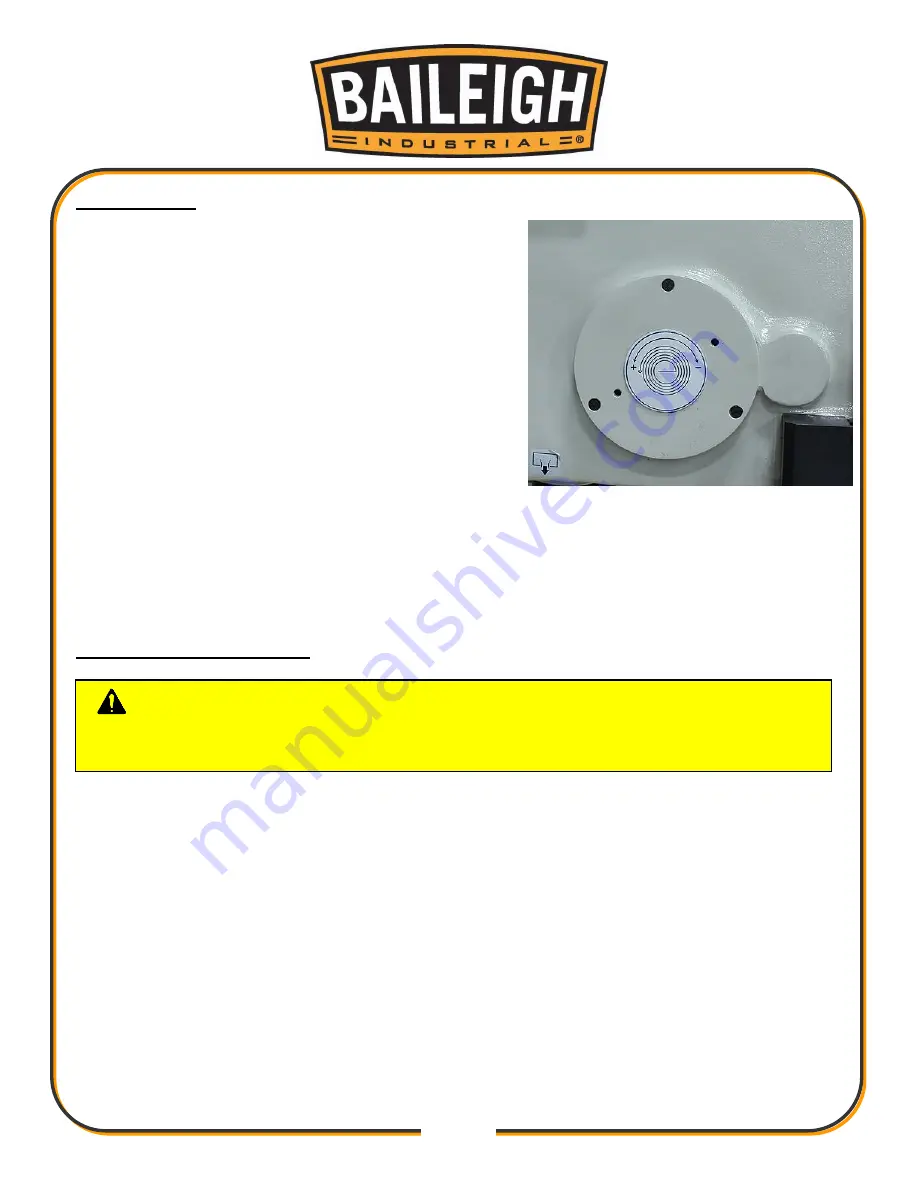
32
32
Return Spring
The return spring should provide enough tension to
fully lift the spindle and any tooling easily and without
slamming up to a stop.
1. Turn the main disconnect Off.
2. Allow the quill to be fully retracted.
3. Do not remove the spring cover.
4. Remove the three cover screws, but do not remove
the cover.
5. Rotate the cover as indicated by the arrow to either
increase or decrease the spring tension.
6. When the spring tension is just enough to fully retract the quill and its tooling, turn the cover
1/3 of a turn more and install and tighten the cover screws.
7. If the retract spring requires replacement, follow the diagram on the cover to set the correct
winding directions.
MATERIAL SELECTION
When selecting materials keep these instructions in mind:
•
Material must be clean and dry. (without oil)
•
Material should have a smooth surface so it processes easily.
•
Dimensional properties of material must be consistent and not exceed the machine capacity
values.
•
Chemical structure of material must be consistent.
•
Buy certificated steel from the same vendor when possible.
CAUTION:
It must be determined by the customer that materials being
processed through the machine are NOT potentially hazardous to operator or
personnel working nearby.
Summary of Contents for DP-1850G
Page 16: ...13 13...
Page 22: ...19 19 GETTING TO KNOW YOUR MACHINE...
Page 36: ...33 33 DRILL HEAD PARTS DIAGRAM...
Page 37: ...34 34 Detail 1...
Page 38: ...35 35 Detail 2...
Page 39: ...36 36 Detail 3...
Page 45: ...42 42 COLUMN BASE PARTS DIAGRAM...
Page 48: ...45 45 ELECTRICAL SCHEMATIC...
Page 49: ...46 46...