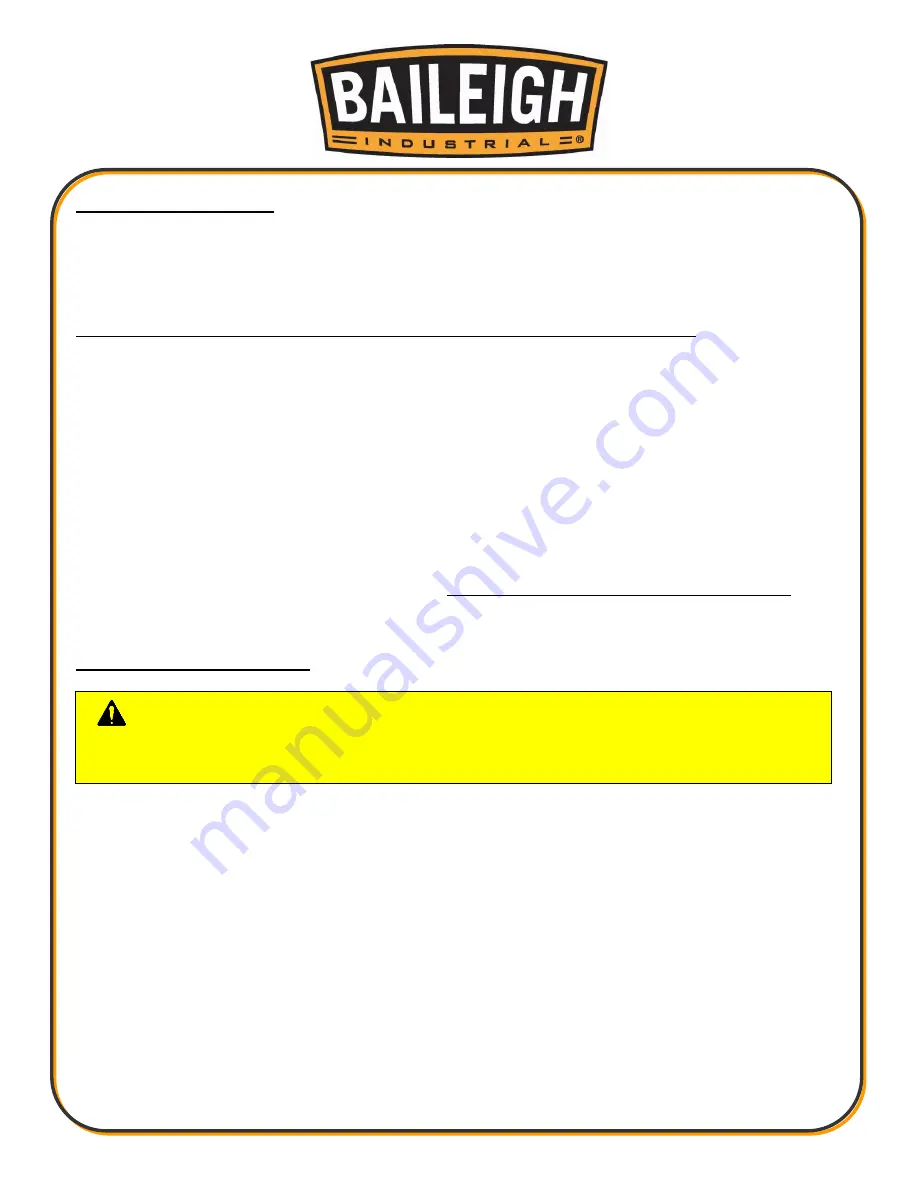
23
23
BLADE BREAKAGE
In some cases blade breakage is unavoidable due to the stresses that are imparted on the
blade. Avoidable breakage is often the result of poor care, or poor operator judgment when it
comes to adjusting or mounting the blade or blade guides.
Listed below are some of the more common reasons for blade breakage.
•
Top blade guide assembly is set too high above the piece part.
•
The blade is tensioned incorrectly.
•
Piece part is fed into the blade too quickly.
•
Blade teeth are dull or broken.
•
Blade is not properly aligned with the guides.
•
Forcing a large width blade to cut a small radius.
•
Using a blade with an improperly finished weld joint.
•
Allowing the blade to run when not in use. (
NEVER
leave an unattended blade running.)
MATERIAL SELECTION
When selecting materials keep these instructions in mind:
•
Material must be clean and dry. (without oil)
•
Material should have a smooth surface so it processes easily.
•
Dimensional properties of material must be consistent and not exceed the machine capacity
values.
•
Chemical structure of material must be consistent.
•
Buy certificated steel from the same vendor when possible.
CAUTION:
It must be determined by the customer that materials being
processed through the machine are NOT potentially hazardous to operator or
personnel working nearby.
Summary of Contents for BS-916M
Page 3: ...ELECTRICAL COMPONENTS 44 ELECTRICAL SCHEMATIC 46...
Page 15: ...12 12 GETTING TO KNOW YOUR MACHINE A G E D C F B H I J K L N P Q O M S T U V W X R...
Page 37: ...34 34 PARTS DIAGRAM...
Page 38: ...35 35...
Page 48: ...45 45...
Page 49: ...46 46 ELECTRICAL SCHEMATIC...
Page 50: ...47 47 NOTES...
Page 51: ...48 48 NOTES...