces is shaped, same side up, and allowance
made for a 1/16" reduction in width. Adjust the infeed fence
to reduce the workpiece width by 1/16", and adjust the
outfeed fence to compensate for stock removed.
Summary of Contents for SS-3528
Page 39: ...36 36 EXPLODED VIEM STAND ASSEMBLY...
Page 41: ...38 38 EXPLODED VIEW SPINDLE...
Page 43: ...40 40 EXPLODED MOTOR AND SPINDLE BASE...
Page 46: ...43 43 EXPLODED HOOD ASSEMBLY...
Page 48: ...45 45 ELECTRICAL SCHEMATIC...
Page 49: ...46 46 NOTES...
Page 50: ...47 47 NOTES...
Page 51: ...48 48 NOTES...