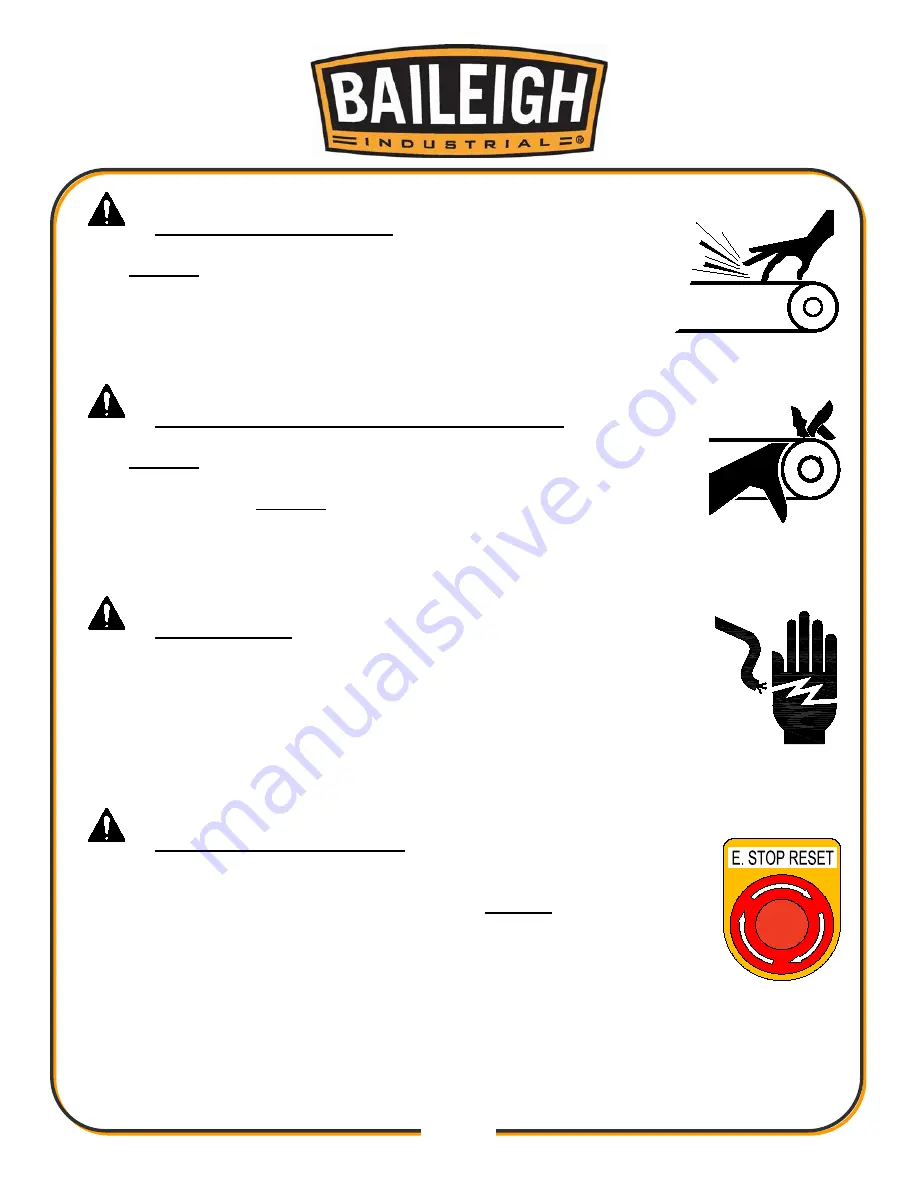
6
6
MOVING BELT ABRASIONS
DO NOT
place hands or fingers near, or in contact with sanding
belt during operation.
MOVING BELTS CAN CRUSH AND DISMEMBER
DO NOT
allow fingers to get pinched between belt and belt rollers.
This may pull the operator’s hand into the machine causing serious
personal injury.
DO NOT
operate without guards in place.
HIGH VOLTAGE
USE CAUTION IN HIGH VOLTAGE AREAS. DO NOT
assume the
power to be off.
FOLLOW PROPER LOCKOUT PROCEDURES.
EMERGENCY STOP BUTTON
In the event of incorrect operation or dangerous conditions, the machine
can be stopped immediately by pressing the
E-STOP
button. Twist the
emergency stop button clockwise (cw) to reset. Note: Resetting the E-
Stop will not start the machine.