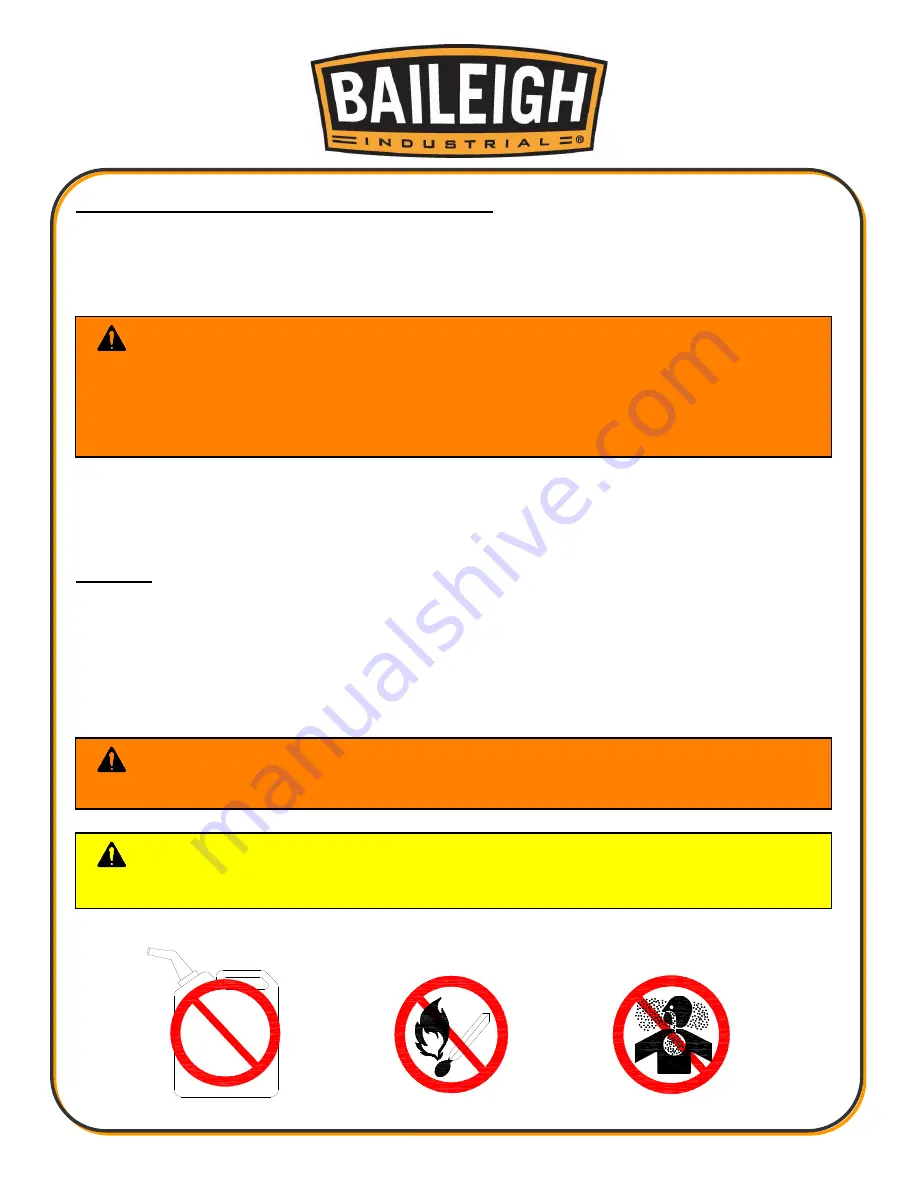
9
9
UNPACKING AND CHECKING CONTENTS
Your Baileigh machine is shipped complete in one crate. Separate all parts from the packing
material and check each item carefully. Make certain all items are accounted for before
discarding any packing material.
Cleaning
Your machine may be shipped with a rustproof waxy oil coating and grease on the exposed
unpainted metal surfaces. To remove this protective coating, use a degreaser or solvent
cleaner. For a more thorough cleaning, some parts will occasionally have to be removed.
DO
NOT USE
acetone or brake cleaner as they may damage painted surfaces.
Follow manufacturer’s label instructions when using any type of cleaning product. After cleaning,
wipe unpainted metal surfaces with a light coating of quality oil or grease for protection.
WARNING:
SUFFOCATION HAZARD! Immediately discard any plastic
bags and packing materials to eliminate choking and suffocation hazards to children
and animals.
If any parts are missing, do not plug in the power cable, or turn the power switch on
until the missing parts are obtained and installed correctly.
WARNING:
DO NOT USE gasoline or other petroleum products to clean
the machine. They have low flash points and can explode or cause fire.
CAUTION:
When using cleaning solvents work in a well-ventilated area.
Many cleaning solvents are toxic if inhaled.
GAS
Summary of Contents for BS-916M
Page 3: ...ELECTRICAL COMPONENTS 44 ELECTRICAL SCHEMATIC 46...
Page 15: ...12 12 GETTING TO KNOW YOUR MACHINE A G E D C F B H I J K L N P Q O M S T U V W X R...
Page 37: ...34 34 PARTS DIAGRAM...
Page 38: ...35 35...
Page 48: ...45 45...
Page 49: ...46 46 ELECTRICAL SCHEMATIC...
Page 50: ...47 47 NOTES...
Page 51: ...48 48 NOTES...