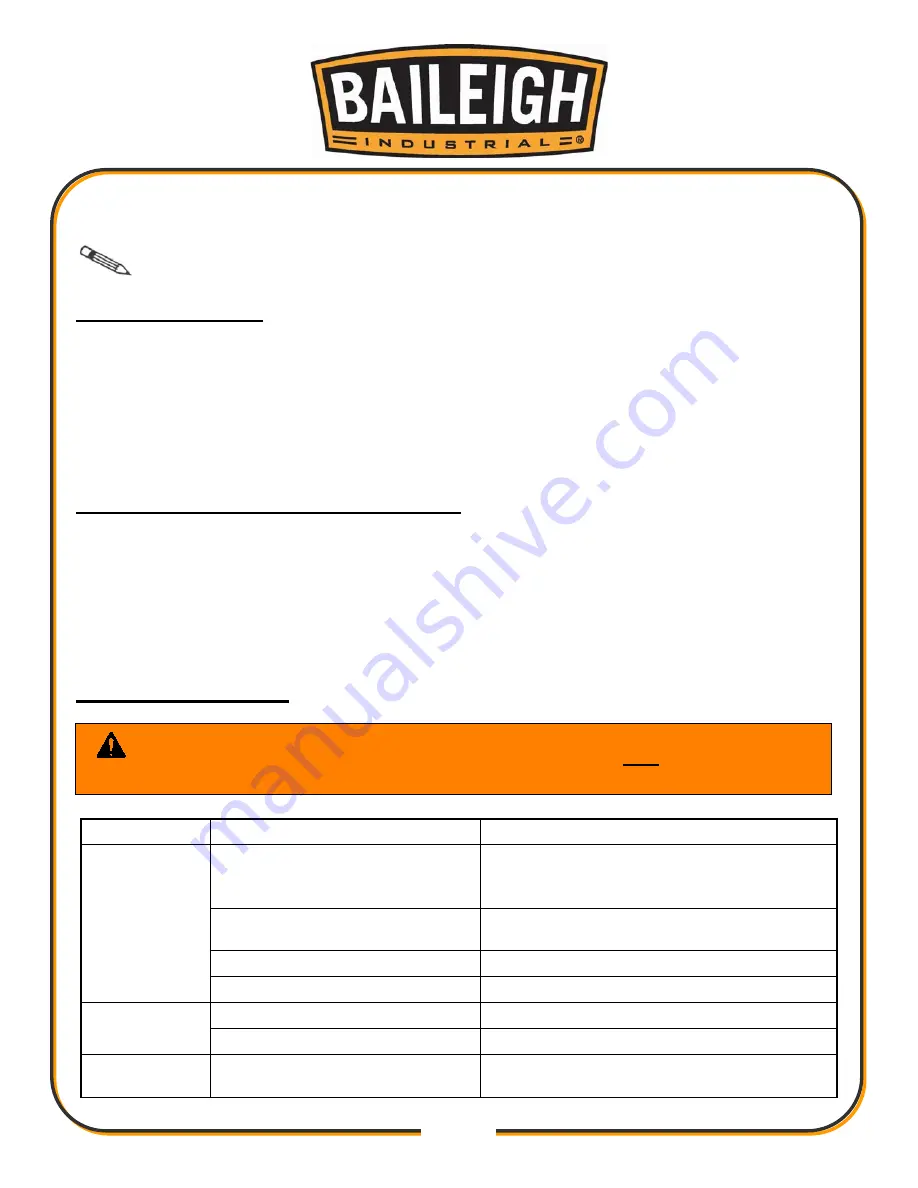
27
27
•
Inspect regularly for tension and wear. Check pulleys to ensure that they are properly
aligned.
Note: Proper maintenance can increase the life expectancy of your machine.
Greasing the Machine
1. Grease the gear rack on the column to keep the table moving smoothly.
7. Lubricate the spline of the spindle and the teeth of the rack with a #2 grease.
8. Fully extend the spindle and lightly grease the spindle shaft.
9. A coat of automotive type paste wax applied to the table and column will help to keep the
surfaces clean.
Storing Machine for Extended Period of Time
If the Drill Press is to be inactive for a long period of time, prepare the machine as follows:
•
Detach the plug from the electrical supply panel.
•
Clean and grease the machine.
•
Cover the machine.
TROUBLESHOOTING
Trouble
Probable Cause
Remedy
Spindle does
not run
Motor overload protector tripped
Let the motor cool down, and the overheat
switch would be reset by itself, then push
the start button.
Caused by chuck guard
adjustment
Adjust / Close the chuck guard.
Defective switch.
Replace switch.
Broken drive belt.
Replace drive belt.
Spindle noisy.
Damaged spindle bearings
Replace bearings.
Worn spline.
Replace spline.
Drill stalls.
Worn drive belt.
Check condition of belt. Replace if glazed
or slipping on pulleys.
WARNING:
Make sure the electrical disconnect is OFF before working on
the machine.